Understanding Level Measurement Tools Precision in Liquid and Solid Material Management
In the realm of industrial processes, accurate measurement of material levels in containers, tanks, silos, or any holding vessel is paramount to ensuring efficient operations, safety, and cost-effectiveness. Level measurement tools play a pivotal role in monitoring and controlling inventory, preventing overflows or running dry situations, and optimizing process control. With advancements in technology, a myriad of level measurement techniques have emerged, catering to diverse applications across industries, from chemical plants to food processing units. This article delves into the significance of level measurement, explores various types of measurement tools, and highlights their unique advantages.
**The Significance of Accurate Level Measurement**
Precise level measurement is crucial for several reasons. Firstly, it enables efficient inventory management, allowing industries to maintain optimal stock levels and avoid unnecessary downtime due to stockouts or overstocking. Secondly, it contributes to process control and automation, ensuring that reactions, mixtures, or storage conditions are precisely regulated. Safety is another vital aspect; incorrect level measurements can lead to spills, overpressurization, or even explosions in extreme cases. Lastly, accurate measurements aid in enhancing product quality and reducing waste, thereby positively impacting the bottom line.
**Types of Level Measurement Tools**
Level measurement tools can be broadly classified into four categories based on their operating principles direct contact, non-contact, continuous, and point level measurement devices.
1. **Direct Contact Methods** These involve sensors or probes coming into direct contact with the measured medium. Common examples include float & tape, capacitance probes, and displacers. Float & tape systems are simple and reliable, suitable for large tanks, while capacitance probes detect changes in capacitance between electrodes to measure levels of liquids or solids. Displacer-type transmitters use the buoyancy principle for high-accuracy liquid level measurement.
2. **Non-Contact Methods** These employ technologies like ultrasonic, radar, or laser to measure levels without physical contact **Non-Contact Methods** These employ technologies like ultrasonic, radar, or laser to measure levels without physical contact
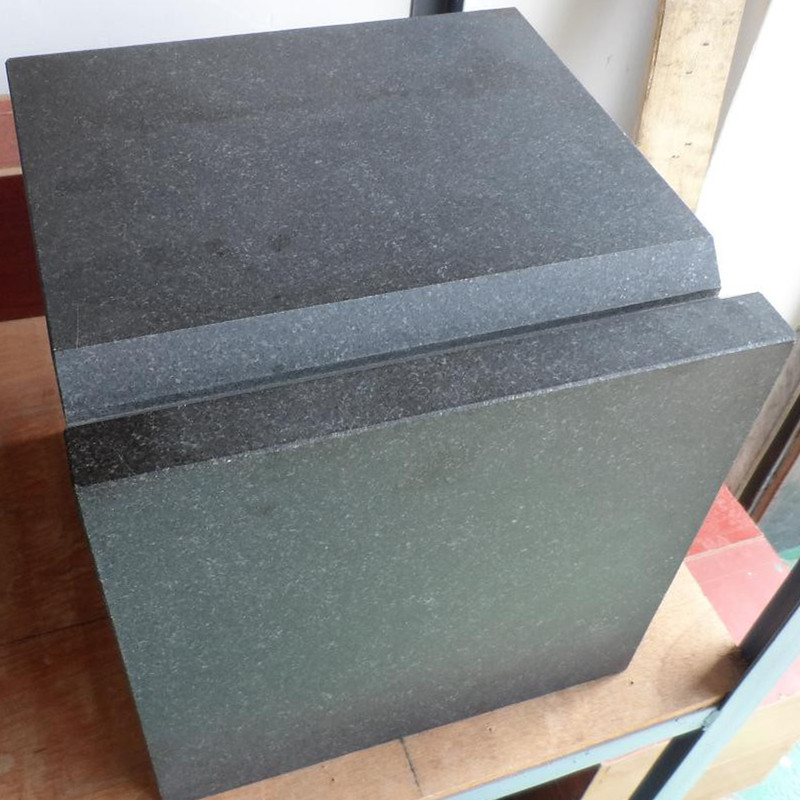
**Non-Contact Methods** These employ technologies like ultrasonic, radar, or laser to measure levels without physical contact **Non-Contact Methods** These employ technologies like ultrasonic, radar, or laser to measure levels without physical contact
level measurement tool. Ultrasonic level meters send sound waves that reflect off the surface and calculate the distance to determine the level. Radar level transmitters use high-frequency electromagnetic waves, capable of penetrating vapor or dust layers, making them ideal for harsh environments. Laser-based systems offer high accuracy and are often used in applications requiring extreme precision.
3. **Continuous Level Measurement** As the name suggests, these tools provide continuous level data, enabling real-time monitoring and control. They encompass a wide range, including guided wave radar (GWR), which uses a probe guided along the tank's length, transmitting electromagnetic pulses to measure level, and time-of-flight methods employed by radar and ultrasonic systems.
4. **Point Level Measurement** These devices signal when a predetermined level has been reached, often used as alarms to prevent overfills or empty conditions. Technologies range from basic mechanical switches (like float switches) to more advanced electronic sensors like vibrating fork sensors, which detect changes in vibration frequency when the medium comes into contact with the forks.
**Selecting the Right Tool for the Job**
Choosing the appropriate level measurement tool depends on factors such as the type of material being measured (liquid, solid, granular), its properties (viscosity, conductivity, density), the environment (temperature, pressure, corrosivity), and the required accuracy and response time. For instance, non-contact radar is preferred in high-temperature or pressurized vessels, while capacitance probes excel in measuring interfaces between two immiscible liquids.
**Conclusion**
Accurate level measurement is an indispensable part of modern industrial processes, directly influencing efficiency, safety, and profitability. The array of level measurement tools available ensures that there's a solution tailored to every application's specific needs. Whether it's a simple point level switch for a small tank or a sophisticated radar system for a large silo, understanding the strengths and limitations of each technology is key to implementing effective level control strategies. As technology advances, we can expect even more innovative and precise measurement solutions to emerge, further enhancing process control capabilities across industries.