The Importance of Granite Inspection Tables in Quality Control
Granite inspection tables, also known as granite surface plates, are indispensable tools in the world of precision engineering and manufacturing. These tables, made from high-quality granite material, serve as an essential element in ensuring accuracy and consistency in various inspection and measurement processes.
Granite, with its inherent properties of rigidity, stability, and thermal non-expansion, makes for an ideal base for inspection tasks. Its low coefficient of thermal expansion minimizes the effects of temperature changes on measurements, providing a reliable platform even in fluctuating conditions. This characteristic is particularly crucial in industries where minute variations can significantly impact product quality, such as aerospace, automotive, and electronics.
The inspection table's surface is meticulously polished to achieve an ultra-smooth finish, allowing for precise measurements. The table's flatness, parallelism, and straightness are meticulously checked to ensure they meet stringent industry standards. This level of precision is vital for tasks that require the alignment, fitting, or comparison of parts, making granite inspection tables indispensable in quality control processes.
Moreover, granite's natural resistance to wear and corrosion enhances the longevity of these tables. They can withstand the harsh chemicals and abrasives used in cleaning and maintenance, ensuring consistent performance over time. This durability translates into cost-effectiveness for businesses, as they do not need frequent replacements or repairs This durability translates into cost-effectiveness for businesses, as they do not need frequent replacements or repairs
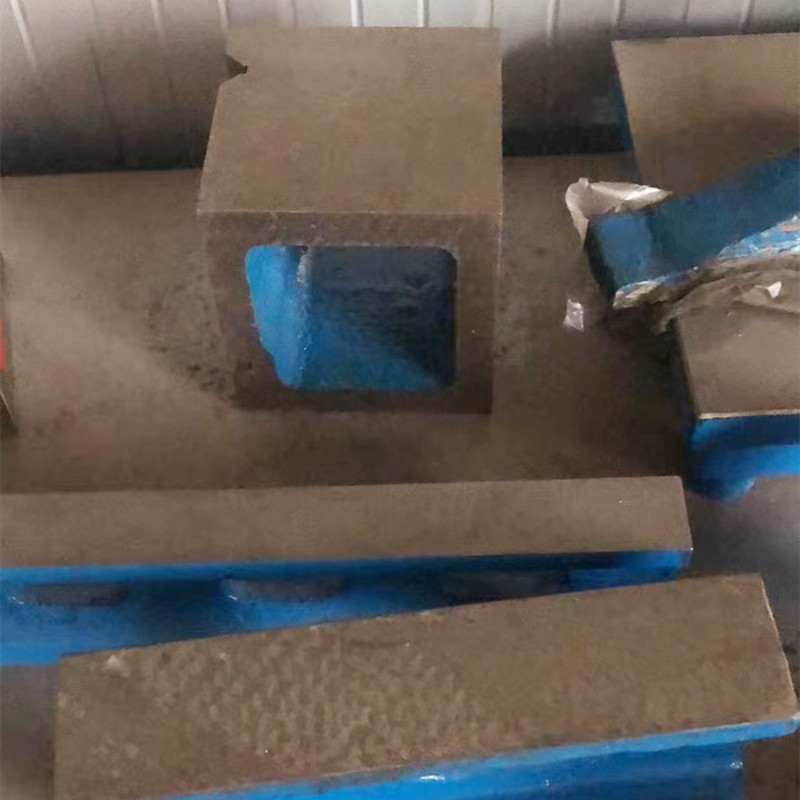
This durability translates into cost-effectiveness for businesses, as they do not need frequent replacements or repairs This durability translates into cost-effectiveness for businesses, as they do not need frequent replacements or repairs
granite inspection table.
In addition to their functional attributes, granite inspection tables also contribute to a cleaner and safer working environment. Unlike metal surfaces, granite does not generate magnetic fields, which could interfere with sensitive electronic devices. Furthermore, it is less prone to scratches and dents, reducing the risk of accidents or damage to workpieces.
The use of granite inspection tables extends beyond traditional manufacturing. In the field of research and development, they are used for calibration purposes, ensuring the reliability of experimental data. In education, they provide a practical learning tool for students to understand the principles of metrology and precision engineering.
In conclusion, granite inspection tables play a pivotal role in maintaining the highest levels of quality and precision in various industries. Their robustness, accuracy, and longevity make them a valuable investment for companies seeking to uphold stringent quality control measures. By leveraging the benefits of granite inspection tables, businesses can enhance their manufacturing processes, minimize errors, and ultimately deliver products of unparalleled quality to their customers.