The Importance of Metal Measuring Tools in Precision Engineering
In the world of precision engineering, metal measuring tools play an indispensable role in ensuring accuracy and quality in manufacturing processes. These tools are the backbone of industries ranging from automotive to aerospace, where minute deviations can lead to significant consequences.
Metal measuring tools are designed to measure various attributes of metallic components such as length, thickness, diameter, flatness, and surface finish. They are vital for maintaining the integrity of the manufacturing process, ensuring that products meet stringent industry standards and client specifications.
One of the most common metal measuring tools is the caliper, available in digital and analog forms. It measures both internal and external dimensions with great precision. Micrometers, another essential tool, offer even higher accuracy, capable of measuring fractions of a millimeter. They are particularly useful in measuring thickness, depth, and outside diameter of metals.
Height gauges, on the other hand, are used to measure the height of metal components or the distance between two points. They are crucial in applications where vertical measurements are critical. Optical comparators, meanwhile, project an enlarged image of a metal part onto a screen, allowing for visual inspection and precise measurement of complex shapes and sizes.
Surface roughness testers gauge the texture of a metal's surface, which significantly affects its performance and wear resistance. Hardness testers, another key tool, determine the strength and durability of a metal by measuring its resistance to indentation Hardness testers, another key tool, determine the strength and durability of a metal by measuring its resistance to indentation
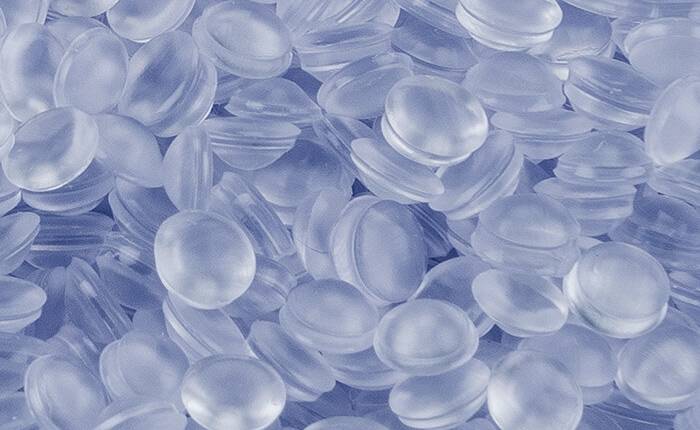
Hardness testers, another key tool, determine the strength and durability of a metal by measuring its resistance to indentation Hardness testers, another key tool, determine the strength and durability of a metal by measuring its resistance to indentation
metal measuring tools.
In addition to these, there are countless specialized tools like thread gauges, bore gauges, and angle finders, each tailored to specific measurement requirements. These tools not only ensure dimensional accuracy but also contribute to quality control, defect detection, and process optimization.
The importance of metal measuring tools extends beyond the production floor. They facilitate quality assurance, helping manufacturers adhere to international standards like ISO and ASME. They also aid in R&D, enabling engineers to test and refine designs before mass production.
However, the effectiveness of these tools depends on their calibration and maintenance. Regular checks and timely calibration ensure consistent and reliable results, minimizing errors and preventing costly rework or product failures.
In conclusion, metal measuring tools are the unsung heroes of the engineering world. Their precision and reliability are fundamental to producing high-quality metal components, driving innovation, and maintaining the stringent standards of modern industries. As technology advances, so do these tools, becoming more sophisticated and accurate, further enhancing the precision and efficiency of metalworking processes.