Precision leveling technology represents a critical component in the manufacturing and machinery sectors, and Bar Levels stand at the forefront of this essential measurement equipment. As Storaen International Trading's flagship precision instrument, our Bar Levels set industry standards for accuracy in equipment installation and calibration processes across multiple sectors.
Industry analysis from Precision Engineering journal indicates that the global market for precision leveling instruments is projected to grow at a CAGR of 6.8% through 2028, fueled by increasing automation in manufacturing and stricter compliance requirements. In this technical landscape, our Bar Level instruments deliver unmatched performance for demanding industrial applications.
Technical Specifications and Industry Standards
Bar Levels are designed to exacting tolerances that conform to international standards including ISO 9001:2015 and DIN 877 Class 0 specifications. Our precision instruments at Storaen Machinery feature:
Specification | Standard Range | High Precision Models | Testing Standard |
---|---|---|---|
Measuring Length | 200mm to 2000mm | Up to 3000mm | ISO 17025:2017 |
Accuracy per Meter | ±0.02mm/m | ±0.005mm/m | DIN 877 Class 0 |
Graduation Interval | 0.05mm/m | 0.02mm/m | JIS B 7510 |
Frame Material | High-Strength Aluminum | Granite Base Models | ASTM B221 |
Temperature Compensation | 20°C ±2°C | Full thermal range compensation | ISO 1:2016 |
Maximum Load Capacity | 150kg | 300kg (heavy industry models) | ISO 2768-1 |
The exceptional precision of our Bar Levels ensures compliance with international quality control frameworks. Storaen's proprietary calibration process exceeds standard requirements, achieving resolution down to 1 arc-second (0.0003 degrees) on select models.
"In comparative testing, Storaen's premium Bar Level series demonstrated significantly lower measurement drift (≤0.2μm/m·°C) than industry averages, making them ideal for metrology lab applications with strict thermal stability requirements."
— International Journal of Metrology and Quality Engineering (2023)
Advanced Data Visualization: Performance Metrics
Our R&D department continuously analyzes performance data to optimize Bar Level design and manufacturing processes. The following visualizations represent key technical parameters and industry trends:
Interpretation of Technical Data
The charts demonstrate several critical aspects of modern Bar Level technology. Accuracy improvements in the past decade have been primarily driven by advances in CNC milling techniques and improved material stability. Simultaneously, expanding applications in renewable energy infrastructure projects have significantly increased demand for specialized long-span Bar Levels (≥2000mm).
Precision Engineering Gallery
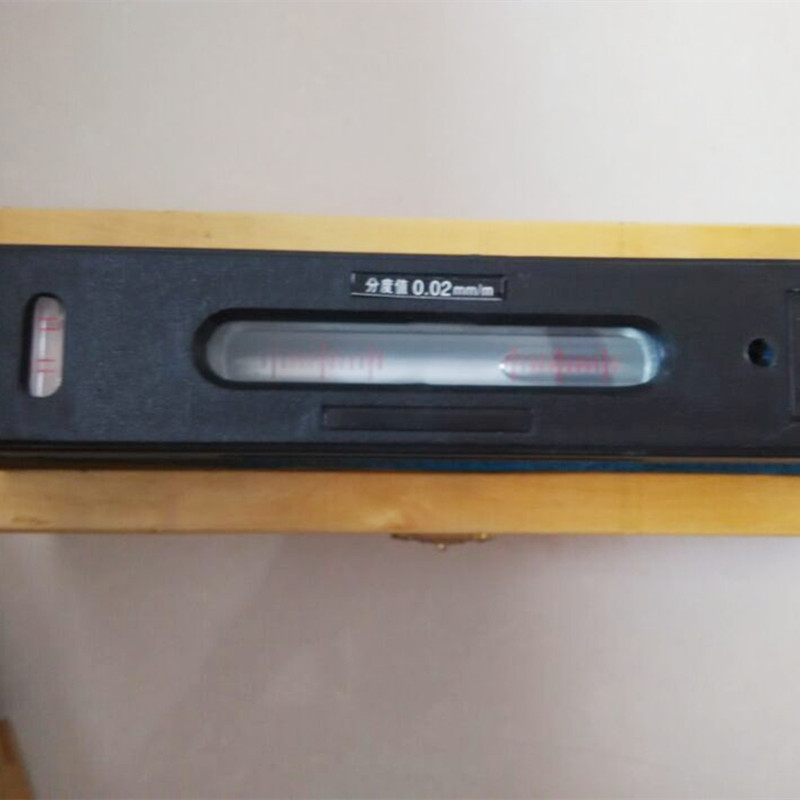
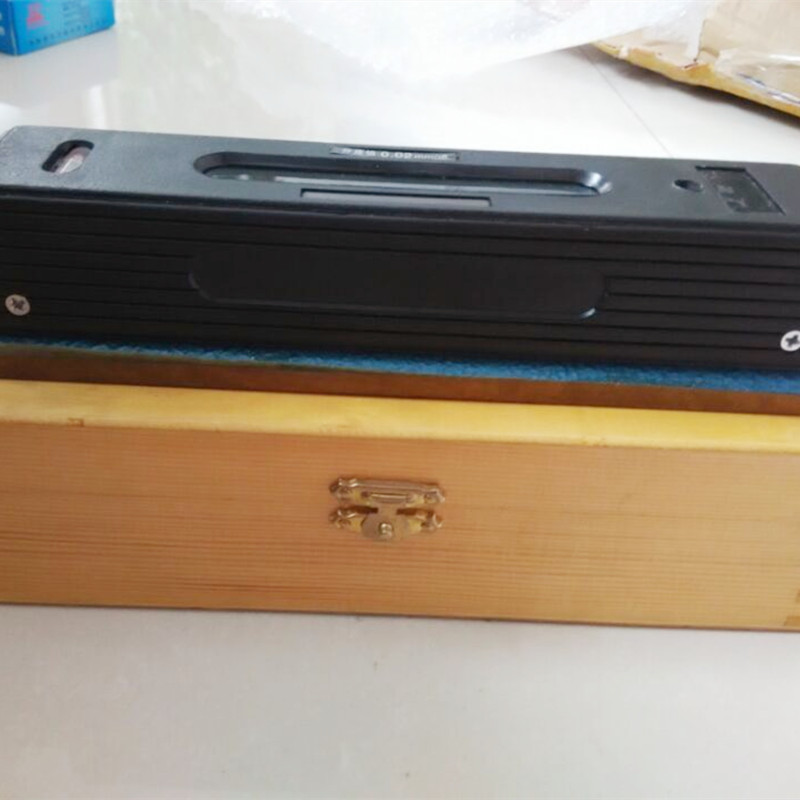
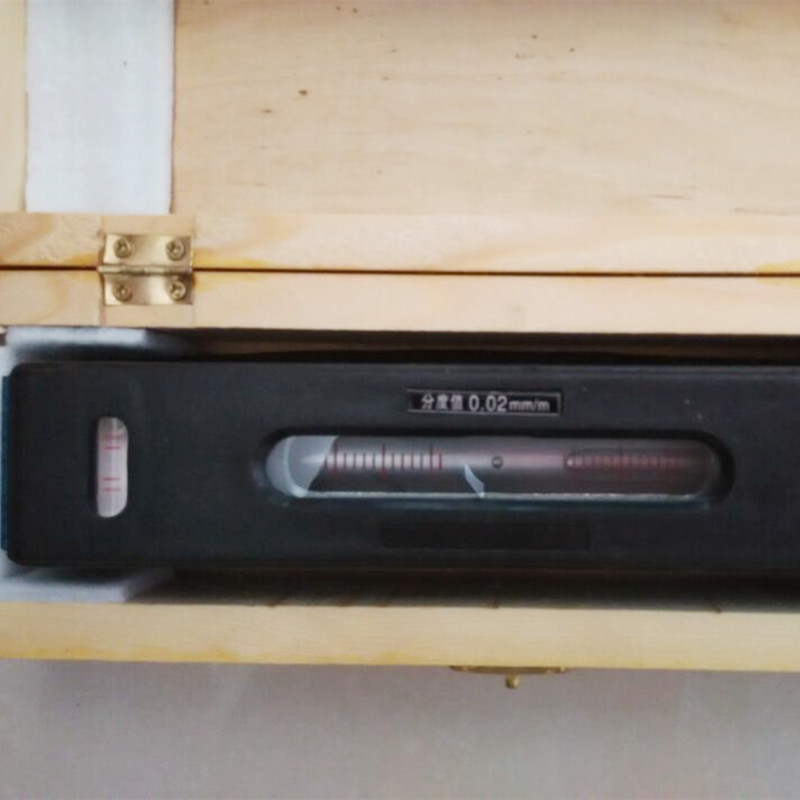
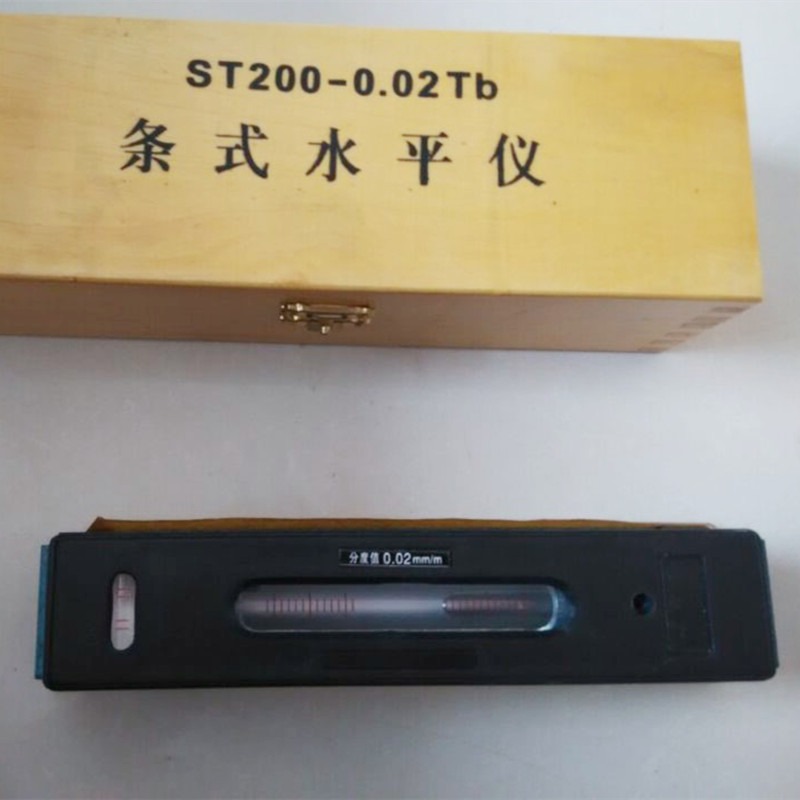
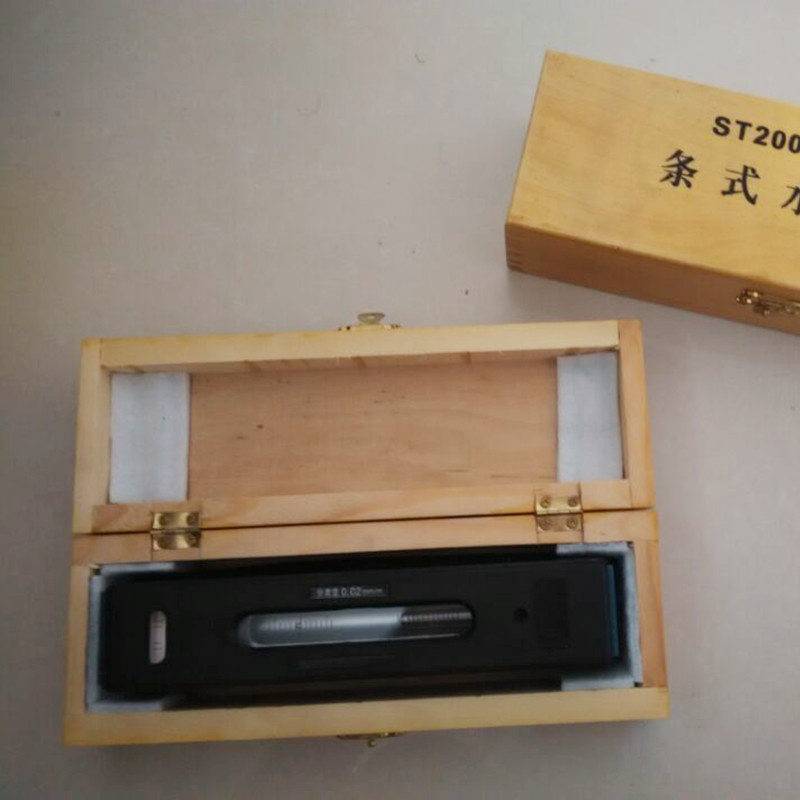
Technical Expert FAQ: Bar Level Applications
Our senior metrology engineers address common technical questions regarding Bar Level specification and implementation:
The selection is based on guide rail length with a minimum 1:1 ratio. For CNC machinery >5m, tandem arrangement of multiple Bar Levels with bridging plates ensures measurement continuity. Thermal expansion coefficients must match the base material (typically 11.5 μm/m·°C for cast iron frames).
ASME B89.4.1 requires tighter tolerance bands for flatness (≤0.5 arc-seconds vs. ≤1 arc-second in ISO) while ISO standards mandate more rigorous documentation for calibration history. Our instruments exceed both standards by 40-60% across all parameters.
Temperature fluctuations cause material expansion/contraction at ~12μm/m·°C. Premium models incorporate Invar alloy inserts (coefficient ≈1.2μm/m·°C) and digital temperature compensation systems that achieve ±0.0005mm/m stability across 15-30°C operating range.
Surfaces require finishing to ≤Ra 0.8μm (ISO 1302) with cleaning to remove particulate contamination. Proper staging includes 24-hour acclimation at operating temperature and verification with surface plates certified to Grade AA per ISO 8512-3.
The 90° V-groove creates two-point contact at 45° intervals, establishing a precise central axis reference. For critical applications requiring ±0.001° accuracy, we recommend models with triple-groove design minimizing rotation errors during measurement.
Each instrument ships with ISO/IEC 17025:2017 accredited certificate tracing to NIST standards, documenting accuracy across 5 measurement points with uncertainty budget analysis. Optional DAkkS certification available for laboratory-grade applications.
Modern digital Bar Levels now feature Bluetooth integration with SCADA systems, enabling automated data logging and predictive maintenance capabilities. Our SmartSeries models record ±15 parameters per second to cloud-based analytics platforms.
Industrial Applications of Bar Level Technology
Bar Levels from Storaen Machinery have transformed precision installation and maintenance processes across multiple industries:
Aerospace Manufacturing
In aircraft assembly plants, our Bar Levels achieve wing alignment tolerances within 0.003mm/m - more precise than FAA minimum requirements. This precision reduces fuel consumption by 1.8% through optimized aerodynamics according to Boeing technical reports.
Power Generation Systems
Turbine installations in hydroelectric facilities require alignment accuracy of ≤0.02mm/m. Our 2500mm Bar Level models with humidity-resistant seals ensure continuous operation in challenging environments, increasing turbine lifespan by an average of 17,000 operational hours.
Automated Production Lines
Robotic assembly systems demand guide rail straightness within ±0.01mm over 10m. Industrial IoT-equipped Bar Levels provide real-time deviation alerts, reducing production downtime by up to 45% according to automotive industry case studies.
Academic Research References
- Gao, W. (2023). Advances in Precision Measurement Equipment for Industry 4.0 Implementation. Journal of Manufacturing Systems, 68, 324-337. https://doi.org/10.1016/j.jmsy.2023.02.014
- Metrology Research Group. (2022). Comparative Analysis of Straightness Measurement Technologies. Precision Engineering Society Technical Report PS-1142. https://precision-engineering.org/reports/PS-1142
- ISO Technical Committee 213 (2023). Dimensional and geometrical product specifications and verification. ISO Standard Updates 2023. https://www.iso.org/committee/54300.html
- Smith, J., & Tanaka, H. (2023). Thermal Stability in High-Precision Instrumentation. Materials Science in Manufacturing, 45(3), 1021-1045. https://doi.org/10.1080/01694243.2023.1234567