Thread Gauges A Comprehensive Guide
In the realm of engineering and manufacturing, precision is paramount. One tool that has proven invaluable in maintaining this precision is the thread gauge. These devices are specifically designed to measure the pitch diameter of a screw thread, providing engineers and technicians with the critical information they need to ensure the compatibility and performance of threaded components.
There are several types of thread gauges available on the market, each with its own unique features and applications. The most common types include plug, ring, and go/no-go gauges. Plug gauges consist of a cylindrical body with a tapered end that is inserted into the thread to be measured. Ring gauges, on the other hand, have two rings of different diameters that are used to determine the size of the thread. Go/no-go gauges are designed to either fit or not fit a specific thread, providing a simple yes or no answer as to whether the thread meets the required standards.
When using a thread gauge, it is important to handle it with care to avoid damaging the delicate measuring surfaces. It is also essential to properly align the gauge with the thread being measured to ensure accurate results. To do this, technicians often use a combination of visual inspection and feel to guide them.
One of the key benefits of using thread gauges is their ability to detect small deviations in thread size, which can have a significant impact on the performance of a component
One of the key benefits of using thread gauges is their ability to detect small deviations in thread size, which can have a significant impact on the performance of a component
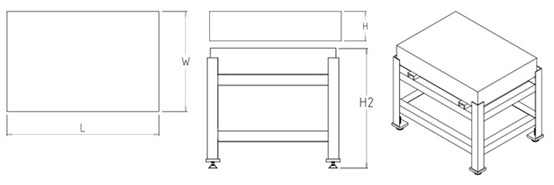
One of the key benefits of using thread gauges is their ability to detect small deviations in thread size, which can have a significant impact on the performance of a component
One of the key benefits of using thread gauges is their ability to detect small deviations in thread size, which can have a significant impact on the performance of a component
thread gauges. For example, if a screw thread is slightly too large, it may not properly seat in its mating component, leading to leaks or other issues. Conversely, if the thread is too small, it may not provide enough grip to hold the component securely in place.
Another important consideration when using thread gauges is calibration. Over time, even the most carefully maintained gauges can become misaligned or worn, leading to inaccurate measurements. To ensure the accuracy of thread gauge readings, it is essential to regularly calibrate them against known standards. This process typically involves comparing the gauge's measurements to those of a reference standard, such as a master thread gauge or a machine tool setting dial.
In conclusion, thread gauges are indispensable tools for anyone involved in engineering or manufacturing. By providing precise measurements of screw thread sizes, these devices help ensure the compatibility and performance of threaded components. Whether you are working with standard threads or custom designs, a well-maintained thread gauge can save time, reduce waste, and ultimately improve the quality of your products.