Surface Plate Calibration Ensuring Precision in Manufacturing
In the realm of precision engineering and manufacturing, the surface plate calibration stands as a cornerstone for maintaining accuracy in measurement and machining processes. This meticulous procedure ensures that the reference surfaces used in various industrial applications are true to their intended flatness, parallelism, and squareness, ultimately guaranteeing the high quality of finished products.
The process of surface plate calibration involves a series of steps designed to verify and correct any deviations from flatness that may have occurred over time or due to environmental factors such as temperature changes, vibration, or mishandling. Technicians typically employ specialized instruments like autocollimators, electronic levels, and laser interferometers to map the topography of the plate's surface and identify any high or low spots.
One common method is the reversal technique, where the measuring instrument is placed on the plate and then both the instrument and the plate are rotated 180 degrees. Any deviations detected are then averaged out, providing a clearer indication of the plate's actual flatness. Additionally, crossing levels at 90-degree angles can determine the plate’s squareness, while parallelism is checked by comparing measurements taken across opposite sides of the plate.
The importance of surface plate calibration cannot be overstated, as even minor discrepancies can lead to significant errors in the manufacturing process. For instance, if a surface plate used for machining operations is not accurately calibrated, it can result in misaligned parts or assemblies, affecting the product's performance and durability For instance, if a surface plate used for machining operations is not accurately calibrated, it can result in misaligned parts or assemblies, affecting the product's performance and durability
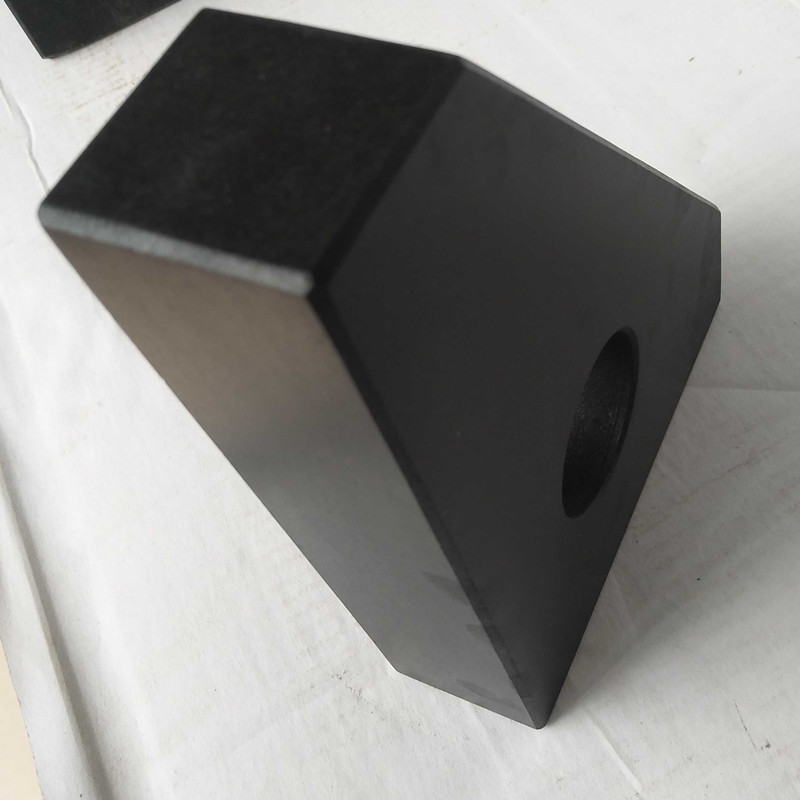
For instance, if a surface plate used for machining operations is not accurately calibrated, it can result in misaligned parts or assemblies, affecting the product's performance and durability For instance, if a surface plate used for machining operations is not accurately calibrated, it can result in misaligned parts or assemblies, affecting the product's performance and durability
surface plate calibration. In industries where exacting standards are paramount, such as aerospace and microelectronics, these inaccuracies can have catastrophic consequences.
Moreover, regular calibration serves a preventive function by identifying wear and tear before it becomes a critical issue. By catching imperfections early, maintenance can be scheduled proactively, avoiding costly downtime and extending the lifespan of the equipment. It also supports continuous improvement initiatives by offering data-driven insights into the working conditions of machinery and the environment they operate in.
In conclusion, surface plate calibration is an essential practice within the manufacturing sector, ensuring that tools and components meet stringent quality standards. Through precise measurement and correction, this process safeguards against inaccuracies that could compromise the integrity of end products. As technology advances and tolerances tighten, the art of surface plate calibration remains a vital skill, preserving the delicate balance between precision and performance in the world of manufacturing.