Calibrated Pin Gauges The Precision Tool for Dimensional Accuracy in Manufacturing
In the realm of precision engineering and manufacturing, calibrated pin gauges occupy a pivotal position as an indispensable tool for ensuring dimensional accuracy. These seemingly simple yet meticulously crafted instruments play a crucial role in quality control processes by providing a reliable means of verifying and measuring internal dimensions such as holes, slots, and recesses. This article delves into the significance, construction, usage, and maintenance of calibrated pin gauges, underscoring their importance in maintaining the highest standards of manufacturing excellence.
**Understanding Calibrated Pin Gauges**
Calibrated pin gauges, also known as go/no-go gauges or simply pin gauges, are cylindrical or tapered metal rods, meticulously ground to precise diameters with tolerances as tight as a few microns. They serve as a reference standard for checking the size and straightness of drilled or machined holes. Each gauge is precisely calibrated against national or international measurement standards to guarantee absolute dimensional accuracy.
The primary advantage of pin gauges lies in their simplicity. They come in sets, with each pin representing a specific dimension. In a 'go' gauge, the pin should easily slide into the hole, indicating that the hole is within the acceptable lower limit of the tolerance range. Conversely, a 'no-go' gauge should not enter the hole or do so only partially, signifying that the dimension exceeds the upper tolerance limit. This binary system provides an immediate pass/fail assessment, making it a swift and straightforward method for quality inspection.
**Construction and Material**
Calibrated pin gauges are typically fabricated from high-grade steel, chosen for its hardness, wear resistance, and stability under varying temperatures. Chromium-plating is often applied to enhance corrosion resistance and improve surface finish, ensuring consistent and reliable measurements over time. The ends of the pins may feature a slightly rounded tip to prevent damage to the part being inspected and facilitate smooth insertion The ends of the pins may feature a slightly rounded tip to prevent damage to the part being inspected and facilitate smooth insertion
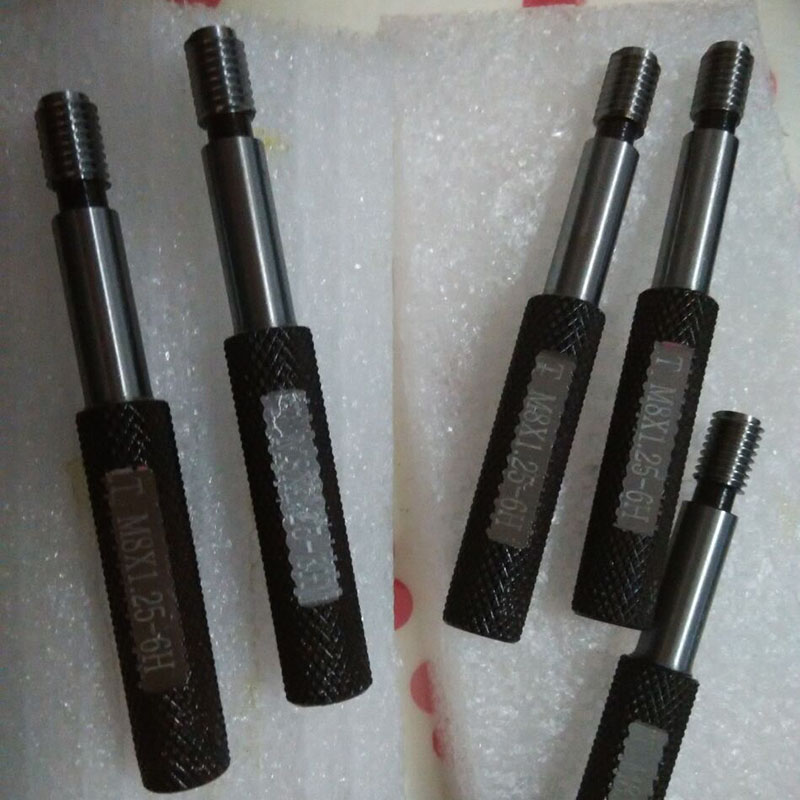
The ends of the pins may feature a slightly rounded tip to prevent damage to the part being inspected and facilitate smooth insertion The ends of the pins may feature a slightly rounded tip to prevent damage to the part being inspected and facilitate smooth insertion
calibrated pin gauges.
**Applications Across Industries**
From aerospace to automotive, medical devices to microelectronics, calibrated pin gauges find application wherever micron-level accuracy is paramount. In the automotive industry, they ensure the correct fitment of engine components; in aerospace, they verify the precision of aircraft parts where safety is critical. Medical device manufacturers rely on them to maintain strict tolerances in implants and surgical instruments, while in semiconductor manufacturing, they contribute to the meticulous fabrication of minuscule components.
**Maintenance and Calibration**
Maintaining the accuracy of pin gauges is crucial to their effectiveness. Regular cleaning with a soft cloth and appropriate solvent prevents contamination and preserves surface integrity. Storage in a controlled environment, typically in a humidity-controlled cabinet, safeguards against dimensional changes due to temperature fluctuations. Periodic recalibration by accredited laboratories is mandatory to verify and restore the gauges' dimensional conformity, typically annually or after a set number of uses, depending on usage frequency and industry standards.
**Conclusion**
Calibrated pin gauges embody the essence of precision in modern manufacturing. Their role extends beyond mere measurement tools; they are guardians of quality, ensuring that products meet stringent tolerances and perform as intended. As technology advances and manufacturing tolerances become ever tighter, the reliance on these meticulously crafted instruments will only continue to grow. By embracing best practices in their use and maintenance, industries can harness the full potential of calibrated pin gauges, driving advancements in product quality and reliability. In the quest for perfection, these humble yet highly effective tools stand as a testament to human ingenuity and the relentless pursuit of precision.