Metric ring gages, an essential tool in the world of precision manufacturing and engineering, play a pivotal role in ensuring dimensional accuracy and consistency. These gauges, also known as ring gauges or external thread gauges, are specifically designed to measure the outer diameter of cylindrical parts, particularly in the context of the metric system.
A metric ring gauge is essentially a circular ring with an accurately machined internal diameter that corresponds to a specific metric dimension. The 'metric' in its name refers to the use of the International System of Units (SI), which is the standard global measurement system. It serves as a master against which parts can be checked for compliance, providing a precise reference for quality control and inspection processes.
The primary function of a metric ring gage is to verify whether a workpiece meets the specified tolerance limits. In manufacturing, where precision is paramount, even the slightest deviation from the set standards can lead to significant issues. Metric ring gages help prevent such deviations by enabling manufacturers to detect any over or under-sizing during production.
The design of metric ring gages is often simple yet robust, typically made from high-strength materials like steel or carbide to withstand repeated usage and maintain accuracy over time. They come in various sizes, covering a wide range of metric dimensions, to cater to diverse industrial applications They come in various sizes, covering a wide range of metric dimensions, to cater to diverse industrial applications
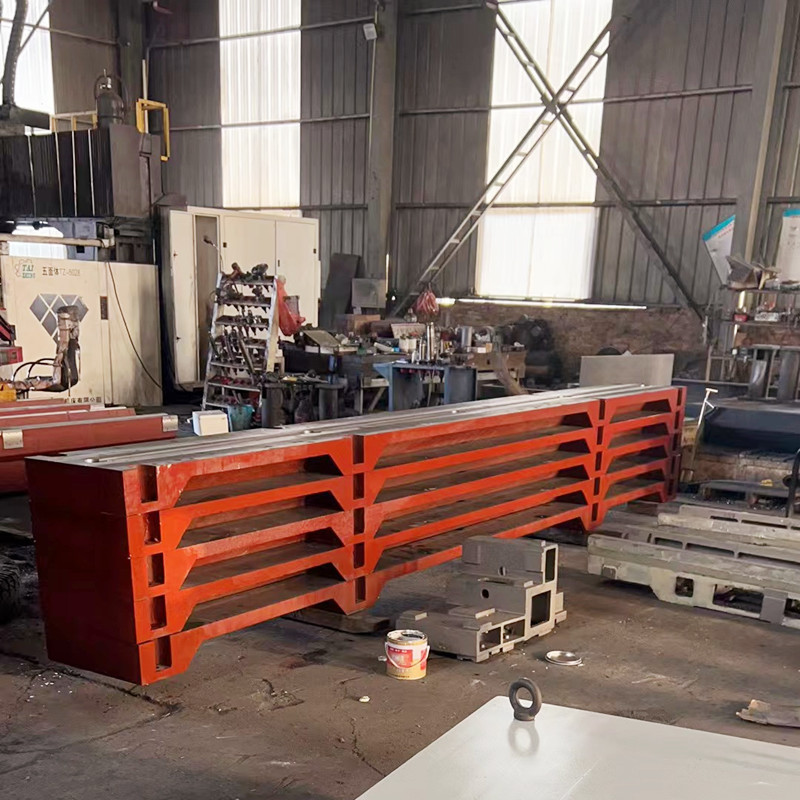
They come in various sizes, covering a wide range of metric dimensions, to cater to diverse industrial applications They come in various sizes, covering a wide range of metric dimensions, to cater to diverse industrial applications
metric ring gages. Some may also have Go-NoGo configurations, where one end indicates acceptable minimum size and the other end signifies maximum limit, simplifying the inspection process.
In addition to their use in manufacturing, metric ring gages find application in calibration laboratories, where they serve as traceable standards for calibrating other measuring instruments. Their importance in ensuring dimensional integrity extends not just to the manufacturing sector but also to automotive, aerospace, medical device, and numerous other industries that rely on precise measurements.
In conclusion, metric ring gages are indispensable tools in the realm of precision engineering. They embody the essence of quality control, fostering reliability and consistency in manufacturing processes. By facilitating accurate measurements and stringent adherence to specifications, they contribute significantly to the overall efficiency and success of industrial operations. As technology advances, the role of metric ring gages is likely to become even more critical in ensuring the highest levels of precision in the products we use daily.