Metal Corner Connections A Crucial Aspect of Structural Integrity
In the realm of construction and engineering, metal corner connections play a pivotal role in ensuring the structural integrity and stability of various structures. These connections are the points where two or more metal elements meet, and they are subjected to significant stress and strain due to external forces such as wind, earthquakes, and vibrations. Therefore, it is essential to understand the design, fabrication, and maintenance of these connections to prevent potential failures and ensure the longevity of the structure.
One of the primary factors that influence the performance of metal corner connections is the type of joint used. There are several types of joints, including welded, bolted, and riveted joints, each with its own advantages and disadvantages. For instance, welded joints provide a high degree of strength and rigidity but may be more susceptible to corrosion. On the other hand, bolted joints are relatively easy to assemble and disassemble but may not offer the same level of strength as welded joints.
Another critical aspect of metal corner connections is the material selection. The choice of material depends on factors such as the specific application, environmental conditions, and required strength and durability. For example, stainless steel is commonly used in marine environments due to its excellent corrosion resistance, while aluminum is preferred for its lightweight properties and high strength-to-weight ratio For example, stainless steel is commonly used in marine environments due to its excellent corrosion resistance, while aluminum is preferred for its lightweight properties and high strength-to-weight ratio
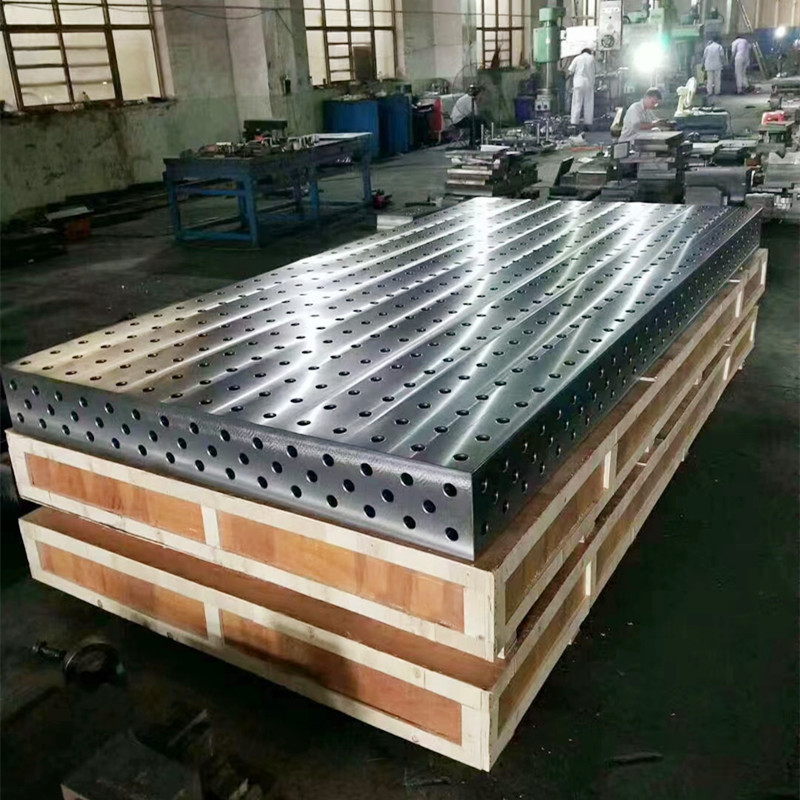
For example, stainless steel is commonly used in marine environments due to its excellent corrosion resistance, while aluminum is preferred for its lightweight properties and high strength-to-weight ratio For example, stainless steel is commonly used in marine environments due to its excellent corrosion resistance, while aluminum is preferred for its lightweight properties and high strength-to-weight ratio
metal corner connections.
Fabrication techniques also play a crucial role in the performance of metal corner connections. Proper cleaning, preparation, and finishing of the metal surfaces are essential to ensure a strong bond between the components. Additionally, the use of advanced joining techniques such as friction stir welding or laser welding can further enhance the strength and reliability of the connection.
Regular maintenance and inspection are also critical to the longevity of metal corner connections. It is important to regularly inspect the connections for signs of wear, corrosion, or damage and to take appropriate measures to address any issues promptly. This may include cleaning and coating the connections to protect them from the environment or replacing damaged components before they fail.
In conclusion, metal corner connections are a vital component of structural integrity in construction and engineering projects. By considering factors such as joint type, material selection, fabrication techniques, and maintenance, engineers can design and construct stronger, more reliable structures that withstand the rigors of various environmental conditions and operational loads.