Understanding Hole Gauges Precision Measuring Tools in Manufacturing
Hole gauges, an integral part of the precision engineering and manufacturing world, play a crucial role in ensuring accuracy and consistency in various industrial processes. These specialized tools are designed to measure the diameter of holes, providing engineers and technicians with vital data for quality control and process optimization.
A hole gauge, also known as a ring gauge, is essentially a cylindrical tool with an inner diameter that corresponds to the nominal size of the hole being measured. It functions by sliding over the hole; if it fits snugly, the hole's diameter is within acceptable limits. This simple yet effective mechanism ensures that components meet the strict tolerances required in industries such as aerospace, automotive, and machinery manufacturing.
There are two primary types of hole gauges go gauges and no-go gauges. A 'go' gauge is used to verify if the hole is within the lower limit of the tolerance zone, while a 'no-go' gauge checks if it exceeds the upper limit. If the 'go' gauge fits through but the 'no-go' gauge doesn't, the hole diameter is considered acceptable.
The precision of hole gauges lies in their manufacturing process. They are typically made from high-strength materials like stainless steel or carbon steel, hardened and ground to achieve exceptional dimensional stability and wear resistance. The tolerance on these gauges is often in the micrometer range, highlighting their importance in maintaining stringent standards The tolerance on these gauges is often in the micrometer range, highlighting their importance in maintaining stringent standards
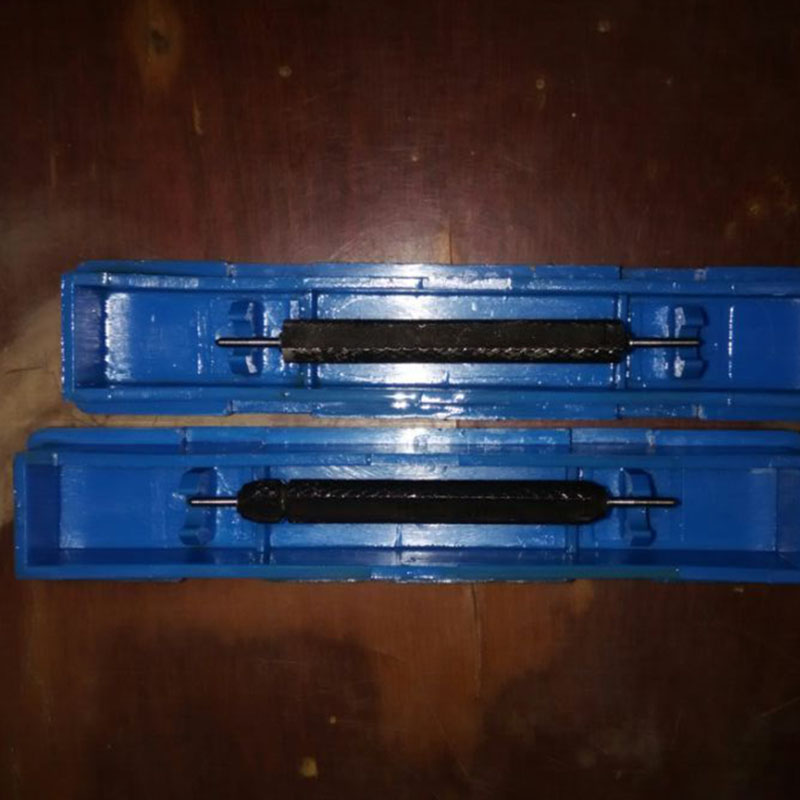
The tolerance on these gauges is often in the micrometer range, highlighting their importance in maintaining stringent standards The tolerance on these gauges is often in the micrometer range, highlighting their importance in maintaining stringent standards
hole gauges.
Hole gauges also come in different configurations. Plain hole gauges are used for simple cylindrical holes, while blind hole gauges are designed for measuring depths and diameters of blind holes. Specialized versions, like thread ring gauges, are used to check the quality of threads in a hole.
The use of hole gauges extends beyond just checking dimensions. They are also instrumental in detecting inconsistencies, ovality, or deformation in holes, which could otherwise lead to assembly issues or failure of components. In this way, they serve as a preventive measure, saving time, resources, and potentially avoiding costly errors.
In conclusion, hole gauges are indispensable tools in the realm of manufacturing and engineering. Their precision, durability, and versatility make them a staple in quality control processes. With ongoing advancements in materials and design, hole gauges continue to evolve, ensuring that the stringent demands of modern manufacturing are met with unwavering accuracy and reliability.