Understanding the Standard Bore Gage A Precision Tool for Measuring Engineered Holes
In the world of manufacturing and engineering, precision is paramount. One tool that plays a vital role in ensuring this precision is the standard bore gage, an essential instrument for measuring the internal diameter of holes. This article delves into the intricacies of standard bore gages, their importance, operation, and applications.
A standard bore gage, also known as a bore gauge or inside micrometer, is a specialized tool designed to measure the diameter of cylindrical openings with extreme accuracy. It operates on the principle of mechanical comparison, where the size of the gage is compared against the internal dimension of the bore. The term 'standard' refers to the adherence to specific industry standards, such as ANSI (American National Standards Institute) or ISO (International Organization for Standardization), ensuring consistent and reliable measurements.
The construction of a standard bore gage typically involves a calibrated, adjustable measuring probe that can expand or contract to fit snugly within the bore. The probe's movement is controlled by a handle or knob, allowing the user to adjust the gage's diameter until it matches the inside diameter of the hole. Once in contact, a reading is taken, often displayed on a dial or digital indicator, providing the precise measurement.
The use of a standard bore gage offers several advantages. Its versatility allows it to be employed in various industries, from automotive and aerospace to machinery and tooling. It ensures the accurate sizing of engine cylinder bores, critical for maintaining optimal engine performance It ensures the accurate sizing of engine cylinder bores, critical for maintaining optimal engine performance
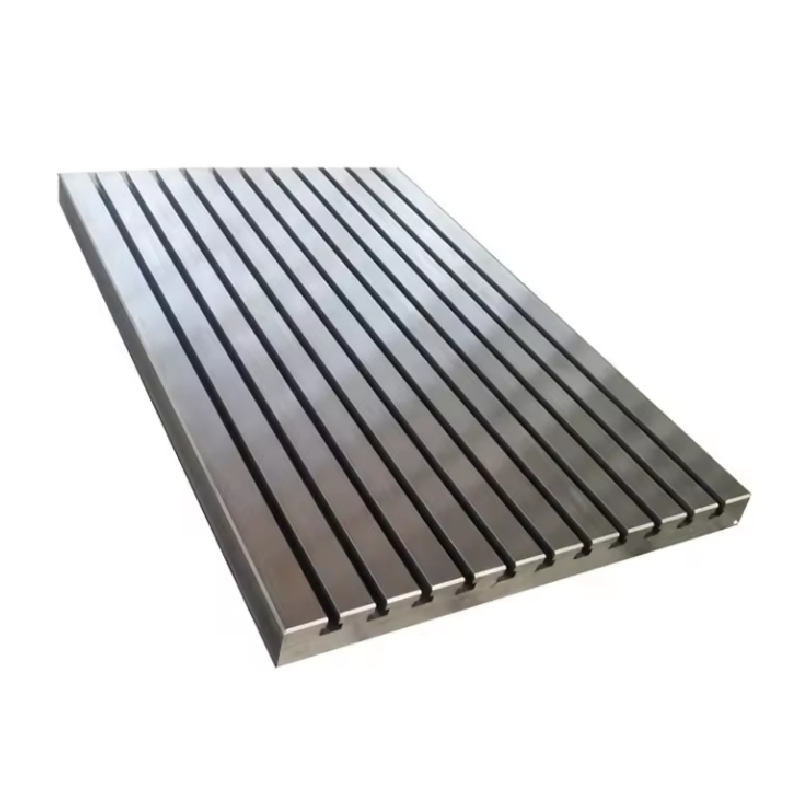
It ensures the accurate sizing of engine cylinder bores, critical for maintaining optimal engine performance It ensures the accurate sizing of engine cylinder bores, critical for maintaining optimal engine performance
standard bore gage. In manufacturing, it verifies the consistency of production processes, preventing defects and ensuring product quality. Moreover, its ability to measure in tight spaces and irregularly shaped holes adds to its utility.
However, operating a standard bore gage requires skill and attention to detail. Proper calibration and cleaning of the gage before use are crucial to obtaining accurate readings. Additionally, understanding the limitations of the tool, such as the effect of temperature and surface finish on measurements, is equally important.
In conclusion, the standard bore gage is more than just a tool; it is a testament to human ingenuity in pursuit of precision. It bridges the gap between design specifications and physical reality, enabling engineers and technicians to create products with unparalleled accuracy. As technology advances, so too do these gages, with digital and wireless models now available, enhancing both efficiency and precision. Despite its simplicity, the standard bore gage remains a cornerstone of engineering measurement, a symbol of the importance of accuracy in our increasingly complex world.