In the realm of hydraulic systems, check valves play a critical role in managing the direction of fluid flow and maintaining pressure. These components, essential for preventing backflow, come in various types, each suited for divergent applications and requirements. When selecting a hydraulic check valve, understanding the intricate differences between types ensures the longevity and efficiency of the entire system. Here's an in-depth look at the various types of hydraulic check valves, enriched with insights drawn from years of experience and authoritative expertise.
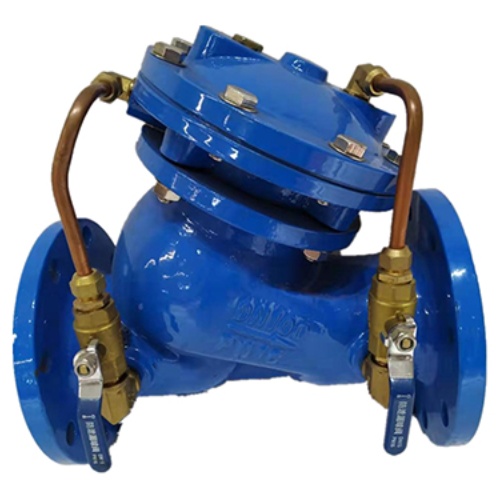
1. Swing Check Valves
Swing check valves are characterized by a swinging disc or flap, which allows fluid to flow in one direction and automatically closes upon flow reversal. These valves are well-known for their simplicity and reliability, making them a staple in systems where the flow direction is relatively stable. The main advantage is minimal flow resistance and energy efficiency due to the unobstructed flow path. However, they may not be suitable for pulsating or high-pressure applications as the swinging mechanism might wear prematurely.
2. Lift Check Valves
These valves operate using a disc that lifts off the seat to allow flow and descends to block reversals. Typically used in vertical lines with upward flow, lift check valves are robust against high pressures and ideal for systems needing quick flow halts. Expertise suggests these valves have excellent sealing capabilities, but the subsequent pressure drop can be a drawback. Maintenance requires regular inspection as debris can hinder their operation.
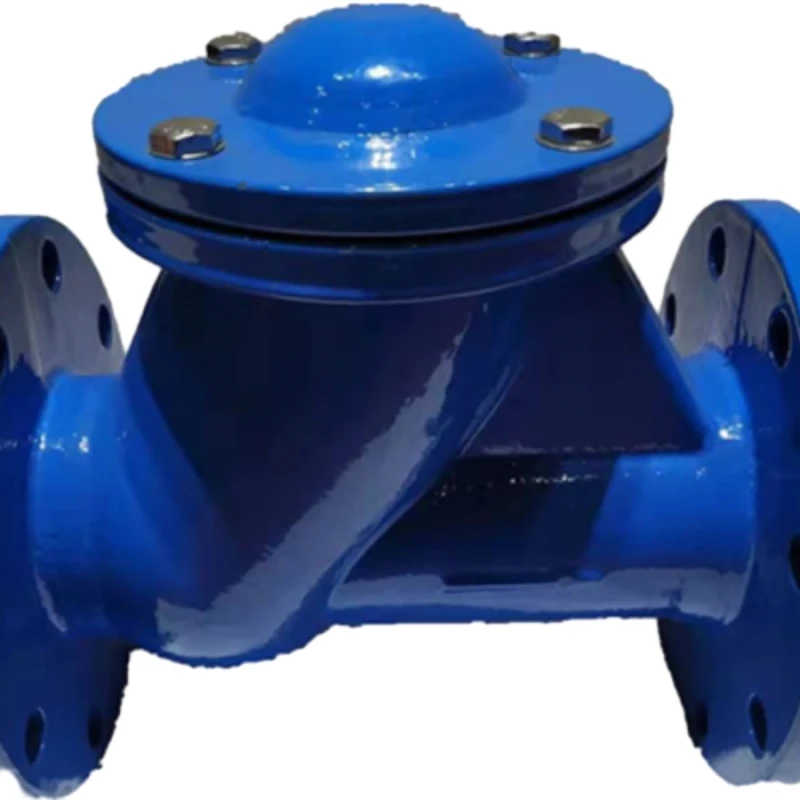
3. Ball Check Valves
Ball check valves feature a spherical ball that moves up and down within a cylindrical chamber, allowing fluid passage when pressured in one direction while sealing when reverse flow occurs. The design is uncomplicated, making maintenance relatively easier. Their durability and ability to handle high-pressure conditions make them suitable for various demanding applications. However, industry authorities recommend regular maintenance checks to prevent sediment accumulation.
4. Disc Check Valves
Utilizing a disc loaded by a spring, these valves open and close based on the flow and pressure. They are distinguished by their compact design and ability to withstand high temperatures and pressures.
The quick operational response makes disc check valves favored in high-speed processes. Professionals highlight the requirement for a minimum upstream pressure to function effectively, thus always assess compatibility with existing systems.
hydraulic check valve types
5. Wafer Check Valves
Known for their slim profile, wafer check valves are lighter and easier to install compared to their counterparts. Positioned between flanges, they occupy less space and reduce installation expense. The unique design allows them to cope well with large flow rates. Hydraulic specialists counsel that these valves are best used where space is a constraint, yet they may not be the best fit for systems with significant fluid debris that could impede their function.
6. Inline Check Valves
These are direct flow-through valves that fit within a pipeline's diameter, making them less invasive and more integrated with system infrastructure. The strength of inline check valves lies in their minimal impact on flow dynamics, aiding in maintaining system efficiency. This type of valve exhibits reliable performance in sterile and clean environments as advised by hydraulic experts.
For successful deployment of hydraulic check valves, industry experts emphasize the significance of selecting the appropriate type based on system requirements, environmental conditions, and maintenance capabilities. Experience has shown that incorrect selection can lead to inefficiencies, potential failures, and increased operational costs. Therefore, a thorough assessment and consultation with hydraulic specialists is advisable, ensuring optimized performance and enhanced trustworthiness in hydraulic systems.
When considering valve types for specific applications, prioritize factors such as pressure levels, flow characteristics, and potential contaminant presence. Additionally, understand that while initial cost is an important consideration, long-term reliability and maintenance availability are equally pivotal for sustainable operations.
In conclusion, each type of hydraulic check valve offers distinct advantages and potential limitations. Leveraging expert advice and accumulating experience from existing installations can greatly enhance system efficacy. Trust in credible sources and authoritative resources for guidance in navigating the diverse landscape of hydraulic check valves, ensuring each choice is intelligent, informed, and advantageous.