Valves play a crucial role in fluid control systems across various industries, ranging from household plumbing to complex industrial processing. Understanding the nuances of different types of valves, their applications, and maintenance strategies can significantly enhance operational efficiency and safety. This article delves into the world of valves by leveraging extensive experience, in-depth expertise, authoritative insights, and trustworthy practices to help you make informed decisions about valve selection and maintenance.
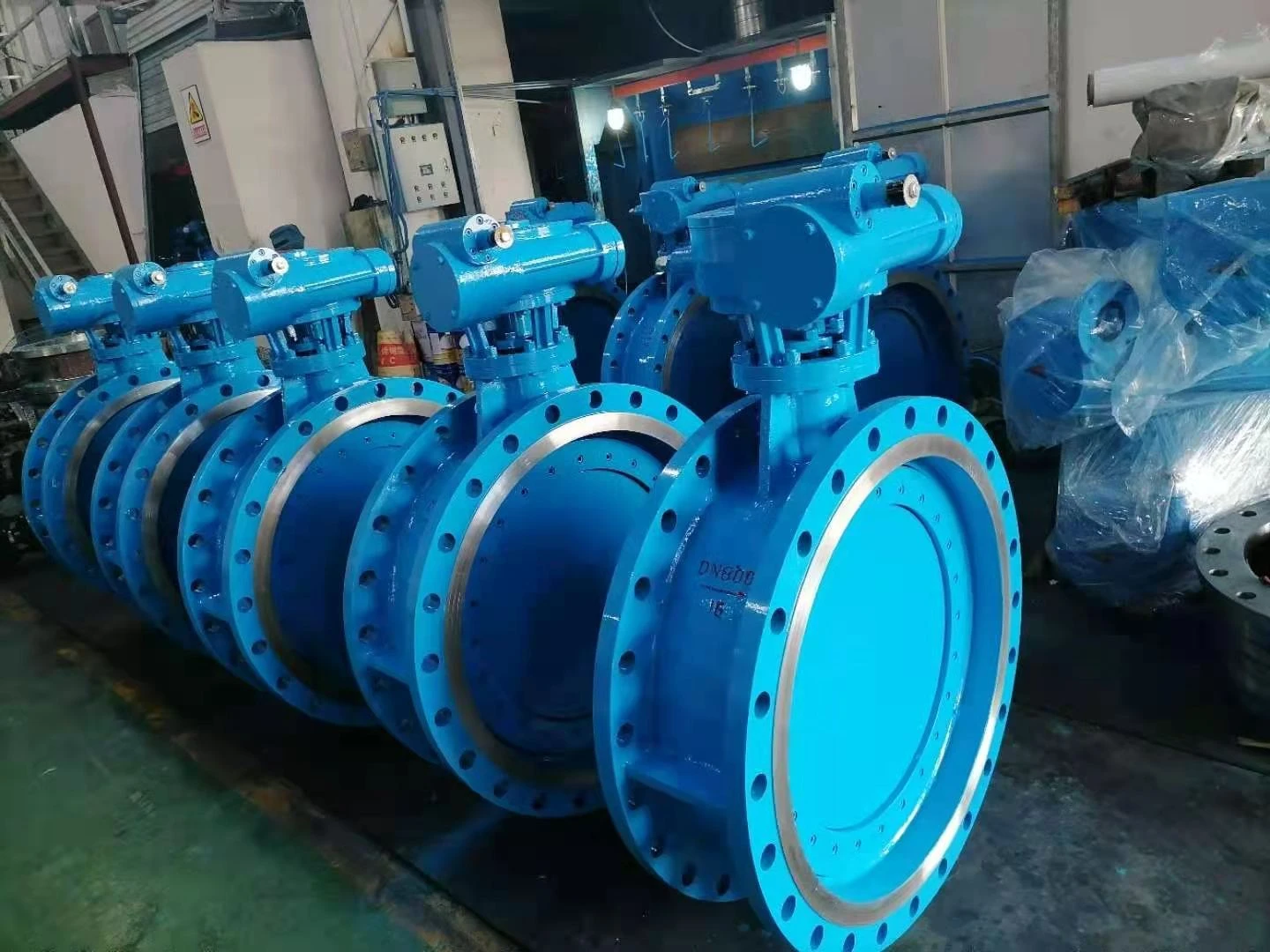
Valves are mechanical devices that regulate the flow and pressure of fluids within a system. Their applications are diverse, spanning industries such as oil and gas, chemical processing, water treatment, and HVAC systems. To select the right valve for a specific application, consider the type of fluid, pressure, temperature, and flow rate. Some common types of valves include gate valves, ball valves, butterfly valves, and globe valves, each serving distinct functions and offering unique benefits.
From years of hands-on experience and industry insight, it’s evident that selecting the appropriate valve type significantly reduces the risk of leaks and malfunctions. For instance, ball valves are known for their tight sealing capabilities, making them ideal for applications requiring a reliable shut-off mechanism. On the other hand, butterfly valves are often chosen for applications requiring quick, frequent operations due to their lightweight and cost-effective design.
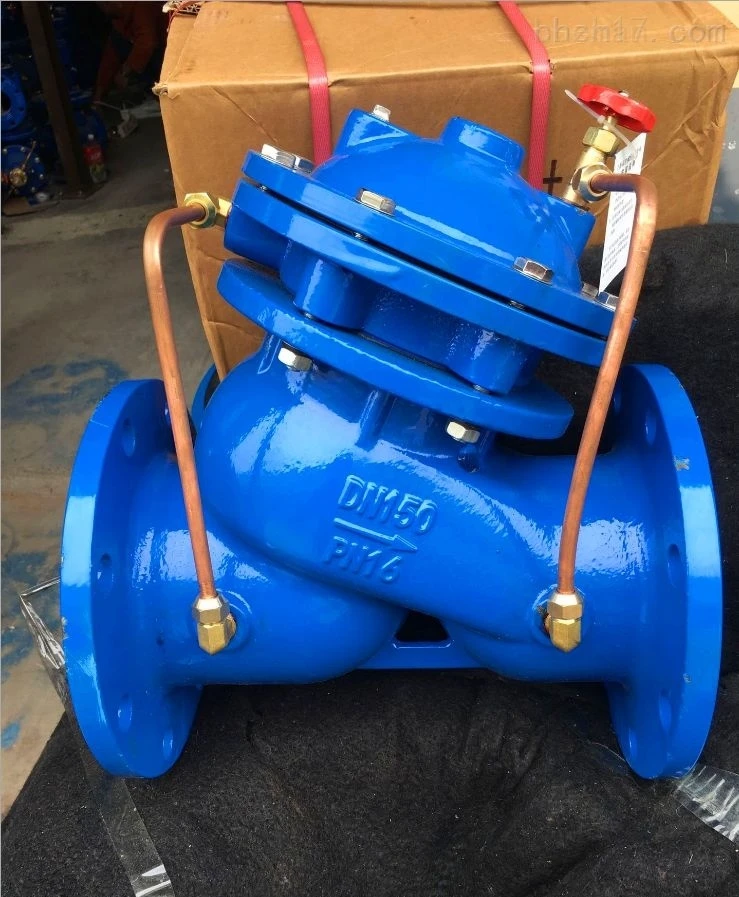
Expertise in valve maintenance is equally vital to ensure long-term functionality and safety. Regular inspection and servicing help detect early signs of wear and tear, preventing costly repairs and system downtimes. It is recommended to establish a maintenance schedule based on the valve’s operating environment and the manufacturer’s guidelines. Key maintenance practices include lubrication, checking seals and packing for integrity, and ensuring that the actuator functions correctly.
valve
Authoritative knowledge in valve technology and trends can offer a competitive edge when specifying valves for new systems. Innovations in smart valve technology, such as automated and remote monitoring systems, provide advanced solutions for real-time flow control and diagnostics. These advancements allow for predictive maintenance, enhancing the reliability and efficiency of systems while minimizing manual intervention.
Building trustworthiness involves sourcing valves from reputable manufacturers with a proven track record of quality and performance. Ensure that the valves meet industry standards and certifications to guarantee safety and reliability. Collaborating with accredited suppliers reduces the risk of errors in the procurement process and assures compliance with industry regulations.
In summary, a deep understanding of valve types, coupled with methodical maintenance practices and adoption of the latest technologies, can result in significant improvements in system efficiency and reliability. By approaching valve selection with a blend of practical experience, expert knowledge, authoritative insights, and reliability assurances, businesses can optimize their fluid control processes effectively.