Control valves play an integral role in industrial processes, where they regulate fluid flow, pressure, temperature, and liquid levels by modulating the flow of fluids like water, steam, gases, or chemicals. Understanding the different types of control valves is crucial for optimizing process efficiency, safety, and overall system performance. In this article, we delve into several common categories of control valves, their functionalities, and typical applications.
1. Globe Valves
Globe valves are one of the most versatile and widely used control valves. They feature a linear motion design with a disk that moves perpendicular to the seat to regulate flow. The flow path through a globe valve involves changes in direction, which results in higher pressure drops compared to other designs. Globe valves are ideal for precise flow control and shut-off applications, commonly found in industries such as oil and gas, chemical processing, and power generation.
2. Butterfly Valves
Butterfly valves operate using a rotary motion, with a disc mounted on a shaft that rotates to block or permit flow. Their simplicity, lightweight, and cost-effectiveness make them popular choices, especially for large pipe diameters. Butterfly valves can be used for both throttling and on/off control but are typically not as accurate as globe valves for fine flow regulation. They find extensive use in water treatment plants, HVAC systems, and pulp and paper manufacturing.
3. Ball Valves
Ball valves employ a spherical disc with a bore to control fluid passage. When aligned with the valve body's flow channel, the ball permits flow; rotation of the ball by 90 degrees shuts it off completely. Known for their tight shut-off capabilities and low maintenance requirements, ball valves are often used in applications where quick on/off control is necessary, such as in petrochemical plants, refineries, and firefighting systems.
4
4
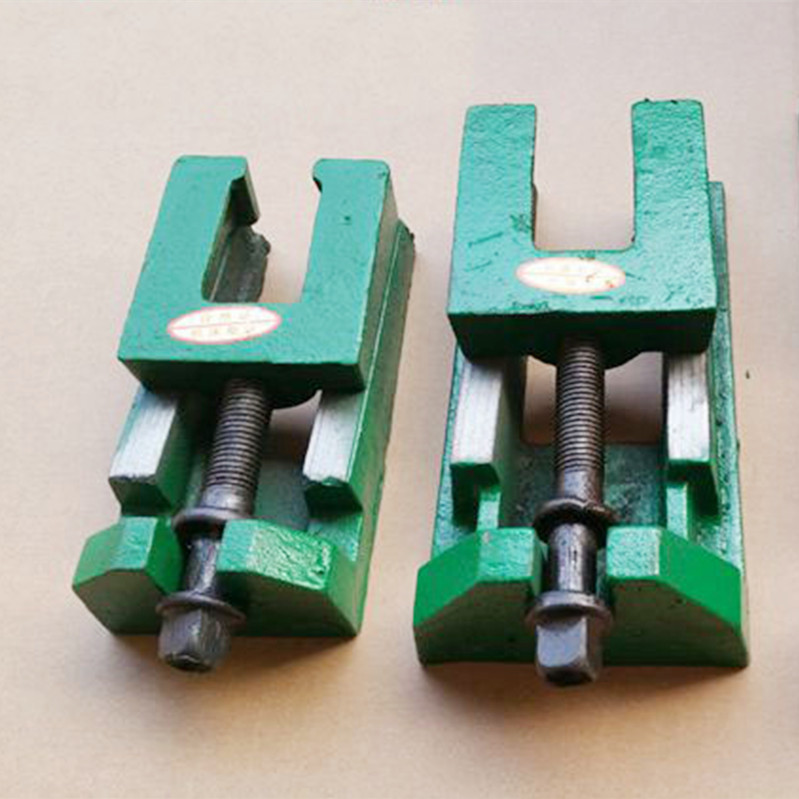
4
4
different types of control valve. Plug Valves
Plug valves are similar to ball valves but use a conical or cylindrical plug instead of a ball. They offer versatile flow control, including throttling, thanks to their various port configurations (such as straight-through, multi-port, or eccentric). Plug valves excel in handling slurries and viscous fluids due to their self-cleaning characteristics. They are commonly employed in mining, food processing, and pharmaceutical industries.
5. Needle Valves
Needle valves are designed for precise flow regulation, particularly in low-flow applications. They feature a long, slender needle-like tip that gradually opens or closes the valve seat, allowing fine-tuning of flow rates. Due to their high accuracy and tight shut-off capabilities, needle valves are frequently used in instrumentation and calibration processes, hydraulic systems, and laboratory equipment.
6. Diaphragm Valves
Diaphragm valves use a flexible diaphragm to separate the valve's actuating mechanism from the fluid, ensuring zero contamination. They are highly suitable for handling corrosive, abrasive, or sterile fluids in industries such as pharmaceuticals, food and beverage, and biotechnology. Diaphragm valves can either be weir-type, suitable for clean fluids, or straight-through for more viscous or solids-laden fluids.
Conclusion
Selecting the right type of control valve is critical to achieving optimal process control. Each valve type has its unique advantages, making it suited for specific applications based on factors such as flow characteristics, pressure drop, fluid properties, and required level of control precision. Understanding these differences allows engineers to make informed decisions that enhance process efficiency, safety, and reliability across diverse industrial sectors. Whether the goal is to minimize energy consumption, improve product quality, or ensure the safe handling of hazardous materials, the appropriate choice of control valve is paramount to success.