An Overview of Knife Gate Valve Types and Their Applications
In the realm of industrial fluid control systems, knife gate valves occupy a pivotal position due to their unique design and functionality. These valves are specifically engineered to manage heavy-duty applications involving slurries, powders, and highly abrasive or corrosive media. Understanding the different types of knife gate valves is crucial for selecting the right valve for a given application, ensuring optimal performance and longevity. In this article, we delve into the various types of knife gate valves and their respective uses.
**1. Conventional Knife Gate Valve**
The conventional or standard knife gate valve is the most basic type, featuring a simple design with a sharp blade that slides across the seat to cut through any solids in the flow path. It's typically used in water treatment plants, paper mills, and mining operations where handling slurries and fibrous materials is common. These valves are not designed for precise throttling but excel in on/off service, providing a tight shut-off.
**2. Resilient Seated Knife Gate Valve**
Resilient seated knife gate valves incorporate an elastomeric seat, usually made of rubber or polyurethane, which enhances the sealing properties, making them suitable for both liquid and gas services. The resilient seat provides better resistance against corrosion and abrasion, extending the valve's life span. They are often seen in wastewater management and chemical processing industries where leak-tightness is critical.
**3. Metal Seated Knife Gate Valve**
Contrary to resilient seated valves, metal seated knife gate valves use metal-to-metal seating, making them ideal for high-temperature and high-pressure applications where extreme durability is required. These valves can withstand harsh conditions like those found in power generation, petrochemical plants, and metallurgical processes. They offer superior resistance to corrosion and wear, even when handling abrasive media.
**4. Bi-Directional Knife Gate Valve**
Bi-directional knife gate valves are designed to provide tight shut-off in both flow directions. This feature makes them versatile, enabling installation without concerns about flow directionality This feature makes them versatile, enabling installation without concerns about flow directionality
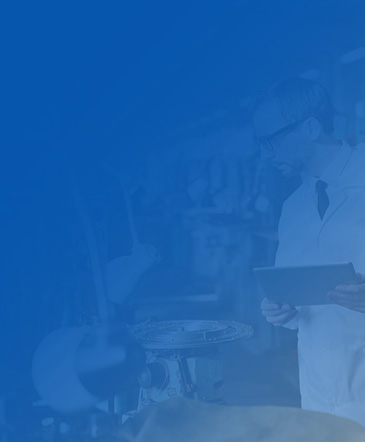
This feature makes them versatile, enabling installation without concerns about flow directionality This feature makes them versatile, enabling installation without concerns about flow directionality
knife gate valve types. They are particularly useful in systems where reverse flow might occur, such as in pumping stations and irrigation networks.
**5. Wafer Style Knife Gate Valve**
Wafer style knife gate valves are designed for easy installation between two flanges, reducing the overall weight and cost compared to other designs. They do not require nuts and bolts for mounting, simplifying maintenance and replacement procedures. These valves are commonly used in piping systems where space is limited and frequent cleaning or inspection is necessary.
**6. Pneumatic/Hydraulic Actuated Knife Gate Valve**
For automated process control, knife gate valves can be actuated using pneumatic or hydraulic systems. These valves offer remote operation, enhancing safety and efficiency in environments that may be hazardous or difficult to access manually. They are prevalent in large-scale industrial operations, including oil and gas refineries and water treatment facilities.
**7. Sanitary Knife Gate Valve**
Sanitary knife gate valves are specifically designed for applications in the food, beverage, and pharmaceutical industries, where cleanliness and hygiene are paramount. They feature smooth surfaces, crevice-free designs, and are often made from stainless steel to facilitate easy cleaning and sterilization. These valves ensure that the product purity is maintained throughout the process.
In conclusion, the selection of a knife gate valve type should be based on the specific requirements of the application, including the nature of the medium being controlled, operating pressures and temperatures, and the need for automation. Understanding the unique features and advantages of each type enables engineers and plant operators to make informed decisions, optimizing process efficiency and equipment longevity. With advancements in material science and engineering designs, knife gate valves continue to evolve, meeting the ever-changing demands of modern industrial processes.