The Significance of Inspection Surface Plates in Precision Engineering
In the realm of precision engineering, an inspection surface plate serves as an indispensable tool for quality control and accuracy assessment. It is a fundamental element in the manufacturing process, ensuring that components and products meet stringent tolerances and specifications.
An inspection surface plate, often made from high-grade materials like granite or cast iron, provides a flat and stable reference surface. Its primary function is to facilitate the measurement, alignment, and inspection of various workpieces. The 'percent' in 'inspection surface plate%' refers to the degree of flatness, which is a critical parameter determining its effectiveness. A higher percentage indicates a flatter surface, translating to more precise measurements.
The surface plate's importance lies in its ability to detect even the slightest deviation from perfection. In industries such as aerospace, automotive, and electronics, where tolerances can be as minute as micrometers, these plates are indispensable. They enable the detection of defects, irregularities, and dimensional deviations that might otherwise go unnoticed, ensuring the integrity and functionality of the final product.
Beyond basic measurements, inspection surface plates also support a range of inspection techniques. They can be used with various metrology tools like gauges, micrometers, and coordinate measuring machines (CMMs) to perform complex geometrical measurements They can be used with various metrology tools like gauges, micrometers, and coordinate measuring machines (CMMs) to perform complex geometrical measurements
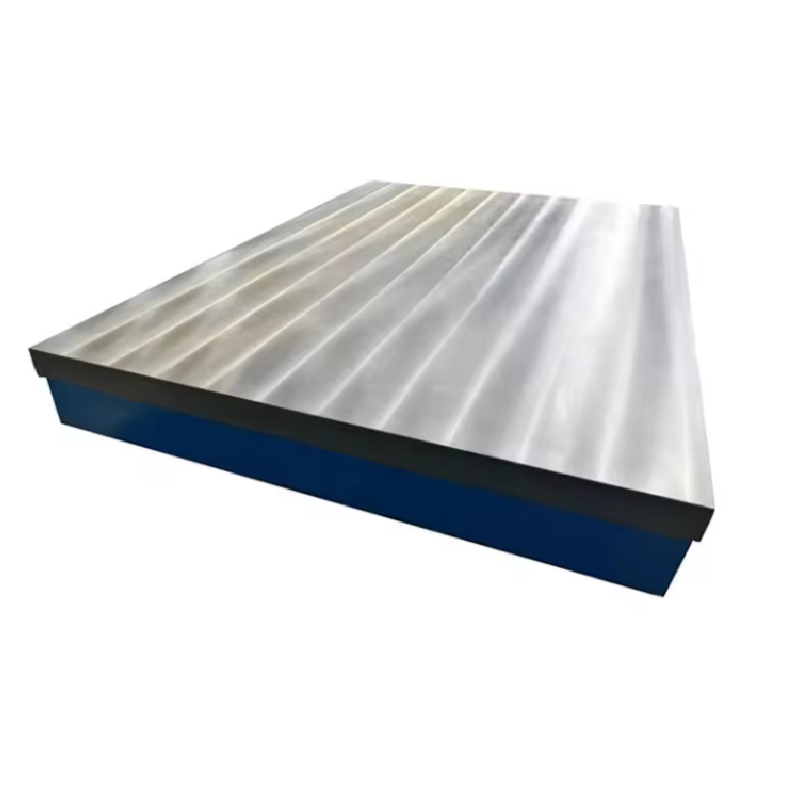
They can be used with various metrology tools like gauges, micrometers, and coordinate measuring machines (CMMs) to perform complex geometrical measurements They can be used with various metrology tools like gauges, micrometers, and coordinate measuring machines (CMMs) to perform complex geometrical measurements
inspection surface plate. The surface plate's uniformity allows for accurate comparison and calibration of these tools, enhancing overall measurement consistency.
Maintenance of inspection surface plates is crucial for maintaining their accuracy. Regular cleaning, conditioning, and certification are necessary to prevent wear, distortion, or contamination that could compromise results. This underscores the need for skilled technicians who understand the intricacies of these tools and the processes they support.
In today's fast-paced manufacturing environment, where precision and efficiency are paramount, inspection surface plates have evolved to incorporate advanced features. Digital indicators, laser scanning, and 3D imaging technologies are now integrated, providing real-time data and enhancing inspection capabilities.
In conclusion, the inspection surface plate is more than just a piece of equipment; it is a testament to the commitment to quality and precision in manufacturing. Its role in ensuring product integrity, preventing defects, and driving continuous improvement cannot be overstated. As technology continues to advance, we can expect even more sophisticated surface plates to emerge, further refining the art and science of precision engineering.