Control valve sizing is an essential aspect of designing efficient and reliable process control systems. It involves selecting the appropriate valve size to ensure optimal flow control, system stability, and energy efficiency. A properly sized control valve not only guarantees process performance but also prevents issues like cavitation, noise, and excessive pressure drop, which can lead to equipment damage and reduced operational efficiency. This article delves into the fundamental principles and steps involved in control valve sizing.
Understanding the Basics
Control valves are regulatory devices used to manipulate fluid flow in response to signals from a controller. Sizing a control valve correctly requires a thorough understanding of process variables such as flow rate, pressure drop, fluid properties, and the desired control characteristics.
Step 1 Determine Required Flow Characteristics
The first step in control valve sizing is to determine the maximum and minimum flow rates required for the process under normal and abnormal conditions. These flow rates are typically provided by process engineers based on the system's design specifications and operating conditions. It's crucial to consider factors like valve authority (the ratio of pressure drop across the valve to the total pressure drop in the system) to avoid valve chatter or instability.
Step 2 Fluid Properties Analysis
Understanding the properties of the fluid being controlled is vital. Density, viscosity, compressibility, and specific heat are all factors that influence valve selection and sizing. For instance, high-viscosity fluids may require special valve designs to minimize pressure loss and maintain controllability.
Step 3 Selection of Valve Type
Different valve types—such as globe, ball, butterfly, or plug valves—offer varying flow characteristics and pressure drops. The selection depends on factors like flow regulation requirements, space constraints, maintenance needs, and material compatibility with the process fluid.
Step 4 Calculation of Flow Coefficient (Cv)
The flow coefficient (Cv) is a standard industry term used to express the capacity of a valve to pass fluid
Step 4 Calculation of Flow Coefficient (Cv)
The flow coefficient (Cv) is a standard industry term used to express the capacity of a valve to pass fluid
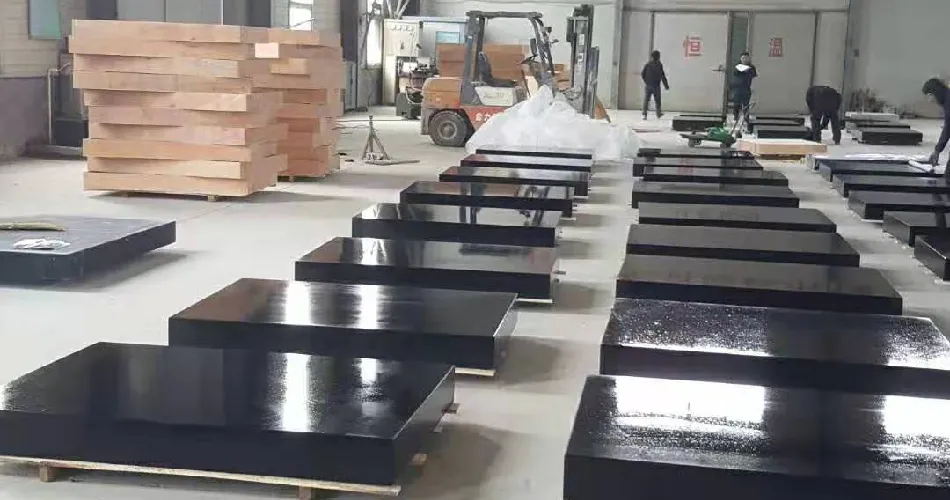
Step 4 Calculation of Flow Coefficient (Cv)
The flow coefficient (Cv) is a standard industry term used to express the capacity of a valve to pass fluid
Step 4 Calculation of Flow Coefficient (Cv)
The flow coefficient (Cv) is a standard industry term used to express the capacity of a valve to pass fluid
control valve sizing. It represents the volume of water (in US gallons per minute) at a specific temperature (usually 60°F) that will flow through the valve with a pressure drop of 1 PSI across the valve. To calculate Cv, engineers use flow rate data and the ISA-75.01.01 (IEC 60534-2-1) standard, which provides Cv calculation formulas considering various valve types and flow patterns.
Step 5 Pressure Drop Considerations
Pressure drop across the valve should be estimated to ensure it falls within acceptable limits for the system. Excessive pressure drop can lead to inefficient operation and increased energy costs, while too little may result in inadequate control. Calculating the pressure drop involves using the valve’s flow characteristic curves, which show how the valve’s flow capacity changes with respect to the pressure drop across it.
Step 6 Valve Sizing and Selection
With the Cv value and pressure drop information, the actual valve size can be selected from manufacturers’ catalogs. These catalogs provide Cv values for different valve sizes and trim configurations. It's essential to choose a valve size that matches the calculated Cv while ensuring that it operates within its recommended range for optimal control.
Conclusion
Control valve sizing is a critical engineering task that demands meticulous attention to detail and a deep understanding of process dynamics. Accurate valve sizing ensures not only process efficiency and safety but also contributes to reducing operational costs by minimizing energy consumption and preventing equipment damage. By following the outlined steps and utilizing available standards and tools, engineers can effectively size control valves to meet the unique requirements of each process application.