The Precision Artistry of Cast Surface Plates A Cornerstone of Metrology
In the meticulous world of metrology, where accuracy and precision hold sway over the intricate dance of manufacturing and quality control, the cast surface plate stands as a silent yet indispensable protagonist. These seemingly humble slabs of metal, meticulously crafted through an age-old casting process, are the bedrock upon which the accuracy of countless measurements rests. This article delves into the essence of cast surface plates, their manufacturing nuances, and their pivotal role in ensuring that the products we rely on meet the highest standards of dimensional integrity.
**The Genesis of Precision Casting Process**
Cast surface plates originate from a fusion of art and science, born in foundries where molten metal is poured into molds to replicate intricate designs with stunning precision. Typically fabricated from iron or a specialized iron-based alloy, these plates harness the material's inherent damping properties to minimize vibrations that could disrupt measurement accuracy. The casting process itself is a testament to human ingenuity, involving careful selection of materials, precise mold design, and controlled cooling techniques to eliminate internal stresses and ensure a uniform, stable structure.
**Surface Finishing The Path to Perfection**
Once cast, the journey towards becoming a high-precision measuring tool is only just beginning. The raw surface plate undergoes rigorous machining and grinding processes to achieve a flatness and surface finish that rivals the stillness of a tranquil pond. Specialized grinding machines, often utilizing diamond abrasives, methodically remove minute layers of material until the plate's surface attains a level of flatness measured in millionths of a meter. This painstaking process guarantees that any object placed upon it will rest in perfect harmony with the plate's surface, enabling precise measurements free from form deviations.
**The Role in Metrology A Foundation for Accuracy**
Within the realm of metrology, cast surface plates serve as the fundamental platform for inspecting, calibrating, and verifying a myriad of tools and components
**The Role in Metrology A Foundation for Accuracy**
Within the realm of metrology, cast surface plates serve as the fundamental platform for inspecting, calibrating, and verifying a myriad of tools and components
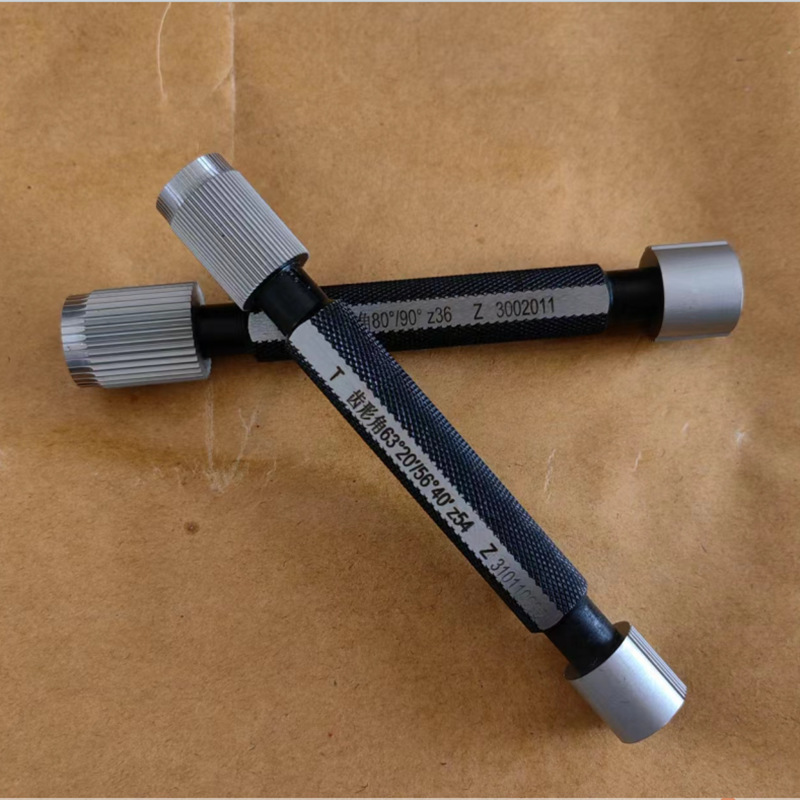
**The Role in Metrology A Foundation for Accuracy**
Within the realm of metrology, cast surface plates serve as the fundamental platform for inspecting, calibrating, and verifying a myriad of tools and components
**The Role in Metrology A Foundation for Accuracy**
Within the realm of metrology, cast surface plates serve as the fundamental platform for inspecting, calibrating, and verifying a myriad of tools and components
cast surface plate. They act as a reference standard against which other measuring instruments are checked, ensuring a traceable chain of dimensional accuracy throughout the manufacturing process. From aligning machine tools to inspecting intricate engine parts, surface plates facilitate the comparison of parts to engineering drawings, thus contributing to the overall quality and consistency of manufactured goods.
**Maintenance and Calibration Ensuring Longevity and Reliability**
Recognizing the criticality of their function, cast surface plates require diligent maintenance and periodic calibration to uphold their metrological integrity. Regular cleaning with soft cloths and approved solvents prevents contaminants from compromising the surface finish. Moreover, environmental conditions such as temperature and humidity must be controlled to minimize distortions. Professional recalibration services ensure that the plate's performance remains within specified tolerances over its lifetime, reinforcing its status as a reliable cornerstone of quality assurance.
**Conclusion A Testament to Precision Engineering**
In the grand symphony of industrial production, cast surface plates resonate as a harmonious note underscoring the quest for perfection. Far from being mere passive elements, they embody the pinnacle of precision engineering, silently facilitating the creation of everything from microscopic electronic components to colossal aerospace structures. As technology advances and manufacturing tolerances tighten, the importance of these meticulously crafted instruments only grows, affirming their irreplaceable role in the ongoing narrative of human progress and innovation.