In the highly demanding aerospace industry, precision is not just a requirement but a matter of safety and functionality. Cast iron surface plates play a crucial role in ensuring the accuracy of aerospace components. These plates, primarily crafted from Cast Iron (C.I), undergo meticulous heat treatment to relieve internal stresses, making them reliable and stable. Storaen (Cangzhou) International Trading Co., a renowned manufacturing powerhouse based in Botou, China, has been at the forefront of producing top-notch industrial products. Specializing in a wide array of items including cast iron welding platforms, precision measuring tools, and various gauges, their commitment to precision engineering and strict quality control makes them a trusted name. Cast iron surface plates and cast iron base plates from the company are essential for spotting, tool marking, workpiece inspection, and a multitude of gauging and layout operations in aerospace manufacturing. They serve as the precision reference that helps ensure every component meets the stringent aerospace standards. Let’s explore the significance and intricacies of cast iron surface plates in aerospace inspection.
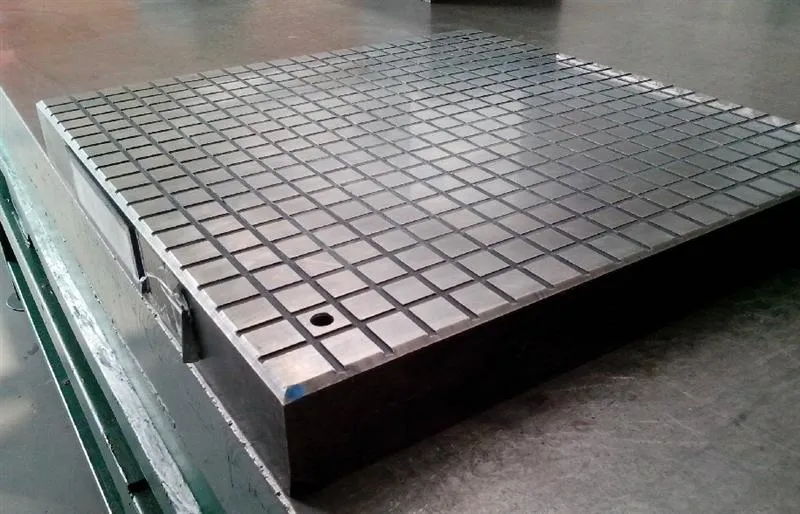
Importance of Cast Iron Surface Plates in Aerospace Inspection
- Precision Reference: In aerospace manufacturing, where even the slightest deviation can lead to catastrophic consequences, cast iron surface plates provide an unwavering precision reference. Whether it's checking the flatness of a wing component or the alignment of engine parts, these plates act as the baseline for accurate measurements. Their stable surface, achieved through heat treatment to relieve internal stresses, ensures consistent and reliable results during inspection.
- Quality Assurance: Cast iron surface platesare instrumental in quality assurance processes. By using them to inspect workpieces, manufacturers can identify any defects or inaccuracies early on. This helps prevent faulty components from progressing further in the production line, saving time, costs, and most importantly, ensuring the safety of aerospace vehicles. The reliability of cast iron base plates and cast iron lapping plates also contributes to maintaining the overall quality of aerospace products.
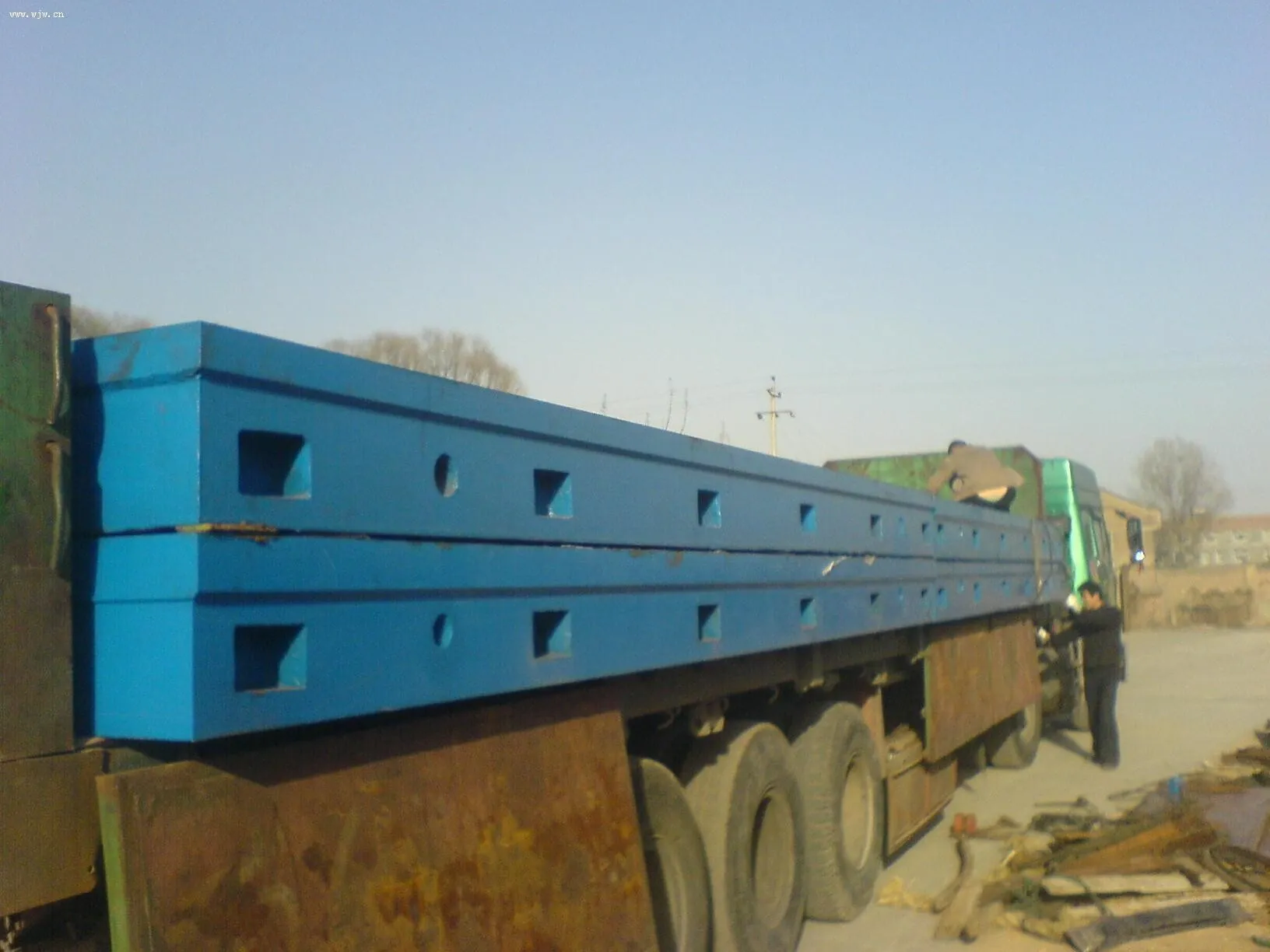
Types of Cast Iron Surface Plates and Their Aerospace Applications
- Cast Iron Surface Plates: These are the most commonly used in aerospace inspection. Their large, flat surfaces are ideal for checking the flatness and parallelism of various aerospace components. From fuselage panels to landing gear parts, cast iron surface platesprovide a stable platform for accurate measurements and visual inspections.
- Cast Iron Lapping Plates: In aerospace, where components require ultra-precise finishes, cast iron lapping platescome into play. They are used to achieve the smooth, flat surfaces needed for critical parts such as turbine blades and engine casings. The lapping process on these plates ensures that the components meet the strict surface roughness requirements of the aerospace industry.
- Cast Iron Base Plates: Cast iron base platesserve as the foundation for many aerospace inspection setups. They provide stability and support for other measuring instruments and fixtures. In assembly lines, these base plates help maintain the alignment of components during the inspection process, ensuring that measurements are taken accurately and consistently.
Plate Type
|
Key Feature
|
Aerospace Application
|
Cast Iron Surface Plates
|
Large, flat, stress-relieved surface
|
Checking flatness and parallelism of components
|
Cast Iron Lapping Plates
|
Enables ultra-precise surface finishing
|
Achieving smooth surfaces for critical parts
|
Cast Iron Base Plates
|
Provides stability and support
|
Serving as the foundation for inspection setups
|
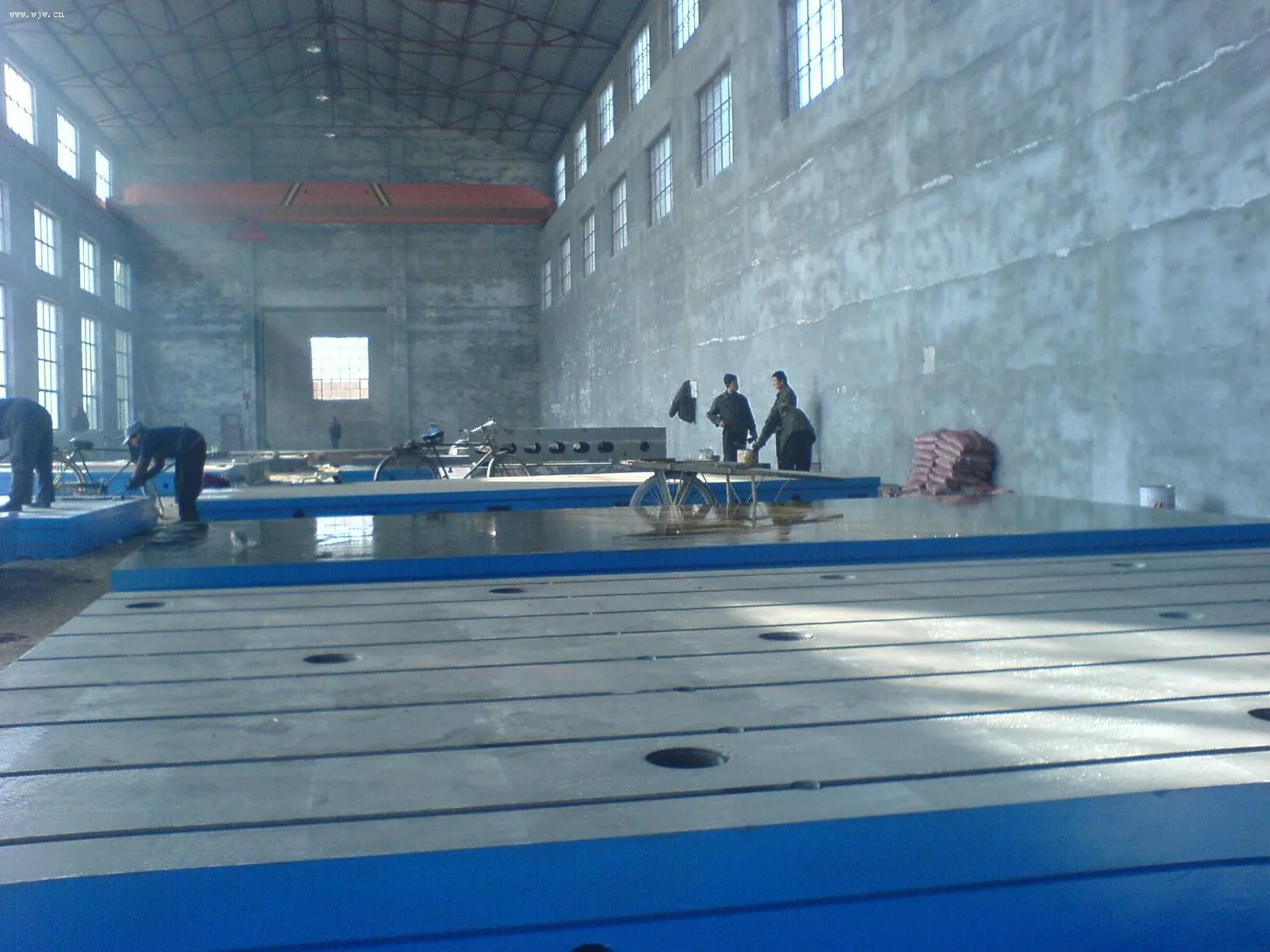
Inspection Criteria for Cast Iron Surface Plates in Aerospace
- Flatness: Flatness is one of the most critical criteria for cast iron surface platesin aerospace. Using precision measuring tools, inspectors check for any deviations from a perfectly flat surface. Even minute undulations can affect the accuracy of component inspections, so ensuring the flatness of these plates is paramount.
- Surface Roughness: The surface roughness of cast iron lapping platesand cast iron surface plates must meet aerospace standards. Rough surfaces can interfere with the accurate placement of components during inspection and may also cause scratches or damage. Specialized equipment is used to measure and verify the surface roughness, ensuring it is within the acceptable range.
- Stability and Durability: Given the high-stakes nature of aerospace manufacturing, cast iron base platesand other plates need to be stable and durable. Inspectors assess the structural integrity of the plates, looking for any signs of cracks, warping, or wear. A stable and durable plate is essential for long-term, reliable aerospace inspections.
-
Selecting the Right Cast Iron Surface Plates for Aerospace Inspection
- Manufacturer Reputation: When choosing cast iron surface plate or cast iron base platesfor aerospace inspection, the reputation of the manufacturer matters. Companies like Storaen (Cangzhou) International Trading Co., with their proven track record in precision engineering and quality control, are more likely to provide plates that meet the exacting standards of the aerospace industry.
- Specifications and Requirements: Different aerospace applications may have specific requirements for cast iron plates. Understanding these requirements, such as the required flatness tolerance, surface roughness, and size, is crucial for selecting the right plate. Matching the plate specifications to the inspection tasks ensures accurate and reliable results.
- Quality Assurance Measures: Look for manufacturers that have stringent quality assurance measures in place. This includes processes for stress relieving during production, thorough inspections before delivery, and certifications that attest to the quality of their cast iron plates. A manufacturer committed to quality assurance is more likely to deliver plates that are suitable for aerospace inspection.
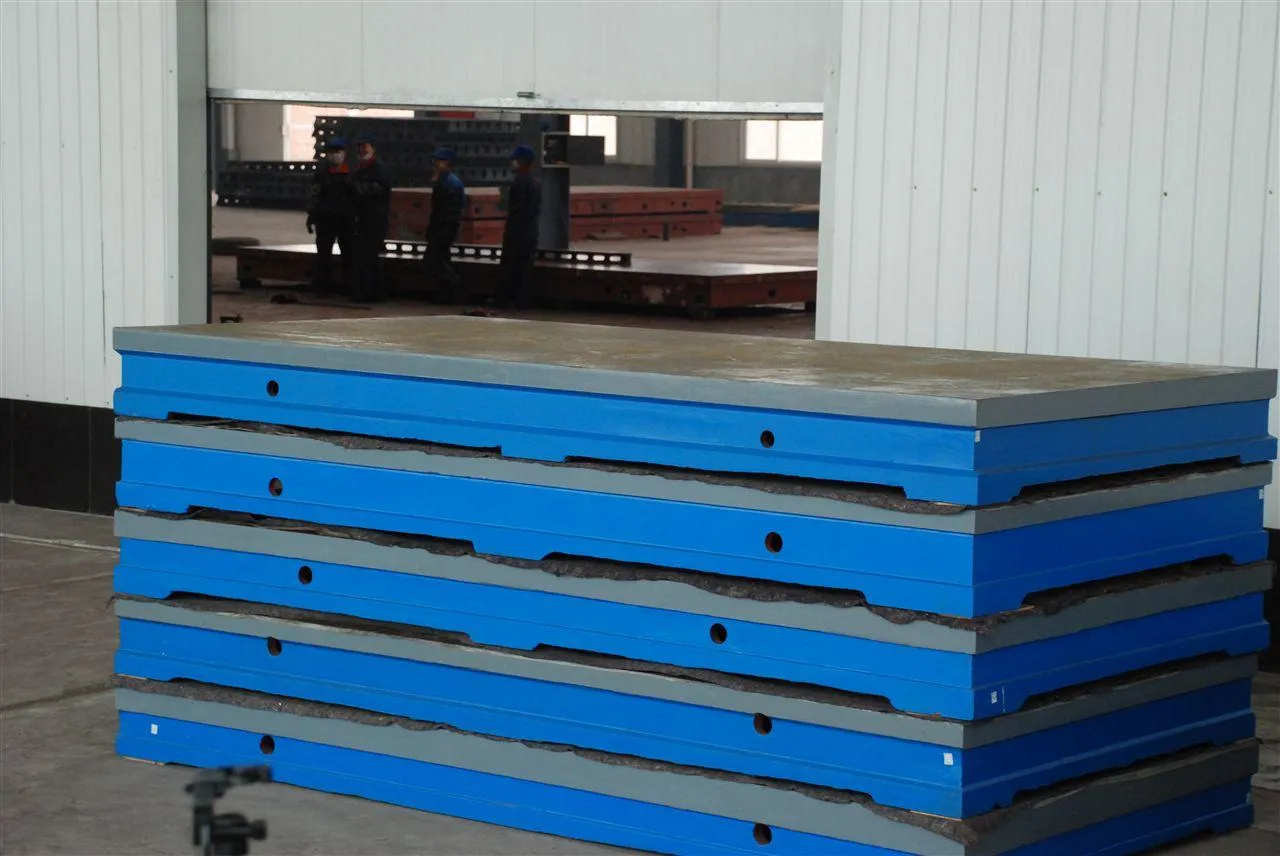
Cast Iron Surface Plate FAQS
How Often Should Cast Iron Surface Plates in Aerospace Be Calibrated?
The calibration frequency for cast iron surface plates in aerospace depends on several factors, such as the frequency of use and the criticality of the inspections. In general, they should be calibrated at least once a year. However, if the plates are used frequently in high-precision aerospace manufacturing processes, more frequent calibration, perhaps every six months, may be necessary to ensure their accuracy and reliability.
Can Cast Iron Lapping Plates Be Repaired if Damaged?
In some cases, cast iron lapping plates can be repaired if they are damaged. Minor surface imperfections or scratches can often be corrected through a process of re-lapping. However, for more severe damage, such as significant warping or deep cracks, it may be more practical to replace the plate. It's best to consult the manufacturer or a professional in the field to assess the extent of the damage and determine the most appropriate course of action.
What is the Ideal Temperature and Humidity for Storing Cast Iron Base Plates?
Cast iron base plates, like other cast iron plates, should be stored in a stable environment. The ideal temperature range is between 18 - 22°C (64 - 72°F), and the humidity should be kept between 40 - 60%. These conditions help prevent rusting, warping, and other forms of damage that could affect the performance of the plates during aerospace inspections.
How Do I Ensure the Flatness of a Cast Iron Surface Plate During Inspection?
To ensure the flatness of a cast iron surface plate during inspection, use precision measuring tools such as optical flats, laser interferometers, or electronic flatness testers. These tools can accurately detect any deviations from flatness. Additionally, make sure the plate is placed on a stable and level surface, and follow the proper measurement procedures recommended by the tool manufacturer for the most accurate results.
Where Can I Purchase High-Quality Cast Iron Plates for Aerospace Inspection?
For high-quality cast iron surface plates and cast iron base plates suitable for aerospace inspection, visit the official website of Storaen (Cangzhou) International Trading Co. With their expertise in manufacturing precision industrial products and a commitment to meeting the highest quality standards, they offer a wide range of reliable cast iron plates. Explore their product catalog, learn about the detailed specifications, and find the perfect plates to elevate your aerospace inspection processes to new heights of accuracy and reliability.
Ready to enhance the precision of your aerospace inspections? Head over to the www.strmachinery.com of Storaen (Cangzhou) International Trading Co. and discover our top-of-the-line cast iron surface plate and cast iron base plates. With our high-quality products, take your aerospace manufacturing and inspection to new levels of excellence!