In the realm of industrial and mechanical applications, ball check valves are fundamental components that ensure fluid dynamics operate effectively. These unassuming devices serve a critical purpose by allowing fluid to flow in a singular direction, thereby preventing backflow that can potentially lead to system malfunctions or failures. With increasing industry demands for efficiency and reliability, understanding the functionality, expertise involved in the design, and trustworthiness in the application of ball check valves is imperative.
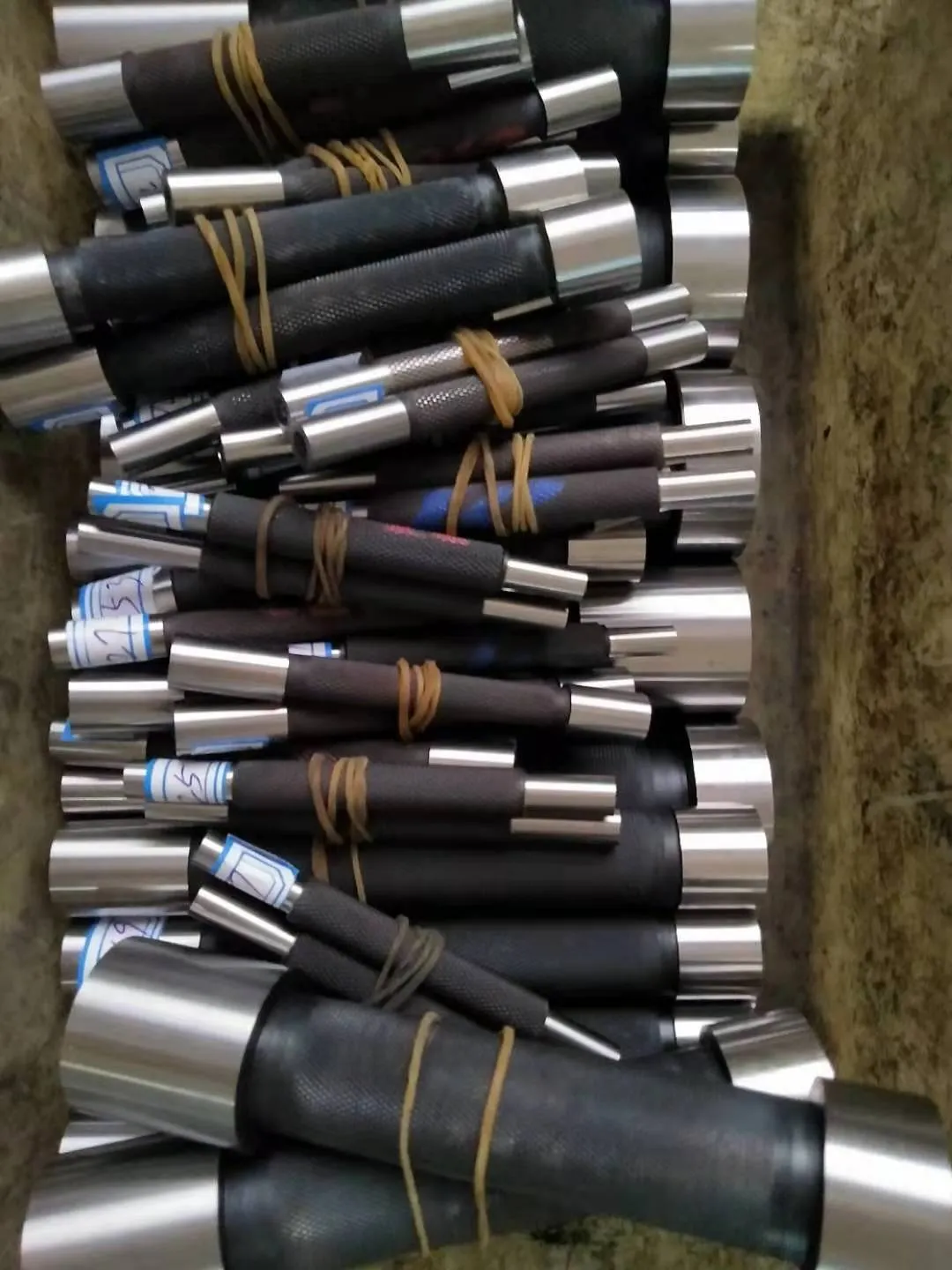
Ball check valves employ a straightforward mechanism that is a testament to skilled engineering. At their core, these valves utilize a spherical ball that rests on a seat. When fluid pressure from the inlet exceeds the force of gravity and potential system pressure at the outlet, the ball is lifted off its seat, allowing flow. Conversely, if the flow reverses or stops, the ball returns to its seat, sealing the valve to stop backflow. This simplicity belies the complexity and sophistication involved in the manufacturing and application processes, which have evolved to meet diverse industrial requirements.
The expertise in designing ball check valves lies in material selection, structural integrity, and operational efficiency. Materials commonly used range from stainless steel to specialized polymers, each selected based on the fluid type and operating environment. Manufacturers leverage advanced materials analysis to ensure that these valves withstand not only chemical corrosion but also various pressures and temperatures. Structural capabilities are rigorously tested through finite element analysis (FEA) to predict how the valve will perform under stress, while maintaining optimal flow characteristics.
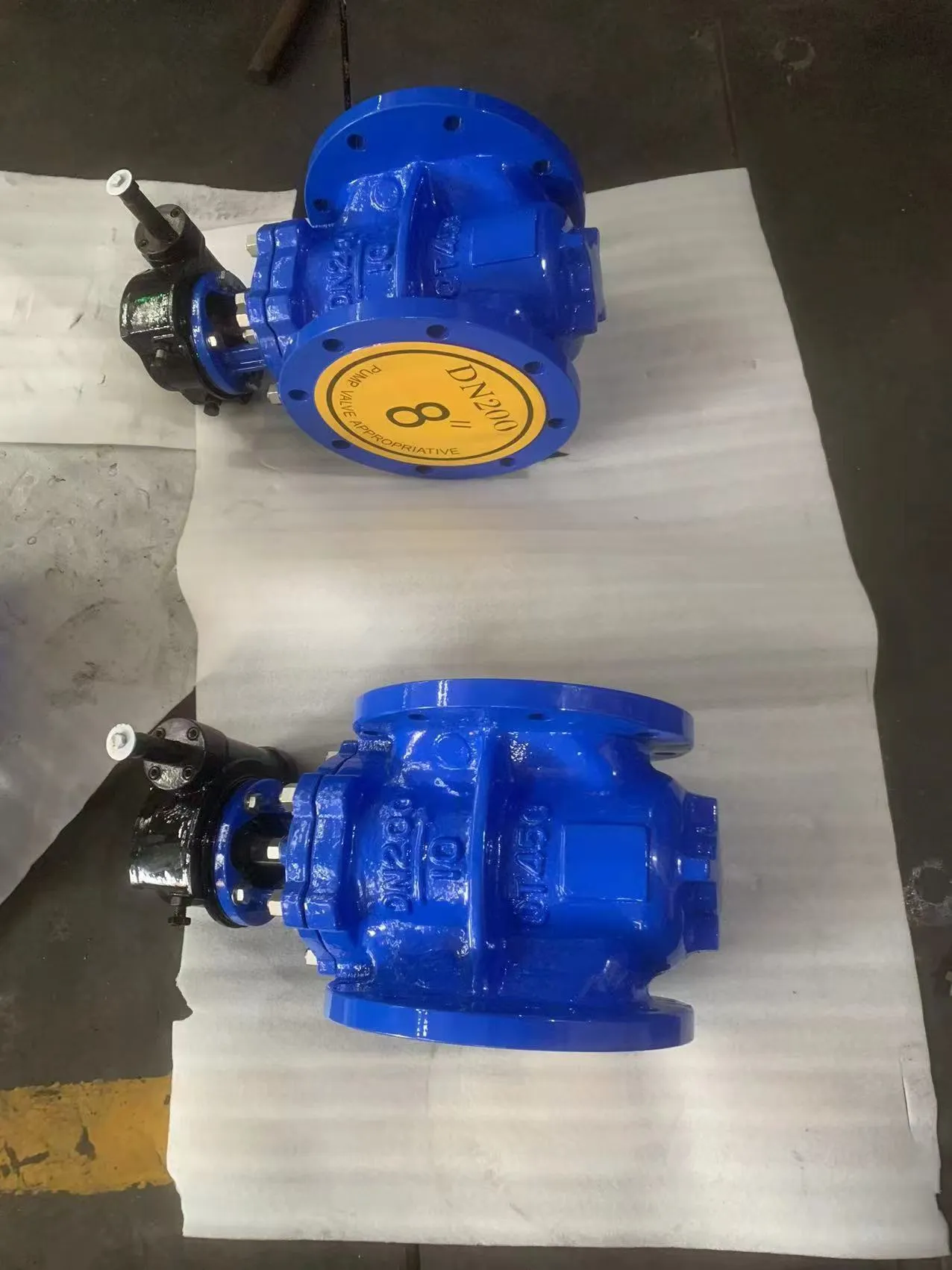
What elevates a ball check valve from a component to a critical system asset is its authoritativeness in operational reliability. Leading manufacturers, recognized for their technological innovation, integrate precision engineering and automation technology to calibrate the valves to strict tolerances. By utilizing computer-aided design (CAD) and computational fluid dynamics (CFD), these entities ensure their products meet industry standards and regulatory requirements. These validations confirm that the products will perform reliably across industries, including automotive, pharmaceutical, oil and gas, and water treatment.
ball check valve
In terms of making a choice based on trustworthiness, ball check valves are subjected to rigorous quality assurance protocols. Each valve undergoes stringent testing procedures—from lifecycle testing to high-pressure testing—to guarantee performance stability. Trust is further cemented by a manufacturer's history and customer testimonials, which often highlight the dependability of the product under dynamic conditions. Certifications from ISO and other quality standards bodies serve as third-party endorsements that incentivize stakeholders in selecting these components for sensitive applications.
Beyond theoretical knowledge, practical experience with ball check valves provides a real-world perspective on their indispensability in systems management. Professionals across engineering fields acknowledge the peace of mind these valves bring—offering a defense against catastrophic failures in pressurized systems. In maritime applications, the use of ball check valves in ballast systems is a prime example, where they ensure the correct flow of water, hence maintaining ship stability and safety.
The expertise in application does not conclude at installation; it extends to maintenance where predictive maintenance technologies now play a crucial role. Utilizing sensors and IoT devices, the predictive analysis can identify wear and potential failure points before they escalate into significant issues. Proactive valve maintenance not only extends the life of the valve but also ensures the entire system remains operational without unexpected downtimes.
In summation, the unyielding demand for components that balance simplicity with advanced operational requirements makes ball check valves indispensable in modern industry. The synthesis of material science, engineering expertise, authoritative manufacturing practices, and a commitment to reliability forms the cornerstone of their value proposition. Industry experts and new entrants alike would do well to consider these factors when integrating ball check valves into their systems, ensuring they choose solutions that align with both current needs and future innovations. This guarantees not only optimal system functionality but also fortifies structural resilience against the evolving challenges of industrial applications.