Understanding the Function and Importance of 5 8 Check Valves
In the world of fluid dynamics and engineering systems, the term 5 8 check valve holds significant relevance. This specialized component plays a crucial role in ensuring the efficient and safe operation of various industrial processes. A check valve, by definition, is a non-return valve that allows fluid to flow in only one direction, preventing backflow and maintaining the desired flow sequence.
The 5 8 check valve terminology might be a bit misleading due to the unconventional representation. It's possible that the numbers refer to a specific size or rating, such as pressure or flow rate, which is not standard in the industry. However, let's delve into the general principles and importance of check valves in the context of fluid control systems.
A check valve operates based on the principle of gravity and fluid pressure. When fluid flows in the intended direction, it pushes the valve open, allowing passage. In contrast, when the flow attempts to reverse, the valve's closure member, usually a spring or a float, shuts, obstructing the flow path. This mechanism ensures that fluids, gases, or slurries move in a unidirectional manner, protecting pumps, pipelines, and other equipment from damage that could result from backpressure This mechanism ensures that fluids, gases, or slurries move in a unidirectional manner, protecting pumps, pipelines, and other equipment from damage that could result from backpressure
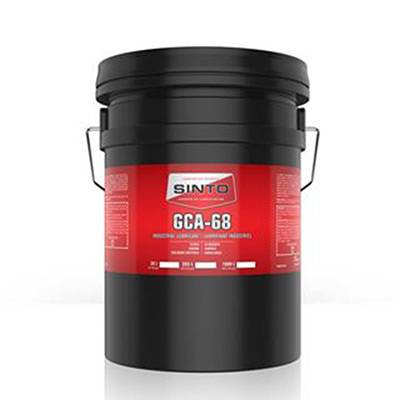
This mechanism ensures that fluids, gases, or slurries move in a unidirectional manner, protecting pumps, pipelines, and other equipment from damage that could result from backpressure This mechanism ensures that fluids, gases, or slurries move in a unidirectional manner, protecting pumps, pipelines, and other equipment from damage that could result from backpressure
5 8 check valve.
The 5 8 check valve, if indeed representing a unique specification, could denote a valve designed for specific pressure or flow conditions. For instance, it might indicate a valve rated for a maximum working pressure of 500 pounds per square inch (psi) or a flow rate of 80 gallons per minute (gpm). These parameters would make the valve suitable for high-pressure or high-flow applications, such as oil and gas, water treatment, or chemical processing plants.
Moreover, check valves come in different types, including swing check, lift check, diaphragm check, and spring-loaded check valves, each with its own advantages and applications. The choice of the right type is crucial to optimize system performance and prevent potential issues like water hammer or pressure surges.
In conclusion, while the specifics of a 5 8 check valve may require clarification, the broader concept of check valves underscores their critical function in fluid systems. They serve as guardians against backflow, safeguarding equipment, and maintaining operational integrity. Engineers and technicians must understand these valves' functioning and select the appropriate ones for their specific applications to ensure safety, efficiency, and reliability in their systems.