The 4-inch ball check valve stands as an essential component in a wide array of industrial applications, playing a pivotal role in ensuring the seamless operation of fluid handling systems. This article delves deep into understanding the intricacies, benefits, and operational excellence of the 4-inch ball check valve, providing an unmatched guide for industry professionals and decision-makers.
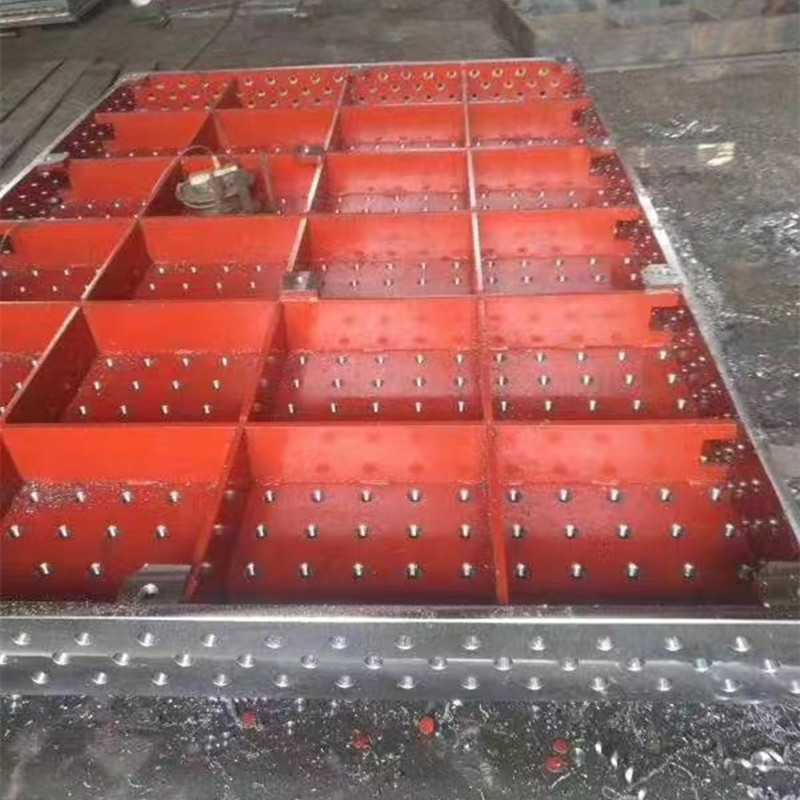
Ball check valves are fundamental in their design, primarily enabling fluids to flow in one direction while preventing undesirable backflow. The 4-inch dimension signifies a robust capacity, suitable for substantial volume handling without compromising efficiency or reliability. These valves are inherently passive, activating through the flow of fluid itself, thus negating the need for manual operation or external control mechanisms. This passive operation not only enhances reliability but also decreases maintenance demands, positioning them as a cost-effective solution across industries.
Operationally,
the 4-inch ball check valve comprises a spherical ball which acts as the closing member. When fluid pressure is exerted on the inlet side, it lifts the ball off its seat, allowing flow to proceed. Conversely, if a reverse flow occurs, the ball returns to its seat, effectively sealing off the passage. Expertly engineered, the precision seating minimizes leakage, a critical requirement for maintaining system integrity, especially in sectors handling hazardous or precious materials.
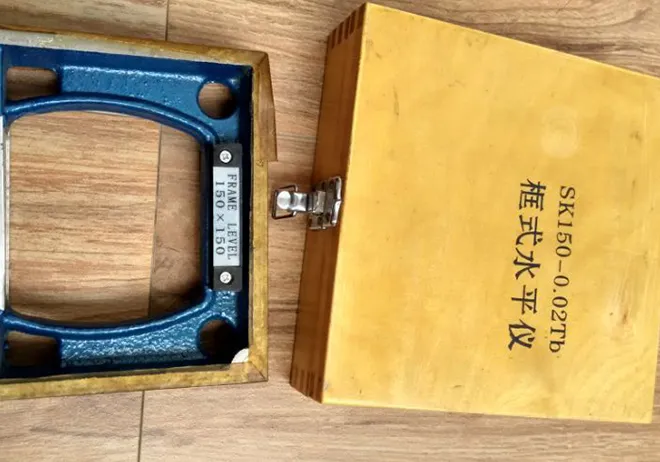
The 4-inch ball valve's construction typically features durable materials such as stainless steel, PVC, or cast iron, each selected based on the specific needs of an application. Stainless steel variants boast corrosion resistance, making them ideal for the chemical processing and pharmaceutical industries. Meanwhile, PVC models cater excellently to water and waste management systems due to their cost-effectiveness and ease of installation. Regardless of material, the commonality lies in the assurance of durability and operational longevity.
Moreover, the simplicity of the design belies its sophisticated efficacy. With a minimalistic approach, ball check valves reduce pressure loss within systems, optimizing energy efficiency and aligning with growing industrial sustainability goals. The valve's capacity to operate within varied temperature ranges further broadens its applicability from hot water systems to cryogenic operations, underscoring its versatility and unmatched functionality.
4 inch ball check valve
Proven in both small-scale and large-scale operations, 4-inch ball check valves are indispensable in scenarios demanding high reliability and low downtime. Industries such as petrochemical, marine, and HVAC systems rely heavily on these components to maintain consistent operations. In these environments, the stakes are high, and the competence of every single part is non-negotiable. The ball check valve's reliability lies not just in its design but in its rigorous testing, often adhering to industry standards such as ANSI, API, or ISO certifications, which vouch for their credibility and quality assurance.
However, despite their durability, the maintenance of these valves shouldn’t be neglected. Regular inspections can preclude potential system failures, ensuring prolonged efficiency. Indicators such as unusual noise or vibration can flag issues that might require addressing to prevent larger system disruptions. Expert insights often suggest the integration of condition monitoring systems for critical installations, providing real-time data and predictive maintenance capabilities.
In essence, the value of the 4-inch ball check valve in modern industrial contexts cannot be understated. It balances simplicity with sophistication, durability with efficiency, and cost-effectiveness with reliability. As industry demands evolve, so will the developments in ball check valve technology, potentially incorporating smart diagnostics and more refined materials, ensuring they continue to meet, if not exceed, future expectations. The strategic implementation of these valves can lead to significant improvements in operational fluidity, safety, and cost management, making them an intelligent choice for industry leaders focused on optimized performance and longevity.
In conclusion, the 4-inch ball check valve emerges as more than just a functional component; it is a linchpin of fluid management systems that underscores the intersection of engineering excellence and practical utility. Its seamless blend of performance, resilience, and adaptability paves the way for enhanced industrial processes, reflecting a commitment to quality and sustainable innovation. For industry stakeholders, the inclusion of such a reliable component not only secures contemporary operations but sets a benchmark for future advancements in fluid dynamics and system efficiencies.