Welding V blocks are essential tools in the precision engineering sector. These versatile devices hold workpieces, usually metal rods, securely in place during welding, allowing for precise and consistent outcomes. The intricacies involved in making these blocks functional under various conditions have been mastered only by those who understand materials, machining, and welding techniques comprehensively.
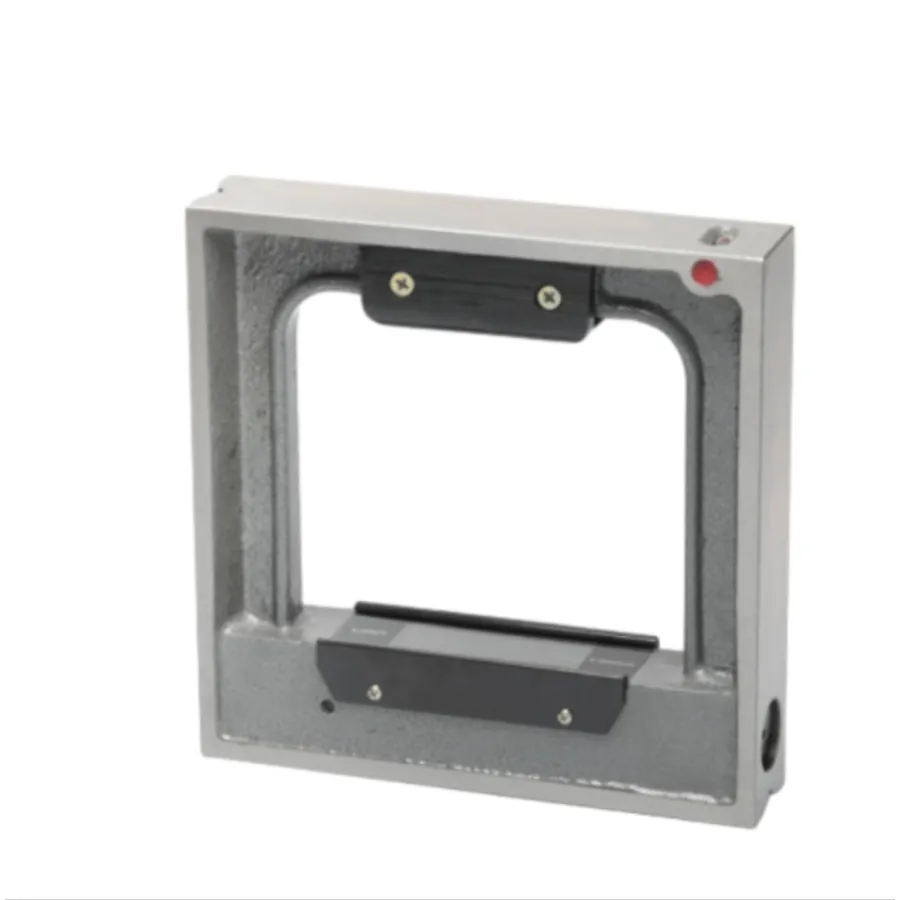
Precision in welding is crucial for many industries, including automotive, aerospace, and construction. A minor deviation in welding can lead to significant safety issues, which is why tools like V blocks are indispensable. Typically constructed from hardened steel to withstand high temperatures and pressures, their maintenance and selection play pivotal roles in ensuring the highest quality of the welded product.
The process of selecting the right V block begins with understanding the specific welding needs. Different metal types require varying V block materials. For instance, while steel V blocks are ideal for high-temperature welding projects, aluminum blocks might be more suitable for lighter, less intense jobs. This flexibility in material choice helps professionals achieve the best possible outcomes while maintaining safety standards.
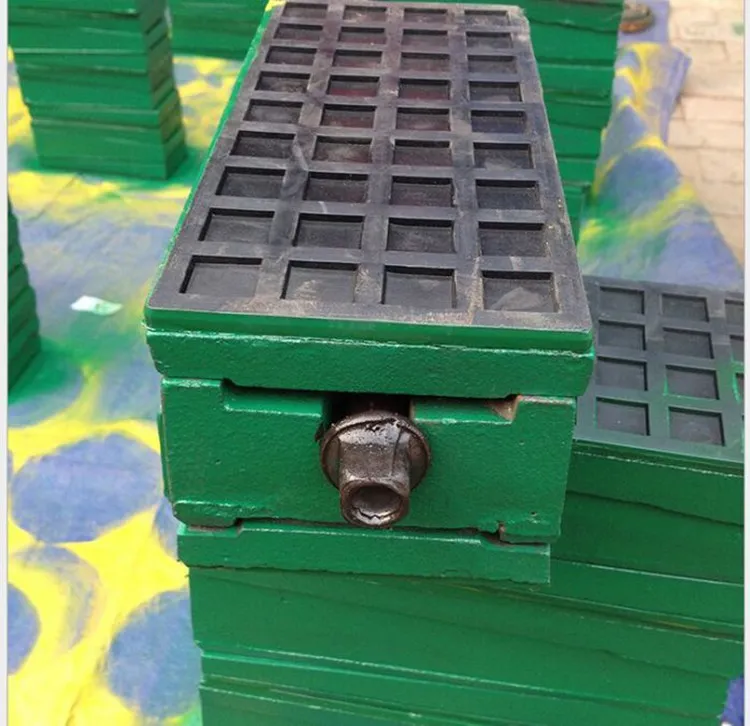
Expert welders stress the importance of V block alignment. An aligned V block ensures uniform pressure distribution across the workpiece, minimizing warping or distortion, which is critical in products that demand high precision. The V blocks' ability to accommodate various angles further enhances their usability, making them a staple in weld shops worldwide.
Authoritative voices in the welding industry advocate for regular V block maintenance. Over time, residues from weld spatter and metal shavings accumulate on the block surfaces, leading to inaccuracies and slippage. Cleaning the blocks with appropriate solvents followed by lubrication ensures their longevity and optimal performance. Implementing a routine maintenance schedule safeguards the integrity of both the V blocks and the welding processes they support.
welding v block
Trust plays a significant role when considering V block manufacturers. Brands with a proven track record of reliability and quality often become the default choice for serious craftsmen. Many industry professionals recommend seeking manufacturers who offer warranties and comprehensive customer support. Access to a knowledgeable customer service team can make a significant difference, particularly when troubleshooting complex welding setups.
Innovation is also influencing the evolution of welding V blocks. Smart V blocks equipped with sensors are gradually entering the market, providing welders with real-time data on pressure distribution and temperature. This advancement not only enhances welding precision but also serves as a preventive mechanism against operational errors.
Whether a beginner or a seasoned expert, understanding the nuances of V block usage elevates the overall quality of welding projects. The right application of these insights ensures the creation of durable, high-quality welded structures, reflecting expertise in metalwork and precision engineering.
Incorporating the latest technology into welding practices necessitates continuous learning. Establishing a strong foundational knowledge in V block utilization can significantly impact one's effectiveness and efficiency in welding tasks. Networking with industry peers and participating in specialized workshops are practical ways to stay updated on the latest developments. Such engagement showcases one's commitment to their craft and highlights professionalism.
Ultimately, the blend of precise tools, expert knowledge, and consistent innovation defines success in welding. V blocks, seemingly simple tools, play a critical role in this equation, demonstrating how foundational elements are often at the heart of sophisticated engineering solutions.