Clamps for welding fixtures are essential tools in the fabrication industry, yet many professionals overlook their importance, focusing instead on more glamorous machines and technology. However, it's these seemingly humble tools that significantly enhance efficiency, precision, and safety in welding operations. Drawing from years of experience and expertise, this article delves into the indispensable role of clamps in welding fixtures, providing insights into their selection, application, and maintenance, thereby emphasizing their authoritative place in any welders' toolkit.
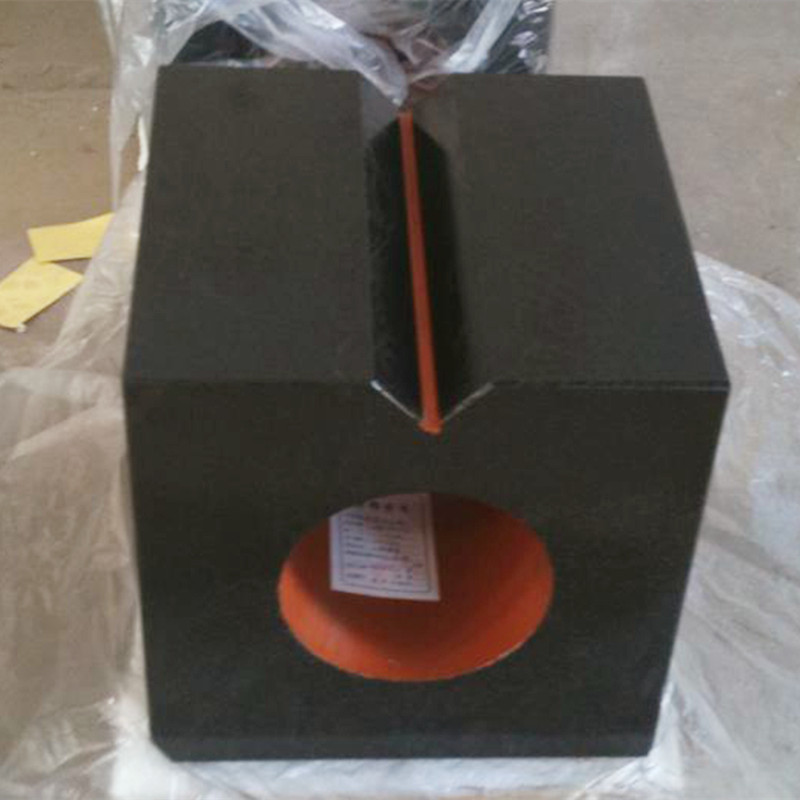
The primary function of clamps in welding is to securely hold metal pieces in place, ensuring precision in alignment and positioning during the welding process. This accuracy is paramount, as even a millimeter's shift can result in structural weaknesses or defects. My years working in metal fabrication have shown time and again that the consistency provided by quality clamps helps to minimize errors, leading to superior and reliable welds.
When selecting clamps for welding fixtures, it's crucial to consider several factors to maximize their functionality. The material strength of the clamp is vital; it must be robust enough to withstand the pressures of welding without warping or degrading. Stainless steel and high-grade alloys are often preferable for their durability and resistance to corrosion. Adjustable features are also a must, as they provide the flexibility needed to accommodate different sizes and shapes of workpieces. Moreover, ease of use is a factor that cannot be ignored; quick-release mechanisms, for instance, can significantly speed up work processes, enhancing efficiency in busy workshops.
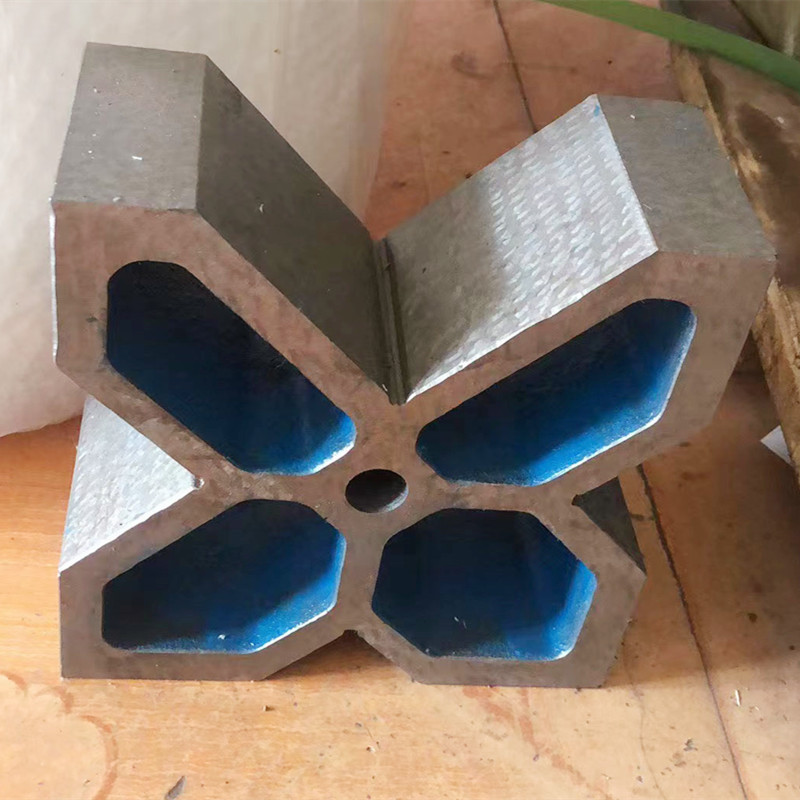
Expert welders understand that different projects demand different types of clamps. For instance, toggle clamps are excellent for repetitive production jobs due to their fast and secure locking action. C-clamps, with their versatile adjustability, are often used in heavy-duty applications where significant pressure is required. In contrast, pipe clamps are specifically designed to handle cylindrical objects, making them indispensable in plumbing and gas fitting tasks. By selecting the appropriate clamp for a project, welders can ensure stability and safety, maintaining high standards of quality and reliability.
clamps for welding fixtures
Maintenance of clamps is as vital as their proper selection and usage. After years of field experience, it’s clear that regularly checking clamps for signs of wear and tear is crucial for safety and performance. Inspecting screw threads for stripping, ensuring moving parts are well-lubricated, and checking for any rust or corrosion will extend the lifespan of the clamps.
Reliable clamps lead to reliable welds, making maintenance an area that should not be overlooked by professionals seeking trusted results.
In terms of authoritativeness, understanding how clamps integrate into a broader workflow is key. In my advisory roles across various fabrication shops, I’ve seen firsthand how misplaced priorities can lead to time loss and increased risk of accidents. By implementing a comprehensive system where clamps are properly selected, used, and maintained, welding operations become significantly more efficient. This not only enhances productivity but also builds a strong reputation for quality within the industry, reinforcing a company's authority and credibility.
Trustworthiness in the context of welding clamps is achieved through consistent results and the longevity of tools. Clients rely on precision-crafted products, and the reliability provided by well-maintained clamps ensures that every weld meets rigorous standards. For instance, custom fabrication shops that focus on automotive parts must guarantee their welds can withstand high stress and impact, something that is only possible when clamps are correctly used to maintain alignment and pressure during welding.
In conclusion, clamps for welding fixtures are more than mere accessories; they are critical components in the art and science of welding. Their role in ensuring precision, enhancing efficiency, and maintaining safety cannot be overstated. Professionals who leverage the right clamps for their specific needs, maintain them properly, and integrate them seamlessly into their workflow are well-positioned to deliver superior results, bolster their credibility, and build trust with their clients, thereby setting a lasting standard of excellence in the welding industry.