Check valves, essential components in numerous industrial and household applications, come in various designs suited to specific needs.
Recognizing the differences among these types contributes to more effective and reliable system operations. This article delves into the distinct types of check valves, highlighting their unique features, advantages, and common applications, providing insights from seasoned professionals in the field.
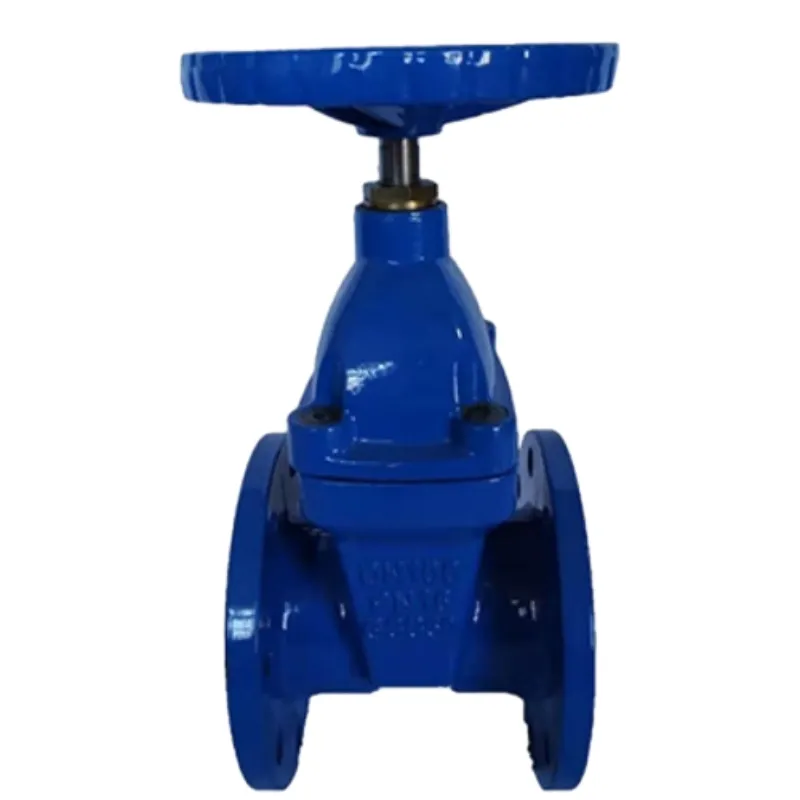
Swing check valves are among the most commonly used types, recognized for their simple yet effective design. They utilize a swinging disc that moves away from the valve seat to allow flow in one direction and returns to its seat when the flow stops, preventing backflow. These valves are prized for their low-pressure drop when fully open, making them ideal for applications involving frequent flow changes. Industries like water and wastewater management, oil, and gas often favor swing check valves due to their durability and ease of maintenance.
In contrast, lift check valves feature a disc that moves perpendicularly to the seat, necessitating a greater force to lift the disc compared to swing designs. This characteristic makes lift check valves suitable for high-pressure applications where a quick response to closing is paramount. Their compact design allows for use in tight spaces, and they are often found in steam, gas, and liquid applications where secure flow regulation is crucial.
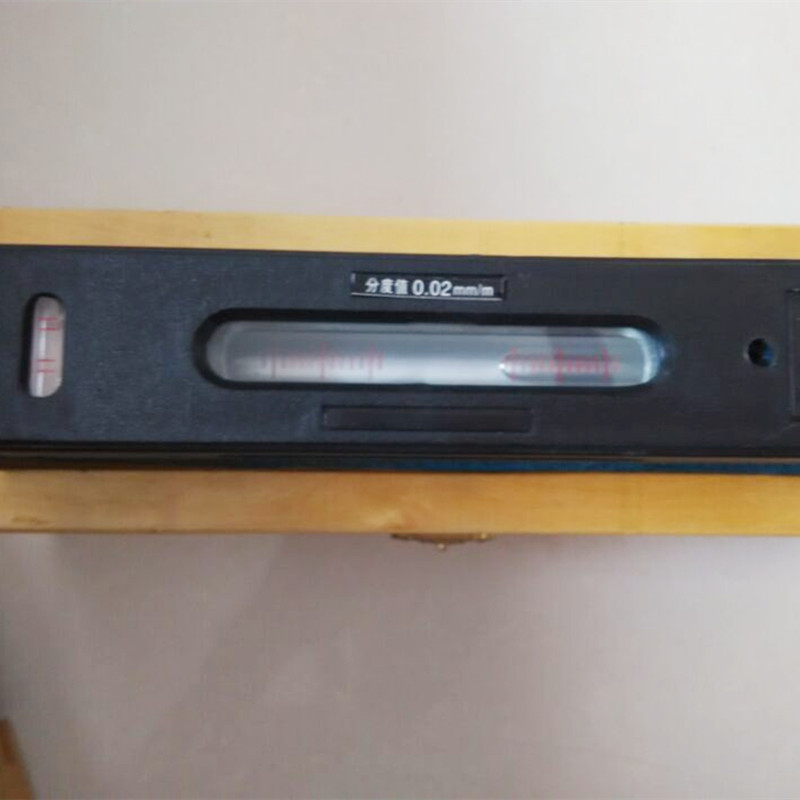
Ball check valves utilize a spherical ball to block backflow, commonly employed in systems where complete closure is necessary. These valves tend to be self-cleaning, as the ball rotates during operation, preventing buildup of debris and wear. With their ability to handle viscous fluids, ball check valves are particularly advantageous in chemical and food processing industries, where cleanliness and minimal maintenance are prioritized.
different types of check valves
Diaphragm check valves incorporate a flexible diaphragm to form a seal, automatically responding to flow pressure. Their design eliminates the risk of backflow contamination, making them perfect for applications requiring strict hygiene standards, such as in pharmaceutical and food processing industries. Moreover, diaphragm check valves are well-suited for handling corrosive fluids as they reduce potential leak points and ensure product integrity.
Wafer check valves, known for their compact and lightweight design, fit snugly between two flanges in a piping system. They are preferred in systems where space constraints are a consideration. Wafer check valves offer low-pressure drop and minimal fluid resistance, being widely used in water systems, heating, ventilation, and air conditioning (HVAC) applications.
The dual-plate check valve, another variation, features two spring-loaded plates that close upon reverse flow. This design is highly efficient in systems with variable flow conditions, providing rapid closure without slamming. Industries facing turbulent flow conditions, such as petrochemical plants, often adopt dual-plate check valves due to their robustness and reliable performance.
In summary, the selection of a check valve type hinges on understanding the specific operational demands and environments. Experience in choosing the appropriate valve contributes significantly to system efficiency and longevity. Experts consistently emphasize the importance of assessing factors such as pressure, temperature, flow rate, and fluid characteristics when deciding on the suitable check valve. Prioritizing quality and compatibility with the system will ensure that check valves perform optimally, safeguarding against costly downtimes and ensuring seamless operations in various industrial landscapes.