The 8 check valve, a critical component in various industrial systems, plays an essential role in ensuring the unidirectional flow of fluids. In industrial applications, ensuring fluid control efficiency is key to maintaining operational integrity, safety, and reducing downtime. Understanding the intricacies of 8 check valves equips businesses and technical experts with the knowledge to select, maintain, and optimize these components for enhanced system performance.
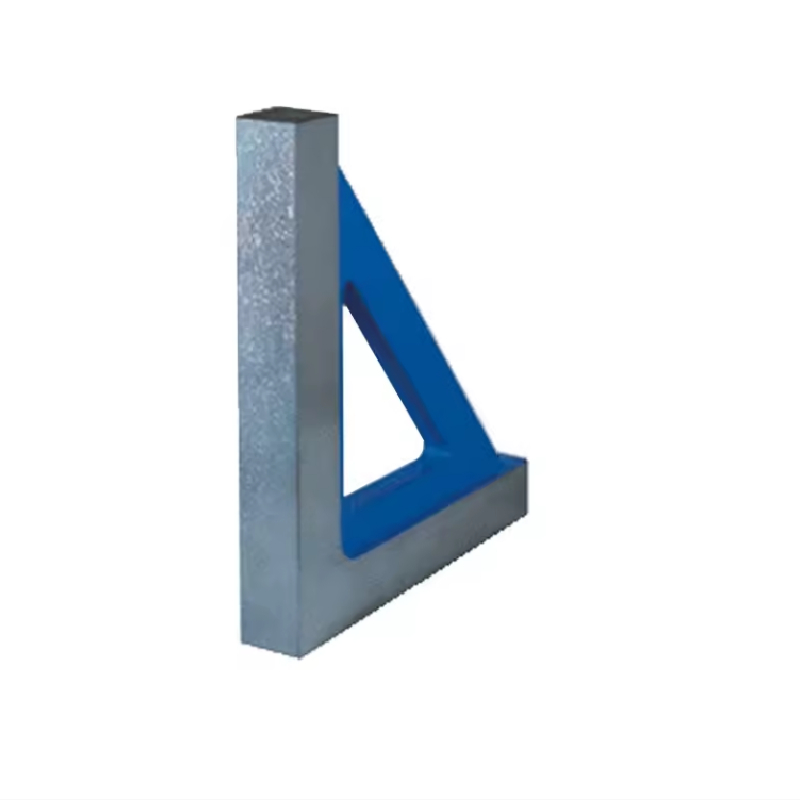
Check valves, though simple in design, are crucial in preventing backflow, which could compromise system integrity, leading to potential safety hazards and costly repairs. The 8 check valve is particularly vital for larger piping systems where substantial fluid volumes need regulation. These valves are engineered to automatically allow flow in one direction while preventing it in the opposite, using various mechanisms such as swing, lift, or dual plate designs.
Expertise in the selection of the right type of 8 check valve is paramount. Factors to consider include the medium type - whether liquid, gas, or slurry, as well as pressure, temperature, and flow velocity. For instance, swing check valves, with their pivoting disc design, are ideal for applications requiring low-pressure drops and are commonly used in water and wastewater systems.
Contrastingly, lift check valves excel in high-pressure environments and are often applied in steam and water systems.
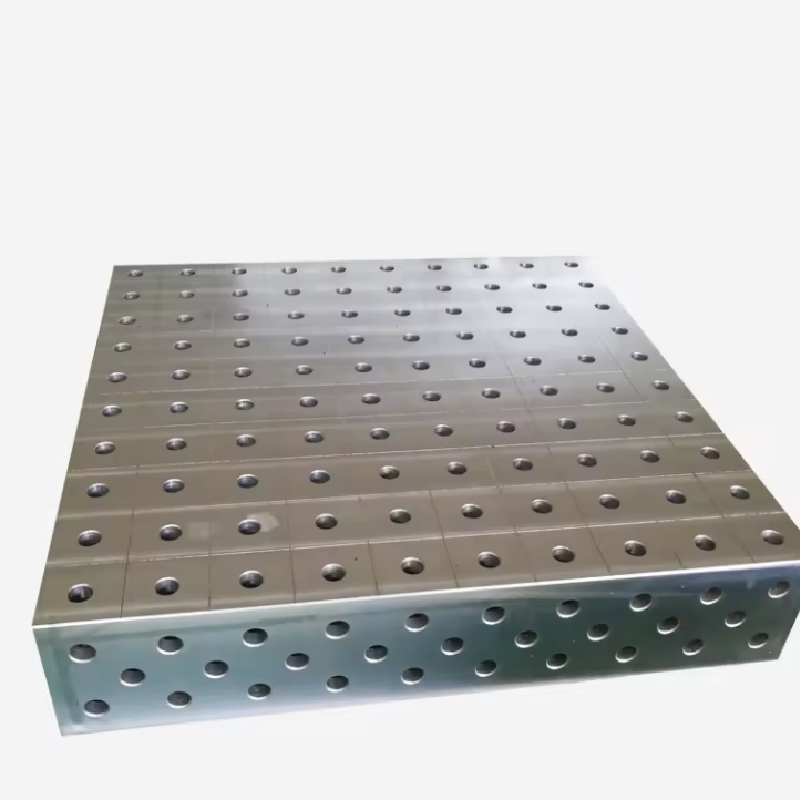
Authoritativeness in the application of 8 check valves is demonstrated through thorough testing and adherence to international standards such as API, ASME, and ISO. These standards ensure that the valves operate optimally under specified conditions and can withstand the rigorous demands of industrial operations. Investing in check valves from reputable manufacturers who comply with these standards guarantees reliability and longevity.
8 check valve
From an experiential perspective, incorporating 8 check valves into systems leads to enhanced operational reliability. Real-world case studies highlight how industries have minimized downtime and maintenance costs by adopting modern check valve technologies designed for longevity and robust performance under extreme conditions. For example, refineries have reported reductions in fluid hammer incidents, which can cause catastrophic pipeline failure, by replacing traditional swing check valves with advanced spring-loaded designs that cushion sudden changes in fluid dynamics.
Trustworthiness in deploying 8 check valves also stems from regular maintenance and inspection. Industries adopting a proactive approach can avert potential malfunctions. Routine checks ensure that valves are free of debris, corrosion, and wear, and that they maintain their sealing capabilities. Operators trained to recognize early warning signs of check valve failure can preemptively address issues before they escalate.
In summary, the deployment of 8 check valves in industry settings underscores a commitment to maintaining fluid control integrity and operational efficiency. Their proper selection, adherence to global standards, and regular maintenance are pillars that support their reliability and performance. Industries that prioritize these aspects not only safeguard their operations but also optimize their production capabilities, reaffirming the crucial role of 8 check valves in modern industrial applications.