Precision gauge tools, often the unsung heroes of the industrial and manufacturing worlds, play a pivotal role in ensuring product excellence. Crafted for meticulous measurement, these instruments thrive in environments where precision is paramount, making them indispensable in the quest for quality.
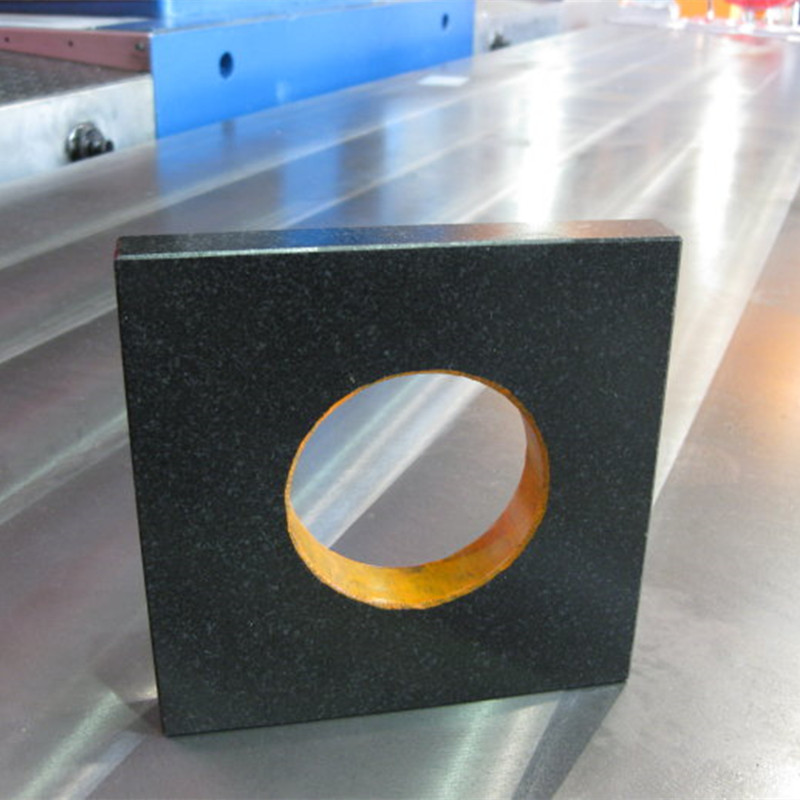
Experience reveals that selecting the right precision gauge is crucial—many seasoned professionals would attest to this. Whether in automotive, aerospace, or electronics industries, the relevance of precision gauges cannot be overstated. These tools guarantee that every component manufactured meets stringent standards, thereby preventing costly recalls and ensuring customer satisfaction.
Expertise in the field underscores that understanding the nuances of precision gauges enhances their utility. These devices range from simple dial indicators to highly sophisticated digital models that integrate with computer systems for real-time data analysis. The choice of gauge will depend on several factors the specific requirements of the measurement task, the environment within which measurements are taken, and the degree of accuracy required. Having a comprehensive understanding of these elements aids professionals in making informed decisions that impact production quality and operational efficiency.
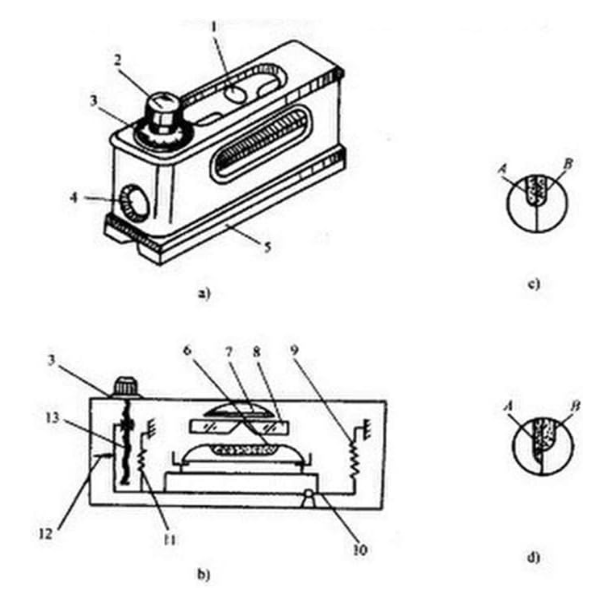
In terms of authoritativeness, precision gauges have a storied history of reliability. Industry standards such as ISO 9001 and ISO 17025, which regulate quality management systems and laboratory competence respectively, frequently call for measurements verified by precision instruments.
Laboratories and workshops worldwide count on gauging tools to meet these international standards. This reliance on precision gauges has positioned them as authoritative tools within quality assurance systems.
Trustworthiness of precision gauges is tested over time. Brands renowned for their consistent performance and reliability, such as Mitutoyo and Starrett, owe their reputations to years of stringent quality control and innovation. These brands invest heavily in technology advancements, ensuring their gauges not only meet current demands but anticipate future measurement challenges.
precision gauge
The product lifecycle of precision gauges is another aspect that bolsters their trustworthiness. High-quality gauges are designed for durability, with some models enduring work environments characterized by vibration, temperature fluctuations, and exposure to various substances. Maintenance of precision gauges generally involves regular calibration, a process essential not just for maintaining accuracy, but also for prolonging the functional lifespan of the instrument. Manufacturers often offer calibration services and provide guidelines that help users maintain the precision and usability of their gauges over time.
Precision gauges evolve with technology, and modern innovations are increasingly shaping how industries use these tools. Connectivity options such as Bluetooth and wireless data transfer allow for seamless integration into larger digital ecosystems. This advancement enhances real-time sharing of measurement data, facilitating faster decision-making processes and streamlining production workflows. Furthermore, such connectivity bolsters the ability to conduct remote diagnostics, reducing downtime and promoting efficiency.
Reliability in results also speaks to the trust placed in precision gauges. The advent of advanced materials and sensor technologies has further improved measurement accuracy, offering resolutions that satisfy the most demanding of applications. Such precision is especially crucial in high-stakes industries—like aerospace—where measurement errors can lead to catastrophic outcomes.
To ensure optimal performance of precision gauges, proper usage is key. Training personnel on accurate handling and reading techniques prevents errors and maximizes the gauge’s potential. This aspect of user competence ensures that the instrument's integrity is not compromised, keeping the focus on producing results that meet or exceed expected standards.
In conclusion, the indispensable nature of precision gauges in the production landscape emanates from their irrefutable experience, expertise, authority, and trustworthiness. As technology advances, so too must the tools of precision, ensuring they remain relevant and continue to pave the way for excellence in manufacturing. As such, maintaining a keen awareness of innovations within this field is necessary for any entity aiming to harness the full potential of precision measurements.