Flanged check valves are a pivotal component in many industrial applications due to their ability to facilitate unidirectional flow and prevent reverse flow within a piping system. Their robust design and reliable operation make them an ideal choice for ensuring system integrity and operational efficiency. As industries evolve and demand more efficient systems, the expertise surrounding the selection, installation, and maintenance of flanged check valves becomes increasingly important.
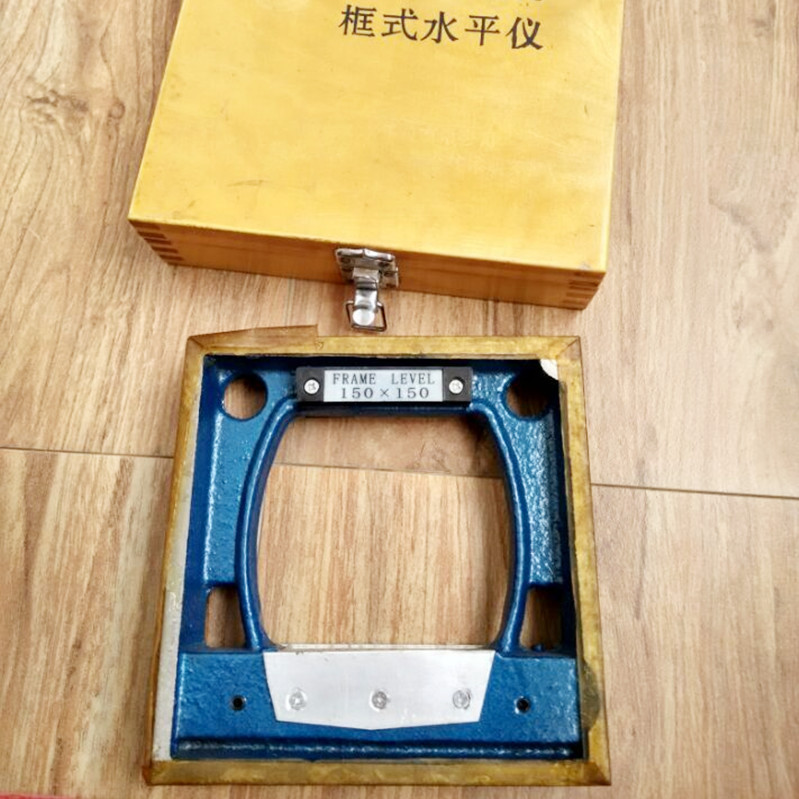
In-depth Knowledge of Flanged Check Valves
A flanged check valve is specifically designed with flanged ends to facilitate secure connection to the piping system. These valves are extremely versatile and come in various forms to accommodate different applications, including swing check valves, tilting-disc check valves, and dual-plate check valves. The selection of the appropriate type of flanged check valve is crucial, as it directly impacts the efficiency and reliability of the flow control system.
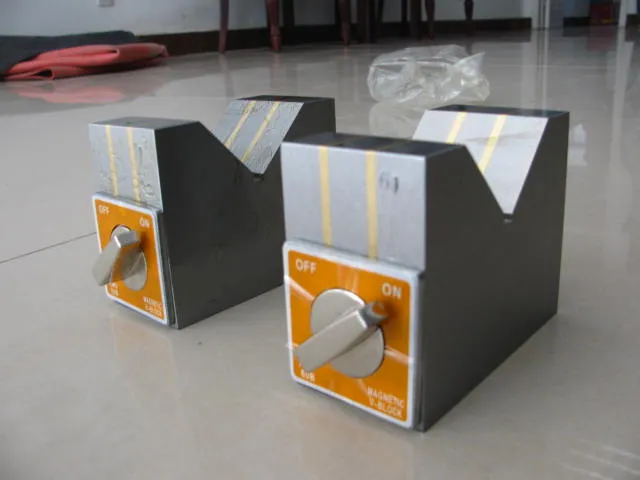
The Expertise in Designing Flanged Check Valves
Understanding the mechanical design of flanged check valves can significantly enhance their application. These valves are engineered to withstand high pressure and temperature conditions, making them suitable for a wide range of industrial applications, such as oil and gas, water treatment, and chemical processing. Their design typically includes a disc that swings onto the seat of the valve, effectively halting backflow while minimizing pressure drop.
Manufacturers often tailor their designs to meet specific industry standards and operational conditions. Therefore, selecting a supplier with a proven track record and commitment to quality can enhance the reliability and lifespan of these valves. Consulting with valve specialists who possess years of industry experience can be instrumental in choosing a valve that meets all operational requirements, from pressure capacity to material compatibility.
Installation and Maintenance Authoritative Guidelines
Proper installation is vital for flanged check valves to function correctly and efficiently. Aligning flanges correctly, using appropriate gaskets, and adhering to torque specifications are fundamental practices that can prevent potential leaks and system failures. Additionally, it is imperative to ensure that the valve is free from debris and that the flow direction is installed correctly.
flanged check valve
A comprehensive maintenance strategy should also be considered to sustain the performance of these valves. Regular inspections, timely replacement of worn components, and adherence to maintenance schedules as recommended by the manufacturer can prevent premature failures and costly downtime. Utilizing expert maintenance service providers can also offer peace of mind, ensuring that the valves remain in prime operational condition.
Ensuring Trustworthiness through Certified Products
Flanged check valves gain trustworthiness through adherence to rigorous industry standards and certifications. These may include ISO, API, and ASME standards, which guarantee that the valves have been tested and certified for industrial use. Traceability is another critical factor, as it confirms the production process and materials used, offering customers assurance of the valve’s quality and performance.
Collaborating with reputable vendors that offer certified products ensures that the flanged check valves meet the requisite safety and efficiency benchmarks. Moreover, having a quality assurance program in place can help identify and mitigate any non-conformities, further enhancing the reliability of the valves.
Real-World Experience Case Studies in Application
The real-world application of flanged check valves offers invaluable insights into their performance and adaptability. In the oil and gas industry, these valves have played a crucial role in ensuring safe and efficient operations, even in the most challenging environments. By preventing backflow, they protect pipelines from contamination, equipment damage, and costly operational disruptions.
In water treatment facilities, flanged check valves contribute to the effective separation of clean and used water, thereby safeguarding the overall system hygiene and functionality. Such applications underscore the importance of valve selection and maintenance, further highlighting their indispensable role across various industries.
In conclusion, the choice and use of flanged check valves require careful consideration of design specifications, installation practices, and maintenance protocols. Leveraging expertise, authoritative guidelines, and a commitment to quality ensures optimal functionality and durability of these indispensable components. As industrial demands continue to evolve, embracing the latest knowledge and technologies related to flanged check valves remains crucial for maintaining an efficient and trustworthy flow control system.