A check valve is an indispensable element in many fluid system designs, operating as a critical component that ensures the smooth and efficient flow of liquids and gases. These devices, often unassuming in appearance, play a pivotal role in maintaining system integrity by allowing flow in a single direction while preventing any backflow. For those delving into fluid mechanics or industries relying on precise fluid control, understanding the intricacies of check valves is fundamental.
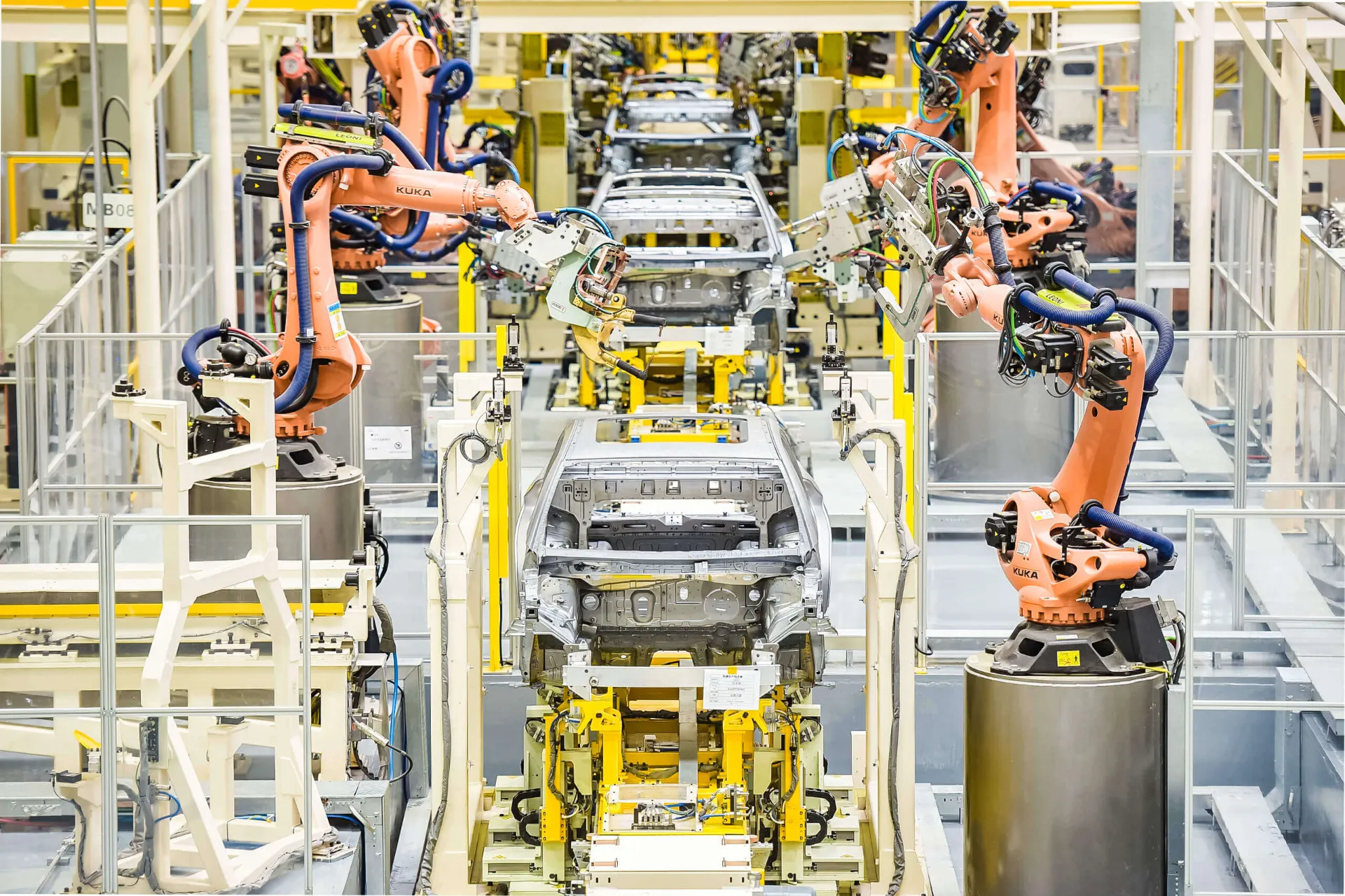
At the heart of the check valve’s operation is its ability to open and close automatically in response to pressure differences in the fluid system. Unlike other valves, check valves do not require an external actuator or a manual mechanism for opening and closing. Their functionality relies purely on the variable pressures exerted by the fluid flow, making them ideal for applications where operational autonomy is crucial.
From an engineering perspective, the design of check valves varies significantly to cater to diverse applications. The most commonly used types include swing check valves, lift check valves, and ball check valves, each tailored to specific operational requirements. Swing check valves, for example, are renowned for their simplicity and efficiency in systems with a high flow rate. They incorporate a disc that swings on a hinge or shaft, allowing fluid to pass through when the system is pressurized and closing to prevent backflow. This design is particularly beneficial in water treatment plants and large-scale pump installations.
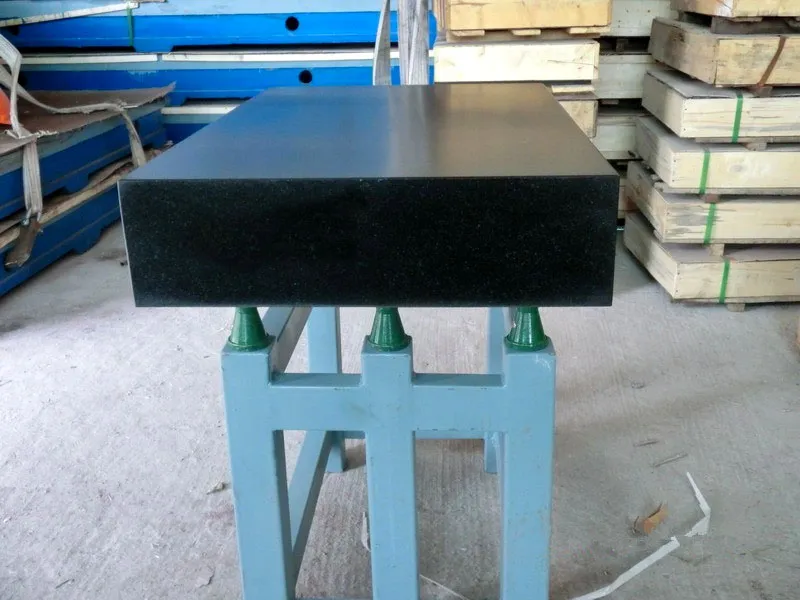
Lift check valves, conversely, operate differently. They incorporate a disc seated on a piston or guide, which lifts when fluid pressure increases, allowing flow. This type is adept at handling turbulent and high-pressure environments, often employed in steam and gas applications due to its robustness and reliability under stress.
Ball check valves, simple in construction, use a ball seated within a conical chamber. Fluid pressure pushes the ball away, allowing flow, but any reverse pressure pushes the ball back into place to seal the valve. This design is prevalent in household plumbing and low-pressure applications, providing a straightforward solution to prevent backflow without sacrificing efficiency.
When selecting a check valve, several factors demand consideration to ensure optimal performance. Material compatibility, for example, is crucial; valves must withstand the chemical composition of the fluid to avoid degradation. Corrosive fluids necessitate check valves made from corrosion-resistant materials like stainless steel or specialized plastics. Temperature and pressure ratings are equally important, as choosing a valve outside the system’s operational parameters can result in failure or inefficiency.
a check valve
Another essential aspect is the sizing of the valve. A valve that is too small might restrict flow and increase system pressure, whereas one that is too large could result in inefficient sealing and potential backflow. Proper sizing ensures the valve complements the fluid dynamics of the system, promoting continuous and unhindered flow.
Furthermore, the installation orientation and location of a check valve can significantly impact its performance. Incorrect installation, such as placing a valve where air pockets might form or in the wrong flow direction, can lead to chattering, wear, and eventual failure. Expert advice should be sought, and manufacturer guidelines meticulously adhered to during installation to mitigate these risks.
Maintenance also plays a crucial role in the longevity and reliability of check valves. Regular inspections for wear and damage, along with timely replacements, ensure the valves continue to function efficiently. In systems where valves are subjected to harsh conditions, more frequent maintenance checks may be necessary to identify issues before they lead to system-wide problems.
From a standpoint of authoritativeness and expertise, understanding the economic benefits of check valves extends beyond operational efficiency. Properly maintained and chosen check valves can lead to significant cost savings by reducing downtime, maintenance costs, and energy consumption due to pump efficiency gains. In energy-intensive industries such as oil and gas, the cost-effectiveness of implementing the right check valves cannot be underestimated.
In conclusion, while check valves may appear as minor components within vast and complex fluid systems, their impact on overall system performance is profound. Their ability to prevent reverse flow not only protects key equipment but also ensures operational efficiency and safety. As industries continue to evolve and demand more sophisticated fluid control technologies, the critical importance of understanding and implementing the right check valve solutions cannot be overstated.