The significance of a 2.5 check valve in fluid systems is often underestimated, yet its impact on efficiency, safety, and operational reliability is profound. Engineers and system designers frequently incorporate check valves as a crucial component to prevent backflow, which can damage equipment and compromise system integrity. Here’s a detailed exploration of the capabilities and applications of the 2.5 check valve, emphasizing expert insights and real-world experiences.
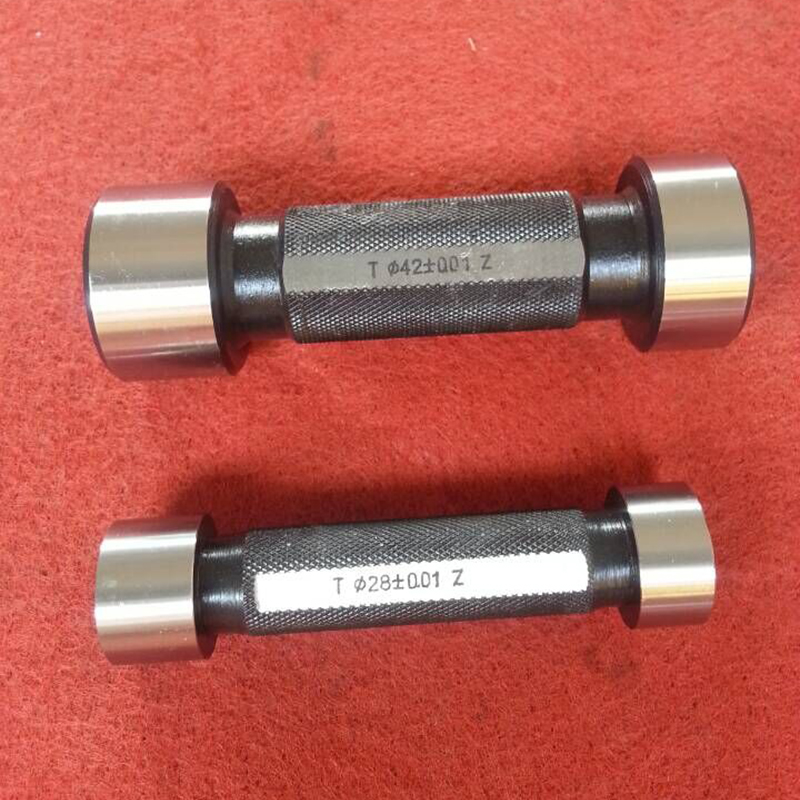
A 2.5 inch check valve is quintessential in various industrial applications, where it serves as a one-way gate for fluid flow, effectively preventing reverse flow which could otherwise cause system failures. Whether integrated into pipelines carrying liquids, gases, or steam, this check valve size is specifically chosen to handle medium flow rates while ensuring minimal pressure drop.
The technical genius of the 2.5 check valve lies in its design simplicity coupled with robust functionality. It typically operates without the need for external controls or power sources, relying on the pressure differential across the valve to open and close the flow path automatically. This passive operation not only contributes to energy efficiency but also enhances the reliability of systems by reducing maintenance demands.
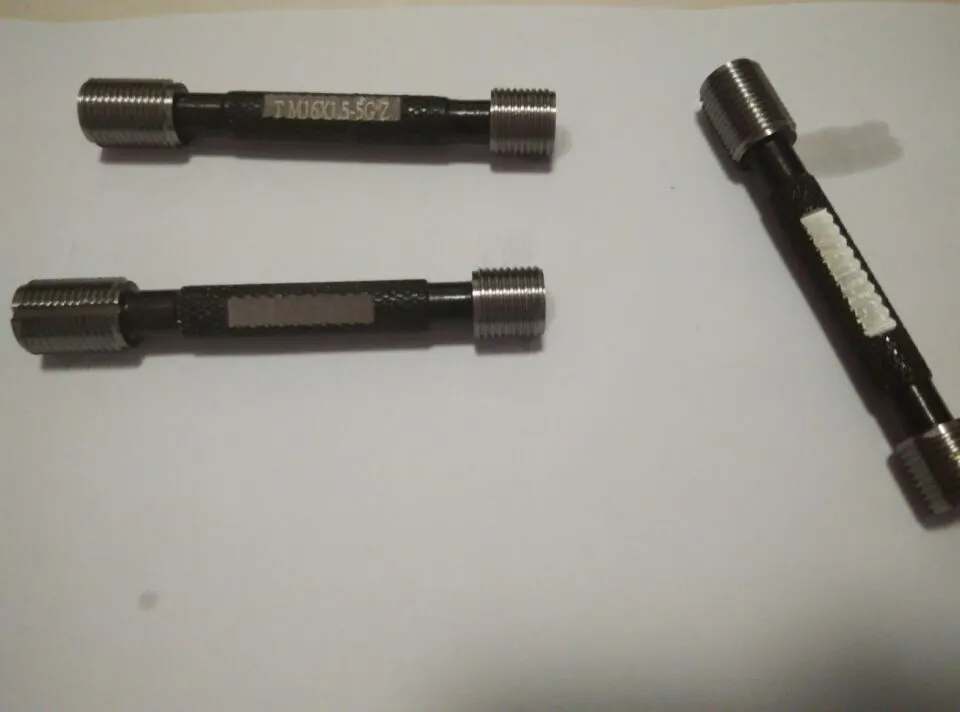
Professionals in industries such as water treatment, oil and gas, chemical processing, and HVAC have consistently vouched for the efficacy of 2.
5 check valves. These valves are often manufactured from high-strength materials like stainless steel, cast iron, or specialized polymers, making them versatile enough to withstand corrosive environments and high-pressure conditions. An operator's experience in a water treatment plant highlighted that a stainless steel 2.5 check valve maintained operational integrity even after years of exposure to highly chlorinated water, testament to its durability and construction excellence.
From a design standpoint, several types of 2.5 check valves are available, each offering unique advantages. Swing check valves, for instance, are popular for their straightforward mechanism, ideal for applications with low flow resistance requirements. Meanwhile, lift check valves are preferred in high-pressure settings due to their efficient sealing capabilities. Selecting the right type involves a nuanced understanding of system specifications and operational demands, underscoring the expertise required in valve selection.
2.5 check valve
Authoritative roles in engineering often emphasize the critical aspect of sizing valves appropriately. A mismatch in sizing can lead to issues like water hammer, reverse flow leakage, or excessive pressure loss. A case study from an oil refinery demonstrated the importance of precise valve sizing; an incorrectly sized check valve led to system downtime and significant repair costs. This scenario emphasizes the role of engineering expertise in ensuring seamless integration and operation of check valves.
In terms of maintenance and reliability, the 2.5 check valve is relatively low-maintenance compared to its larger counterparts. Regular inspection and routine cleaning suffice to keep it functional over extended periods. Knowledge sharing among plant engineers corroborates that scheduled maintenance every six months significantly augments the lifespan of these valves, enhancing their trustworthiness.
Incorporating the latest technological advances, manufacturers are now equipping 2.5 check valves with IoT capabilities, allowing for real-time monitoring of valve performance and predictive maintenance scheduling. This innovation not only boosts operational efficiency but also aligns with the contemporary push towards automation and smart systems in industrial operations.
In conclusion, the 2.5 check valve exemplifies a perfect blend of engineering prowess, efficiency, and reliability. Its pivotal role in preventing backflow and safeguarding system operations cannot be overstated. Choosing the appropriate valve type, material, and ensuring precise sizing are critical considerations that demand industry expertise and authoritative decision-making. With ongoing technological advancements, the future of 2.5 check valves promises further enhancements in operational efficiency and system reliability, securing their indispensable status in industrial applications. As industries evolve, so too will the innovations and capabilities of the 2.5 check valve, perpetuating its importance in the facilitation of safe and effective fluid management across the globe.