Check valves are essential components in various industrial systems, ensuring the unidirectional flow of fluids and preventing backflow. Understanding the three main types of check valves—swing check valves, lift check valves, and ball check valves—can greatly enhance system efficiency and reliability.
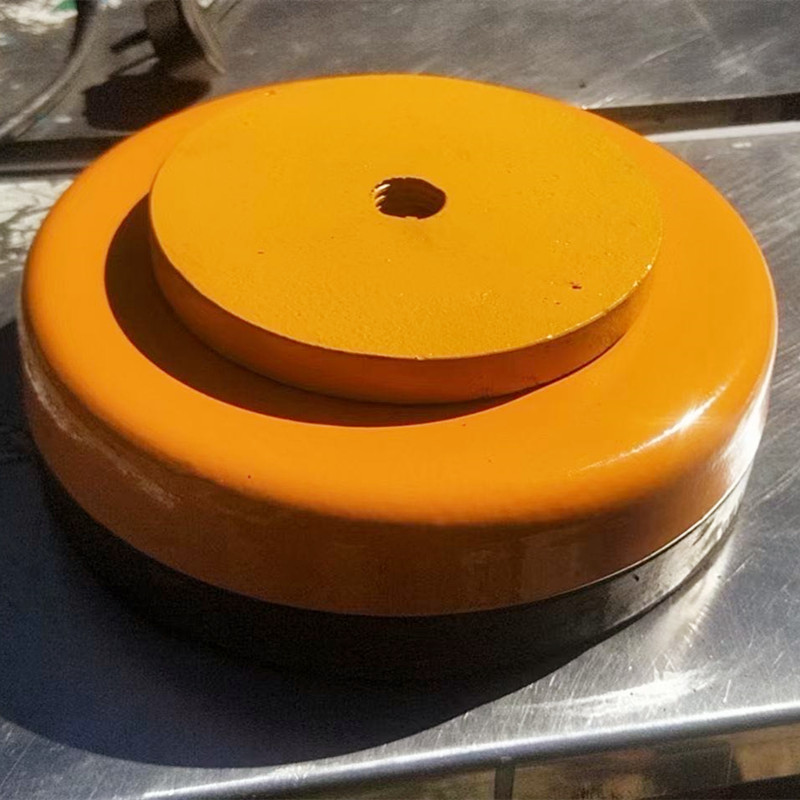
Swing check valves are perhaps the most commonly used type. They operate by means of a disc that swings on a hinge or shaft, opening to allow forward flow and closing when flow reverses. These valves are particularly valued in systems where low-pressure drops are acceptable, such as in water and wastewater management. Their simplistic design and the ability to handle large volumes of liquid make them a go-to choice for many engineers. However, it's crucial to ensure that these valves are installed correctly. If not aligned properly, they can suffer from issues such as water hammer—a phenomenon that can cause significant system disturbances or damage. Speaking from hands-on experience, regular maintenance checks are paramount. A simple schedule of inspections can prevent malfunctions, ensuring the disc moves freely without restrictions.
Lift check valves function differently. Their internal disc moves up and down with the flow of fluid. The benefit here is their ability to close more quickly than swing check valves, thanks to their rapid response to changes in flow direction. They’re particularly suitable for high-pressure systems. These valves offer an advantage in maintaining a tight seal, but they do require a higher pressure drop to operate efficiently. Expertise in system calibration is recommended when dealing with lift check valves to ensure optimal performance without causing unnecessary strain on system components. Experienced professionals often emphasize the importance of choosing the right material and sizing for these valves to withstand the specific pressures in their operating environments.
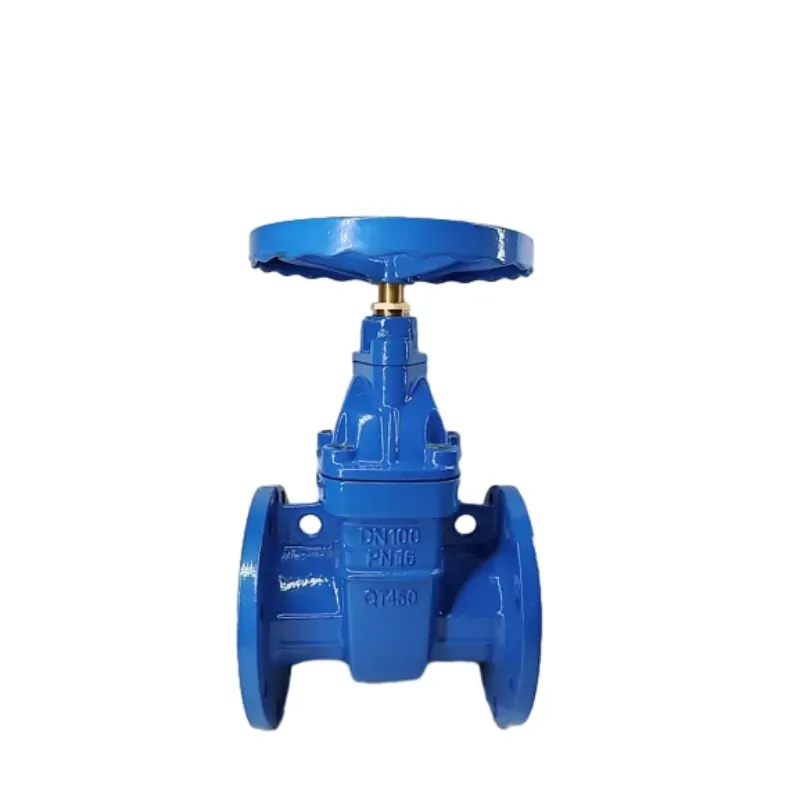
3 types of check valves
Ball check valves, recognized for their compact size and robust design, operate using a ball that moves in and out of a seat to block or allow flow. This type is particularly popular in applications where space is limited, or systems deal with viscous fluids that might cause other types of check valves to stick or become ineffective. The versatility in handling different types of fluids and their resistance to clogging underlines their authority within industries like petrochemical and pharmaceutical manufacturing. From a reliability standpoint, ball check valves are lauded for their low maintenance requirements. Trust in these components is often underscored by their long service life and consistent performance, even under harsh conditions. However, it’s crucial to ensure that they are installed in the correct orientation because incorrect installation can lead to ineffective flow regulation.
Beyond technical specifications, ensuring trustworthiness in any industrial application involves selecting products from reputable manufacturers. Companies that adhere to international quality standards and offer thorough testing and certifications usually provide the most reliable products. Expert reviews and case studies regarding the use of these valves can further solidify their credibility, offering insights into their performance in real-world applications.
Selecting the appropriate check valve type requires not only an understanding of system requirements and fluid characteristics but also a commitment to ongoing system monitoring and maintenance. Utilizing these valves effectively can optimize flow control, reduce downtime, and enhance the longevity of the entire system. Engaging with valiant design engineers and maintenance professionals is always recommended to navigate specific industry challenges and to sustain high levels of operational excellence. With such comprehensive insights, businesses can ensure the efficiency and reliability of their check valve applications, ultimately fine-tuning their operations to meet industry demands while safeguarding against system inefficiencies.