Fabrication table clamps are essential tools in any metalworking or woodworking shop, offering both precision and stability. These clamps ensure that workpieces remain firmly in place during fabrication processes, enabling artisans and professionals alike to create with accuracy and efficiency. Understanding the nuances and advantages of various types of fabrication table clamps can significantly enhance productivity and craftsmanship.
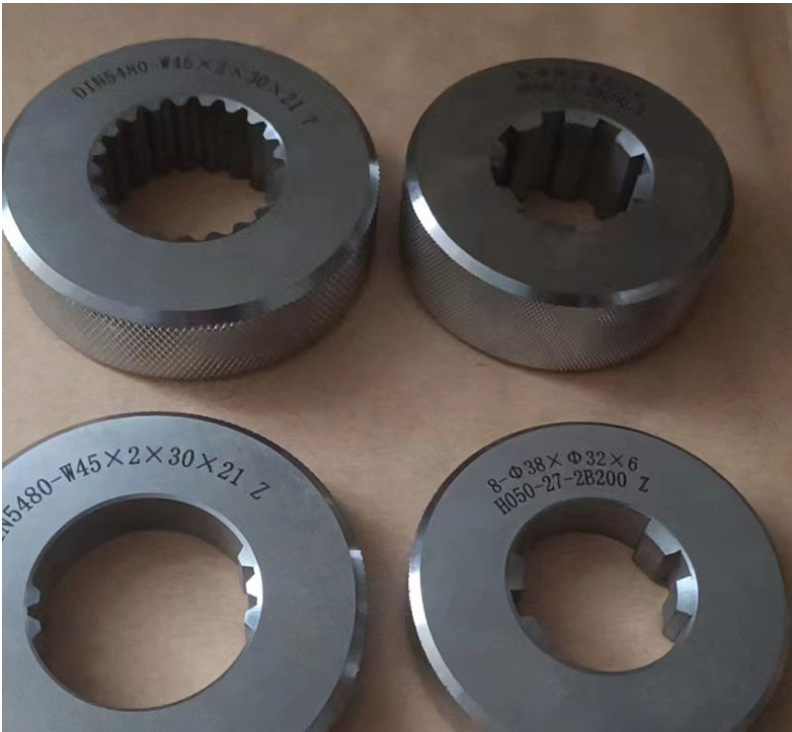
Quality fabrication table clamps provide a stable foundation for working on materials, effectively reducing the chance of errors. In any fabrication process, the slightest movement can lead to discrepancies in measurement or alignment, resulting in a flawed product. Clamps negate this risk by securing workpieces with a firm yet gentle grip, preventing both slippage and damage. When selecting clamps, attention to material strength and clamping power is crucial. Fabrication experts often prefer clamps made from hardened steel due to their durability and reliable performance under stress.
There are several types of clamps, each designed for specific applications. Fixed clamps are straightforward and ideal for securing materials in a static position. Their strong grip makes them perfect for repetitive tasks that require maintaining exact positions. On the other hand, adjustable clamps offer versatility, being able to accommodate various material sizes quickly and efficiently. This adaptability is particularly beneficial in environments where tasks frequently change. For metal fabrication, where precision is paramount, magnetic clamps provide a solution that does not damage surfaces and allows for easy repositioning when necessary.
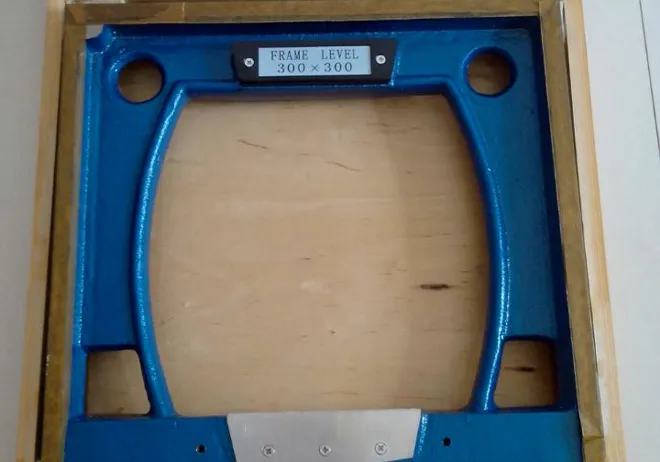
In specialized use cases, such as welding, the heat-resistance of a clamp becomes a primary consideration. Clamps that can withstand high temperatures without deforming ensure safety and maintain their integrity during intensive processes. Many experienced welders invest in clamps with copper-coated tips, which help to conduct heat away from the point of welding, minimizing the occurrence of thermal distortion.
Investing in high-quality fabrication table clamps can improve not only the quality of craftsmanship but also the safety of the workplace. Clamps that fail under pressure can lead to workplace injuries or material wastage. According to industry standards, it is advisable to seek out clamps with a tensile strength rating that exceeds everyday operational demands by at least 25%. This margin ensures that the clamp performs optimally even under unforeseen stress.
fabrication table clamps
Moreover, the design of the clamping system plays a critical role in its functionality. Ergonomically designed clamps reduce the physical strain on technicians, contributing to prolonged and comfortable use. Features such as quick-release mechanisms and non-slip handles enhance user experience by streamlining the workflow and reducing setup times. These attributes are particularly valuable in production settings where efficiency is key.
Authoritative reviews and recommendations from fabrication veterans stress the importance of regular maintenance to extend the lifespan of clamps. Periodic inspections for signs of wear and tear, as well as routine cleaning to remove metal shavings or dust, ensure the clamps remain in top condition. Lubricating the moving parts of clamps can prevent rusting and ensure smooth operation, which is essential for maintaining precise clamping pressure.
Speaking from years of experience, trusted fabricators emphasize the need for establishing a clamping strategy tailored to specific project requirements. For complex assemblies, a combination of clamp types might be necessary to achieve optimal support and precision. Testing different configurations can lead to insights that drive both innovation and efficiency in fabrication processes.
As industry standards evolve, the development of new materials and technologies continues to enhance the capabilities of fabrication table clamps. Manufacturers are increasingly integrating innovative features such as digital readouts for pressure and positioning, giving users unparalleled control over their work environments. Staying informed about these advancements ensures that professionals and hobbyists can make knowledgeable decisions when selecting tools that will shape the future of their craft.
In a competitive landscape, trustworthiness in tool selection directly influences the reputation of the fabricator. Clamps that consistently perform as expected reflect the skill and reliability expected in high-quality workmanship. Thus, when choosing fabrication table clamps, considering their performance history, materials, and expert reviews can lead to safer, more consistent, and superior results in any fabrication task.