Gate valve seals are crucial components in ensuring the effective functioning of a vast array of industrial applications. These seals are designed to control the flow of liquids or gases, and their performance directly impacts the operational efficiency and safety of systems where they are applied. In an industry where precision and reliability are paramount, understanding the nuances of gate valve seals is essential for engineers and maintenance professionals seeking to optimize system performance.
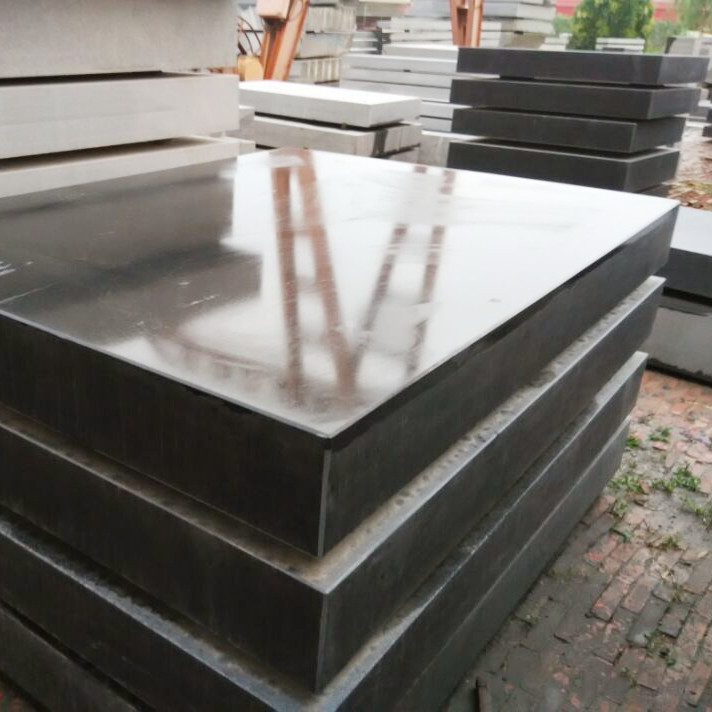
The selection of gate valve seals is a decision that should not be taken lightly. Given the diversity of materials available, such as rubber, PTFE, graphite, and metal, each choice comes with its specific set of properties that suit different operational environments. For instance, rubber seals provide excellent flexibility and are ideal for low-pressure applications but may become brittle in extreme temperatures. On the other hand, graphite seals withstand high temperatures and pressures, making them suitable for applications involving steam or aggressive chemicals. Selecting the right seal material can significantly enhance the longevity and reliability of the valve.
In terms of installation and maintenance, gate valve seals require careful attention to detail to ensure optimal performance. A robust seal installation process begins with ensuring that both the seal and the gate valve itself are clean and free from any debris or damage. Proper alignment of the seal is crucial, as any misalignment could lead to fluid leakage, compromising system integrity. Routine inspection and maintenance of these seals can preemptively identify wear or damage, allowing for timely replacements before failures occur. Maintaining a detailed log of seal performance and replacement history is a practice that can enhance maintenance efficiency and reliability.
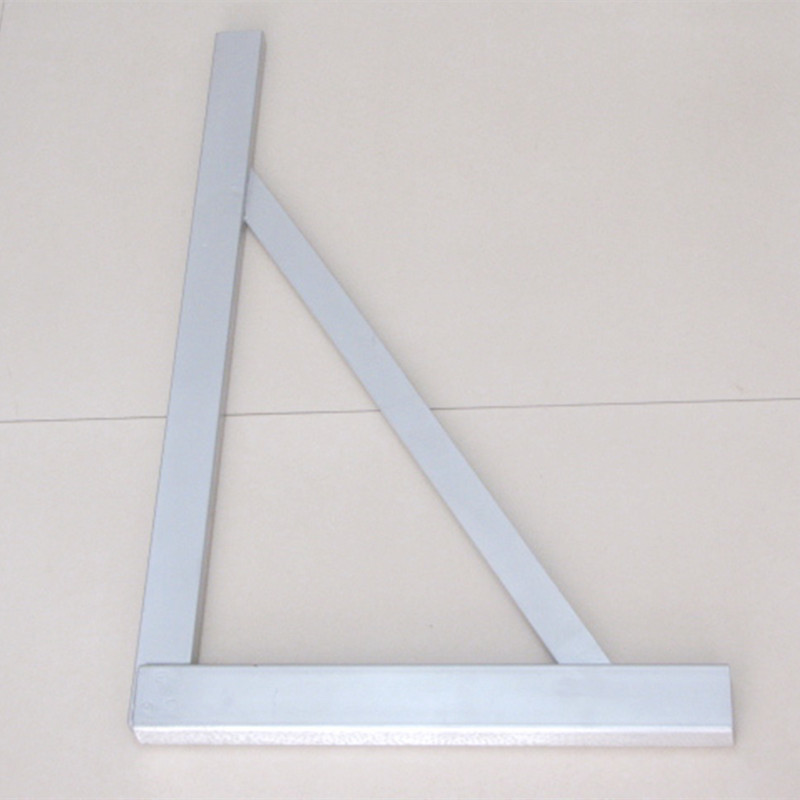
Gate valve seals also play a pivotal role in energy efficiency. In industries where energy consumption is a critical concern, high-quality seals can minimize leaks, ensuring that the systems operate at peak efficiency. This not only reduces unnecessary energy expenditure but also aligns with environmental and regulatory requirements for reducing emissions. By choosing the appropriate gate valve seals and maintaining them diligently, facilities can achieve both operational excellence and sustainability goals.
gate valve seal
Reliability in high-stakes environments, such as oil and gas, power generation, and chemical processing, hinges on the capability of gate valve seals to provide uncompromising performance. These industries often operate under stringent safety regulations, where even a minor leak can escalate into significant safety hazards and environmental incidents. Therefore, investing in superior quality gate valve seals, designed and tested to withstand specific conditions, is a critical aspect of risk management. Ensuring that seals meet relevant industry standards, such as ANSI or API specifications, provides an additional layer of assurance regarding their performance capabilities.
Innovation in seal technology continually pushes the boundaries of performance and durability. Manufacturers are focusing on developing seals with enhanced materials that cater to the evolving demands of modern applications. For example, the incorporation of advanced polymers and composite materials has led to the creation of seals that offer superior resistance to degradation while extending the operating life of gate valves. Professionals and decision-makers must stay informed about these technological advancements to harness their potential for improving system performance and cost-efficiency.
Implementing a predictive maintenance strategy, leveraging the latest in analytical tools and IoT monitoring, can further enhance the reliability of gate valve seals. Sensors and diagnostic tools can monitor the condition of seals in real-time, providing valuable data that can predict potential failures. This proactive approach not only reduces unplanned downtimes but also optimizes maintenance resources and extends the operational lifespan of both the seals and the entire system.
In summary, the significance of gate valve seals extends beyond their immediate functional purpose. They are integral to a holistic strategy for optimizing operational efficiency, maintaining safety standards, and achieving cost-effectiveness in industrial processes. By prioritizing the quality, installation, maintenance, and monitoring of these seals, organizations can unlock significant value in their operations. As industries continue to evolve, the role of gate valve seals will remain paramount, underscoring the need for expertise, trustworthiness, and innovation in their selection and application.