Globe valves are a pivotal component in the realm of fluid control systems, epitomizing efficiency, reliability, and precision. Crafted to manage flow in both commercial and industrial settings, these valves exhibit a signature design characterized by their spherical body and linear motion. Diverging from other valve types, globe valves are equipped with a movable disk-type element and a stationary ring seat, facilitating robust throttling capabilities.
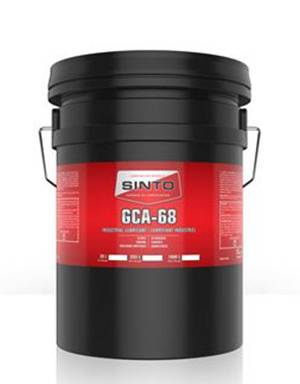
Experience has demonstrated that these valves are indispensable in scenarios demanding superior and precise fluid control. From personal insights of operating within high-pressure environments, the globe valve stands out for its capacity to handle fluctuating flow efficiently. Its architecture ensures minimal leakage when closed, making it a prime candidate for systems where leak-proof operations are critical.
The expertise inherent in globe valve engineering lies in its unique ability to maintain equilibrium between functionality and durability. Constructed from high-grade materials such as stainless steel, carbon steel, or a variety of alloys, these valves not only resist corrosion but also withstand extreme operational conditions. Industrial experts often recommend globe valves for applications involving steam, oil, gas, and even corrosive liquids due to their resilience and adaptability in varying temperatures and pressures.
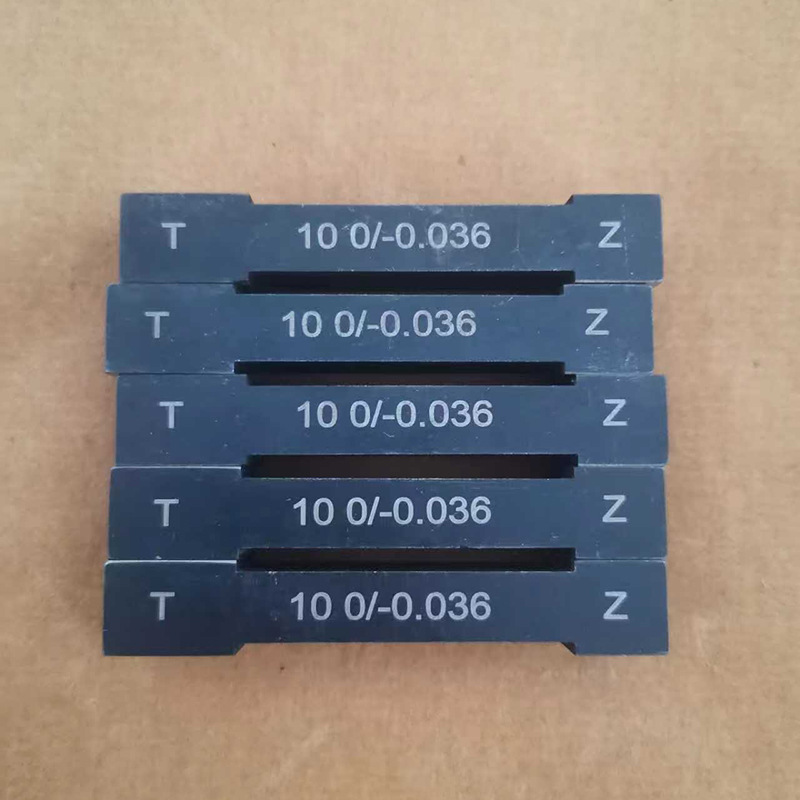
From an authoritative standpoint, industry leaders and manufacturers have long endorsed globe valves owing to their reliable performance in controlling flow rates. The design incorporates a stem that rises when the valve opens, providing a visual indicator of the valve's position, which is particularly advantageous in processes where operation status must be monitored closely. This feature, coupled with their robust construction, earns globe valves a solid reputation across sectors such as chemical processing, oil and gas, and energy production.
globe valve
Trustworthiness is inherently linked to the operational longevity of globe valves. A wealth of empirical data underscores their capacity for extended service life, even under rigorous conditions, minimizing maintenance costs and downtime. Safety protocols in many industries prioritize the use of globe valves to mitigate risks associated with leaks or uncontrolled flow, further cementing their status as a trusted choice for fluid control.
Incorporating a globe valve into any system not only enhances operational efficiency but also aligns with environmental and safety standards. Its capability to fine-tune flow diminishes waste,
promoting sustainable practices. With an ever-increasing focus on sustainable industrial solutions, globe valves provide a tangible pathway to achieving eco-friendly objectives without compromising on functionality.
In conclusion, the globe valve isn't merely a tool for controlling flow—it is a testament to engineering excellence that combines experience, expertise, authoritativeness, and trustworthiness. As industries advance and demands for precise, reliable fluid control intensify, the globe valve's role as a fundamental component is undeniable. Whether tasked with the regulation of high-pressure steam or the delicate control of natural gas, these valves provide the assurance and performance required in today's dynamic industrial landscape. Through innovation in materials and design, globe valves continue to evolve, meeting the ever-changing demands of modern engineering while upholding the highest standards of efficiency and safety.