Control valves are indispensable components in various industrial processes, serving as the primary means of regulating the flow and pressure of fluids. Their importance in ensuring efficient and safe operations cannot be overstated. This article delves into the different types of control valves and their specific applications, providing insights garnered from decades of expertise and real-world experience.
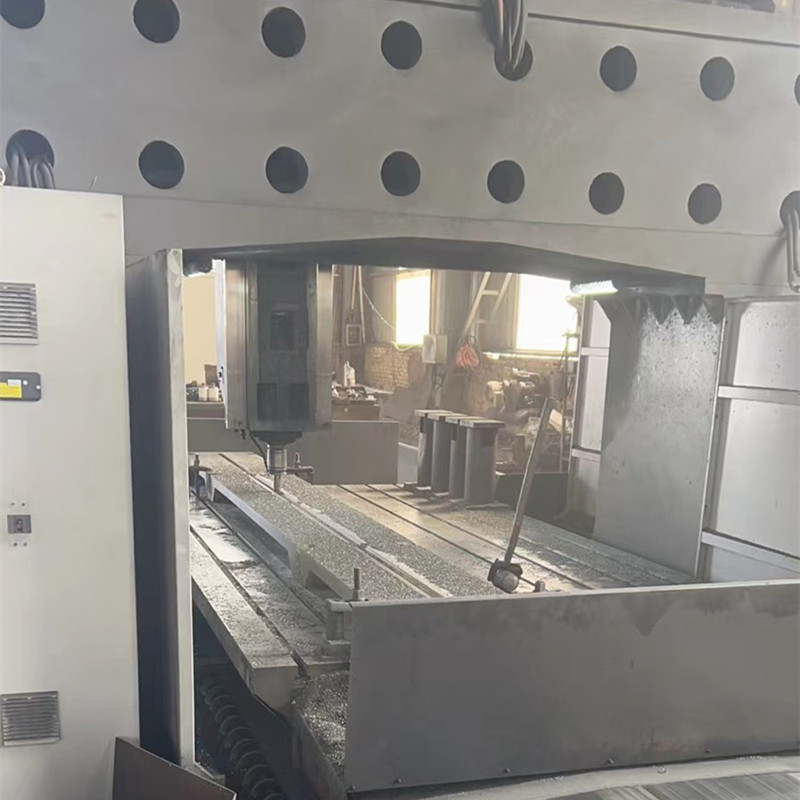
Control valves come in several types, each designed to meet specific needs in industrial applications. The most common types include globe valves, ball valves, butterfly valves, and diaphragm valves.
Globe valves are perhaps the most ubiquitous type of control valve. Known for their excellent throttling capabilities, they are used when precise flow control is required. They operate by moving a disc into or out of the path of a flowing fluid. Typically constructed from durable materials like stainless steel or brass, globe valves find applications in industries such as petrochemicals, where precise control over fluid flow is paramount. Their design allows for excellent flow regulation, making them the valve of choice in high-pressure environments.
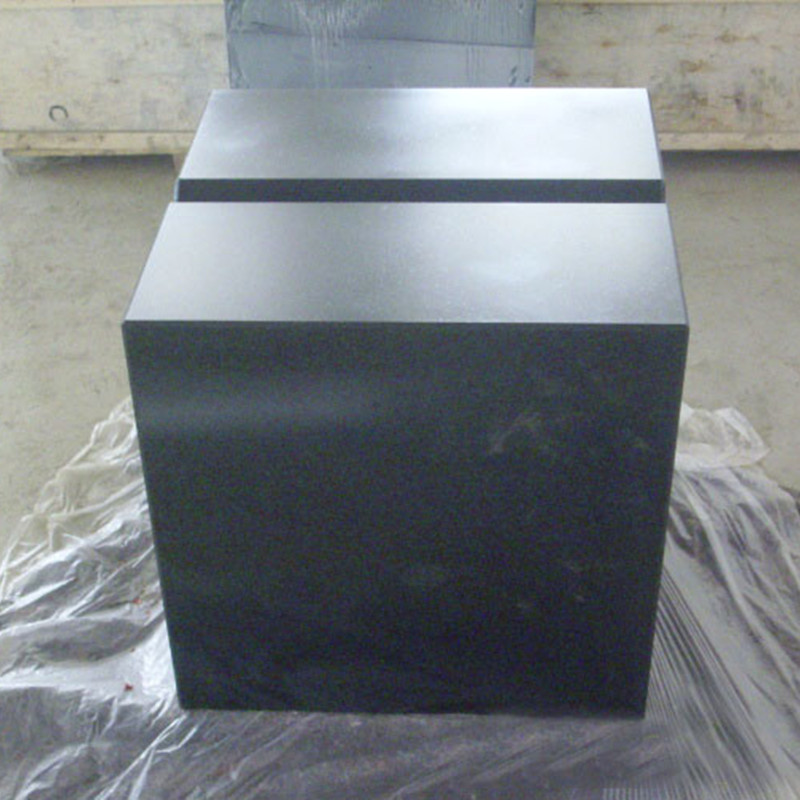
Ball valves, in contrast, provide straightforward on-off control without much throttling. This simplicity makes them ideal for applications requiring rapid shut-off, such as emergency handling systems. They consist of a spherical disc, the part which actually controls the flow through it. Ball valves are widely used in applications across the oil and gas sector, where quick operation and reliability are crucial. Their robust nature enables them to withstand high pressures and temperatures, making them well-suited to harsh industrial environments.
Butterfly valves, with their compact design and quick operation, are ideally suited for applications where space is limited. These valves use a rotating disc to control the flow of fluids and are often employed in large-scale water distribution, manufacturing, and food processing industries. They offer a relatively good pressure control capability and can handle bi-directional pressure. In applications where installation space is a concern, butterfly valves are often preferred due to their light weight and low pressure drop characteristics.
types of control valve and applications
Diaphragm valves are favored in applications involving high-purity fluids and corrosive substances. Their design, which uses a flexible diaphragm to open or close the valve, makes them ideal for controlling flow in pharmaceutical, biotechnological, and food industries. The absence of a dynamic seal between the body and the bonnet ensures there is no contamination of the fluids, which is crucial in maintaining the integrity of the product in high-purity processes.
For more demanding applications, specialized types of control valves such as pinch valves and pressure reducing valves are used. Pinch valves are perfect for handling slurries and granular products. They offer minimal flow obstruction because they control the flow by pinching a flexible inner tube through which media passes. This design is particularly beneficial in wastewater treatment plants and mining operations.
Pressure reducing valves maintain a constant downstream pressure despite varying upstream pressure and are employed in steam, gas, and water distribution networks. This ability to regulate pressure downstream ensures that systems are protected from the potential damage of excess pressure, thus prolonging the life of connected equipment and machinery.
Each type of control valve offers unique advantages tailored to specific applications, underlining the importance of selecting the appropriate valve type to meet operational demands critically. Industry professionals must consider factors such as the chemical properties of the media, pressure, temperature, and the desired flow characteristics when selecting a valve. The right choice not only optimizes the process efficiency but also reduces maintenance costs and enhances safety.
In conclusion,
the selection of a control valve is a critical decision in industrial operations. Understanding the distinct characteristics and applications of each valve type boosts process efficiency and safety. Whether dealing with high-pressure steam in a power plant or ensuring the sterile flow of pharmaceuticals, selecting the right control valve is paramount for operational success. Through the lens of experience, expertise, authoritativeness, and trustworthiness, the nuances of control valves reveal that their correct application is as much an art as it is a science.