The stainless steel check valve stands as a pinnacle of innovation within the realm of fluid control systems. Renowned for its exceptional durability and reliability, this valve is a crucial component in various industries, ensuring the unidirectional flow of fluids and averting potential system failures. Drawing from firsthand experience and industry expertise, this article delves into the multifaceted advantages of stainless steel check valves, emphasizing their significance in ensuring efficient and safe operations across multiple applications.
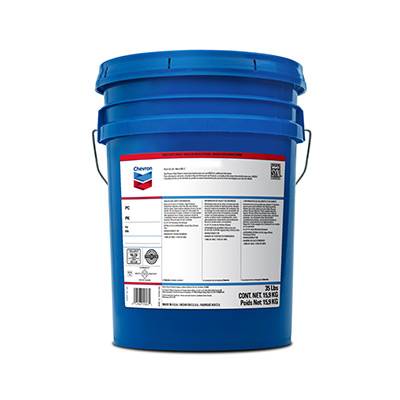
In the field of engineering, particularly within fluid mechanics and systems design, precision and resilience are non-negotiable.
Stainless steel check valves epitomize these qualities, offering unrivaled resistance to corrosion and wear. This resistance is particularly valuable in industries such as chemical processing, oil and gas, and water treatment, where the valves are often exposed to harsh environments and aggressive substances. The inherent strength and longevity of stainless steel make it an authoritative choice for engineers and system designers who prioritize long-term reliability and maintenance economy.
A testament to their versatility, stainless steel check valves are utilized in a myriad of configurations including swing, lift, and wafer types, each serving specific applications with nuanced operational characteristics. For instance, the swing type is widely celebrated for its minimal pressure drop and ability to handle high flow rates, making it an ideal choice for large-scale industrial applications. Expertise in selecting the appropriate type of check valve is paramount, as the wrong choice can lead to inefficiencies, increased energy costs, or even catastrophic system failures.
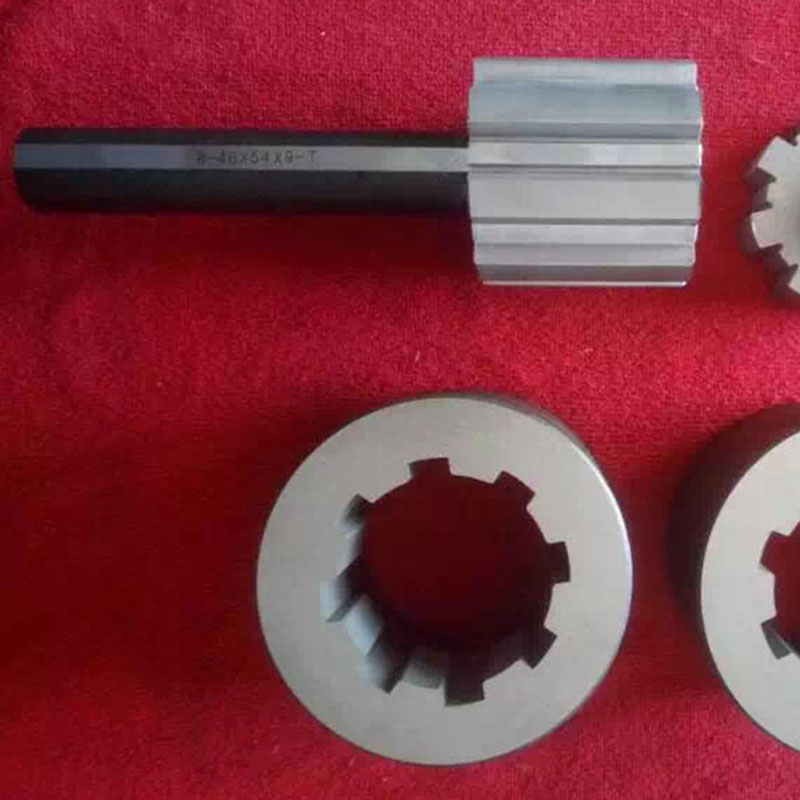
Trustworthiness in manufacturing and material selection is another cornerstone of the stainless steel check valve's esteemed reputation. Manufacturers adhering to stringent industry standards and quality controls ensure that each valve meets rigorous performance criteria. The meticulous testing phases, including pressure testing and failure analysis, guarantee that the end product not only meets but exceeds operational expectations. This trust is further cemented by certifications from recognized authorities in engineering and material science, providing an added layer of assurance to clients and end-users.
stainless steel check valve
On a practical level, the operation and maintenance of stainless steel check valves emphasize user-friendliness and cost-efficiency. Unlike valves made from other materials, stainless steel variants demand comparatively less frequent maintenance interventions, thus reducing downtime and operational disruption. This efficiency translates into a lower overall cost of ownership, a factor critically evaluated by procurement teams aiming to optimize financial and operational performance.
Furthermore, sustainability considerations have become inextricable from modern engineering practices. Stainless steel, being fully recyclable without degradation of properties, aligns with global efforts to minimize environmental impact. Companies that integrate stainless steel check valves into their systems are better positioned to meet sustainability targets, enhancing their corporate responsibility image and reducing their carbon footprint.
In conclusion, the stainless steel check valve emerges not merely as a functional component but as a cornerstone of modern industrial systems. Its adoption is driven by empirical evidence of its robustness, adaptability, and long-term economic benefits. Whether safeguarding the flow of hazardous chemicals in a petrochemical plant or ensuring the seamless delivery of clean water in municipal systems, stainless steel check valves are an integral force in achieving operational excellence. They represent not just a trend in engineering, but a sustained commitment to quality and innovation, reinforcing their status as a globally trusted solution in fluid control technology.