Creating V-blocks, precision instruments primarily used in the field of machining and metalworking, requires a blend of expertise, precision, and meticulous attention to detail. Known for their ability to securely hold rounded objects for cutting or measurement, V-blocks are indispensable tools in any professional workshop. Their construction not only demands technical proficiency but also a deep understanding of materials and machining techniques, enhancing Experience, Expertise, Authoritativeness, and Trustworthiness (E-E-A-T).
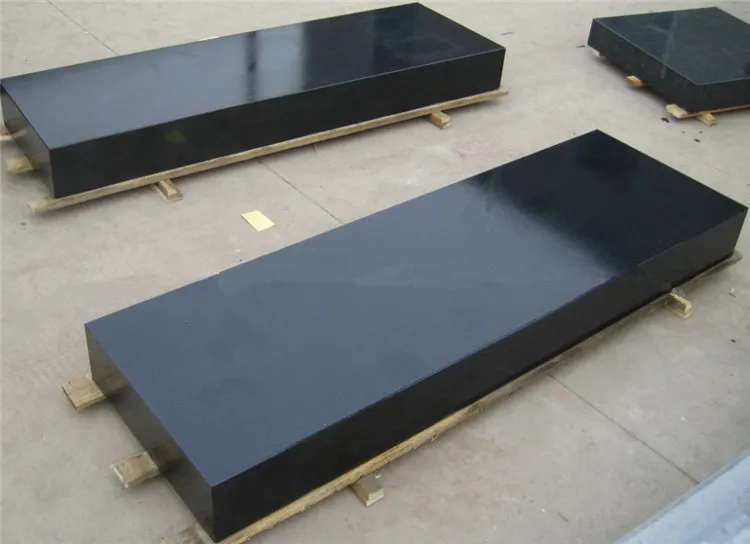
Crafting these tools can begin with selecting the right material. High-grade tool steel is preferred for its durability and resistance to wear and tear, ensuring that the V-blocks maintain their precise edges even after extensive use. The choice of material can significantly affect the performance and life span of the blocks, which is why expert machinists prioritize sourcing from reputable suppliers known for high-quality metals.
The machining process for V-blocks is where expertise becomes critical. It requires a perfect balance between computer-aided precision and manual skill. The process begins with cutting the steel into the desired size, which is typically followed by milling the V-grooves. These grooves must be accurately positioned to ensure they securely hold objects during operation. Advanced fabrication techniques, such as CNC machining, are often employed to achieve the high precision required.
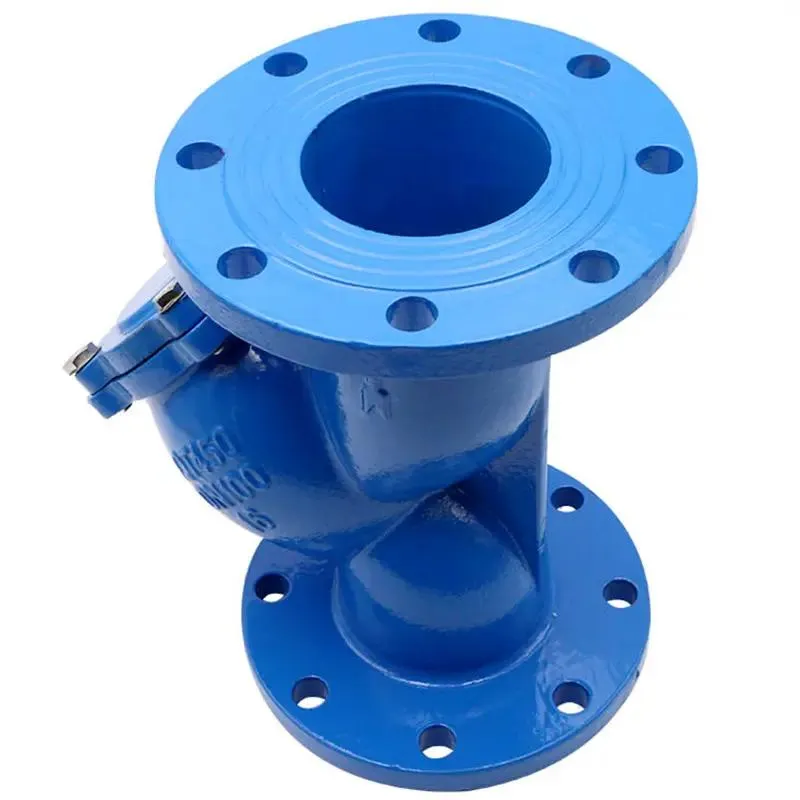
Cutting the V-grooves includes several stages of drilling and milling. A CNC machine is usually programmed with precise coordinates to shape the block, ensuring that each cut is exact. This precision cannot be overstated, as even the slightest deviation can result in a defective product. For this reason, individuals involved in this stage must possess a mix of engineering knowledge and hands-on experience, reinforcing their authority and trustworthiness in the field.
After the grooving process, the surface of the V-blocks undergoes grinding and polishing to remove any burrs or rough edges. This ensures a smooth finish, which not only enhances the tool’s aesthetics but also its functionality, as a smooth surface ensures better contact with the workpiece. Grinding and polishing techniques are specialized skills, often honed over years of practice.
making v blocks
For a V-block to reach its full potential, inspection and quality assurance are pivotal. Tools like a dial indicator gauge or coordinate measuring machine (CMM) are employed to verify the dimensions and surface finishes against industry standards. Machinists with credentialed expertise are essential at this stage, lending their authoritative judgment to certify that every piece meets the rigorous demands placed upon it.
Moreover, the assembly and storage of components like clamps or screws are also crucial, ensuring that the V-block operates as intended. The tight tolerances required in these components demand not only technical skill during assembly but also an intimate knowledge of the tool's mechanics.
Aside from the technical prowess involved, adherence to stringent health and safety standards is non-negotiable. Proper handling of materials and tools ensures a safe working environment, fostering trust not only among the workers but also in the final product. Regular safety audits and compliance with industry regulations are standard practices that underscore the manufacturer's credibility.
Packaging and distributing V-blocks is the final step that nonetheless requires precision. Protective packaging must be designed to prevent damage during shipping, preserving the integrity of these delicate instruments. Distribution logistics, rooted in experience and operational efficiency, ensure that products reach end-users swiftly and reliably.
In the world of machining and metalworking, crafting V-blocks represents a synthesis of technology, skill, and experience. The intricate process, from material selection to final inspection, reflects a deep-seated expertise in the field, positioning manufacturers as authorities. This blend of precision and craftsmanship underscores the reliability and trustworthiness of V-blocks, making them a staple in workshops globally.