Selecting the right components for industrial fluid handling systems is crucial, and one indispensable component is the 4-inch knife gate valve. This essential piece of equipment serves a critical function in pipelines that require an efficient shut-off and control mechanism. Designed with precision, the 4-inch knife gate valve has redefined the standards of reliability and operational excellence in various industries, including wastewater, mining, and pulp processing.
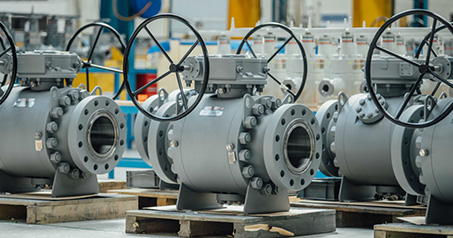
Renowned for its ability to cut through fluids carrying solids and viscous matter, the 4-inch knife gate valve features a sharp-edged blade that effectively performs this feat with minimal pressure drop. Its mechanism involves a gate that fits into a seat, moving vertically to start or stop the flow. This operational simplicity translates to effectiveness in handling heavy slurries, granules, and even fibrous materials without causing significant disruptions or blockages. The design's brilliance lies in its ability to self-clean during operation; as the gate moves across the seat, potential build-up is removed, maintaining a clear pathway.
Industrial applications demand resilience, and the 4-inch knife gate valve meets this need through rugged construction materials such as stainless steel, cast iron, or coated carbon steel. Each choice of material offers unique advantages. Stainless steel provides excellent corrosion resistance—an ideal choice for handling corrosive media. In contrast, cast iron offers strength and cost-effectiveness for less demanding environments. The option to coat carbon steel with specialized materials extends the valve’s durability, ensuring a long service life even in the harshest conditions.
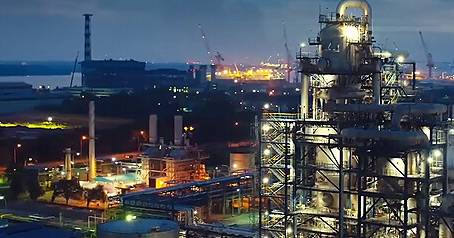
An often-overlooked advantage of the 4-inch knife gate valve is its compact design, which makes it suitable for installations where space is constrained. This is particularly beneficial in retrofitting existing systems where large changes are impractical. The valve's relatively low weight compared to other valve types makes it easier and less costly to install, especially in overhead and remote locations.
4 inch knife gate valve
Safety and environmental compliance are paramount concerns in industrial settings, and the 4-inch knife gate valve plays its part. Many modern designs include features to reduce fugitive emissions and adhere to rigorous standards such as ISO and ASME, ensuring safe operation and compliance with regulatory mandates. By minimizing the risks associated with leaks and emissions, these valves protect personnel and the environment, underscoring their role in responsible industrial operations.
Maintenance is another area where the 4-inch knife gate valve excels. Thanks to its straightforward design, routine inspection and repairs can be carried out with minimal downtime. Parts such as the seals and seats are easily accessible and replaceable, contributing to lower long-term maintenance costs. Many manufacturers offer a variety of packing materials and seal designs to cater to different pressure and temperature ranges, allowing the valve to be tailored to specific needs and enhancing its versatility.
In the context of flow control systems, the expertise of sourcing a reliable 4-inch knife gate valve cannot be overstated. However, optimal performance is achieved only when the valve is part of a comprehensive strategy that considers the entire system—each component must work harmoniously to maximize efficiency and productivity. That’s why expert consultation during the selection and installation processes is crucial. Specialists bring to the table a wealth of knowledge regarding the intricacies of fluid dynamics, material compatibility, and system design, ensuring that the 4-inch knife gate valve is integrated seamlessly into the application at hand.
In conclusion, the 4-inch knife gate valve is an indispensable component in modern industrial applications, distinguished by its cutting precision, robust construction, and operational reliability. Its thoughtful design not only meets rigorous industrial standards but also supports efficient and safe operations across a wide range of challenging environments. Its role in maintaining optimal system performance while minimizing environmental impact underscores its importance as a trusted component in industrial fluid handling systems.