Precision tools and gauges play a crucial role in the manufacturing sector, where accuracy and reliability are paramount. These tools ensure that components meet stringent standards, enabling the production of high-quality products across various industries. As an experienced quality control engineer with over two decades in the field, I’ve witnessed firsthand the transformative impact that high-caliber precision instruments can have on the overall manufacturing process.
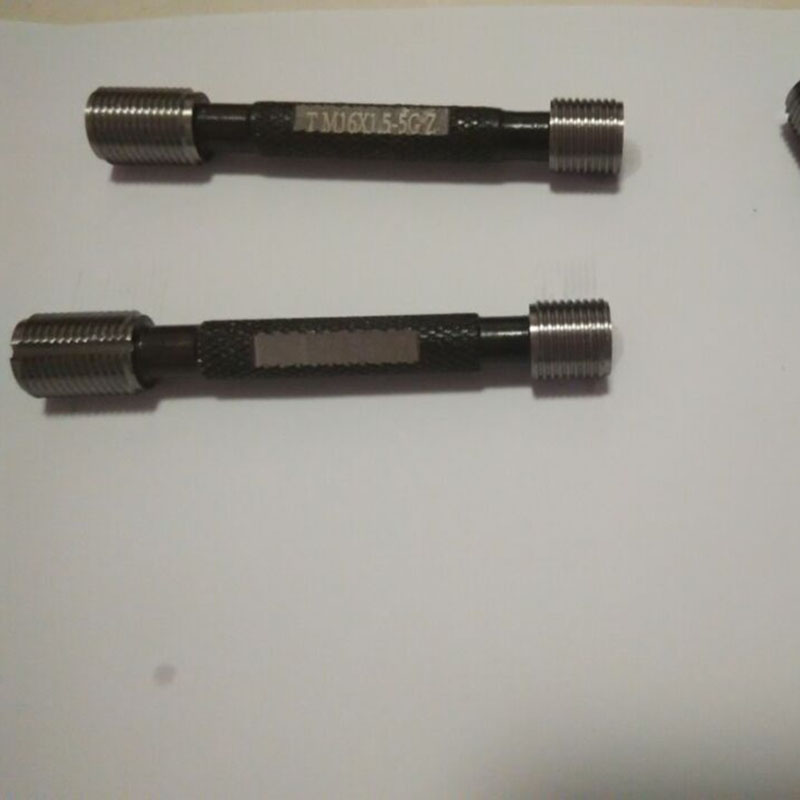
In the realm of precision engineering, the importance of using top-tier tools cannot be overstated. These tools, ranging from micrometers and calipers to dial indicators and surface plates, are the backbone of ensuring dimensional accuracy. In industries such as aerospace, automotive, and medical devices, where even the slightest deviation can lead to catastrophic results, precision tools and gauges are indispensable.
Expertise in the correct usage and calibration of these tools further amplifies their efficacy. Manufacturers are increasingly recognizing the value of comprehensive training programs aimed at enhancing operators’ skills in this area. By investing in training, companies not only improve measurement accuracy but also significantly reduce material wastage, thereby boosting overall operational efficiency.
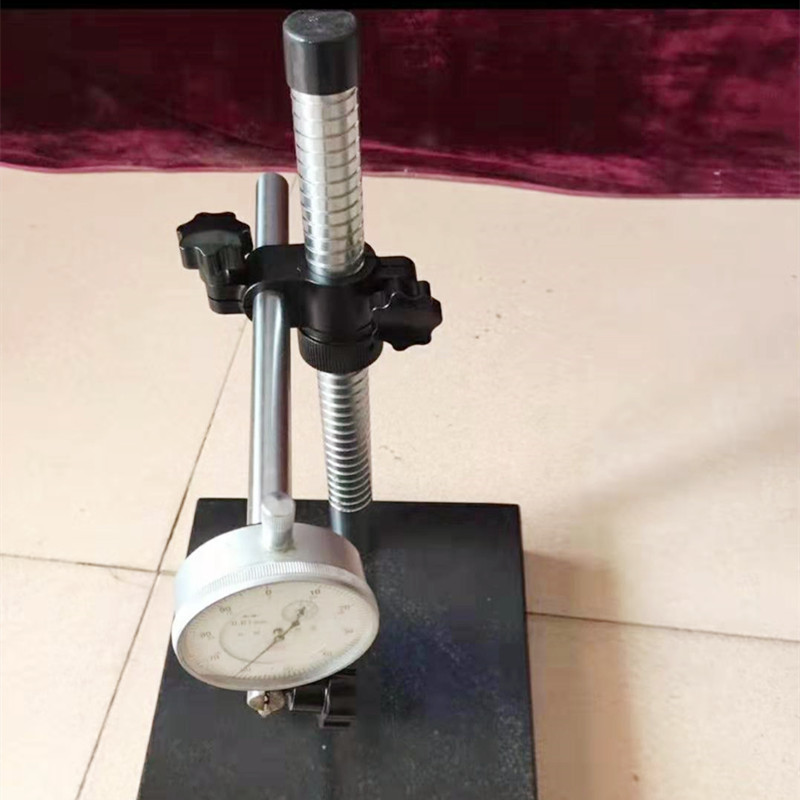
When selecting precision tools and gauges, several factors must be considered to ensure you’re making informed choices. Materials used in the construction of these tools should be of high quality, ensuring durability and consistent performance over time. Brands that offer comprehensive warranties and after-sales service tend to inspire confidence, reflecting their commitment to quality and customer satisfaction.
Moreover, integrating advanced technology with traditional tools is an emerging trend that is rapidly gaining traction. The infusion of digital technology into precision measurement tools, such as digital readouts and software integration, provides manufacturers with more detailed data analysis capabilities. This technological evolution not only enhances measurement precision but also facilitates better decision-making processes through real-time data tracking and analysis.
precision tool and gage
The authority of a manufacturer in the precision tool and gauge market can often be gauged by their industry certifications and adherence to international standards. Certifications such as ISO 90012015 for quality management systems and ISO 17025 for laboratory competence are critical indicators of a company’s commitment to maintaining high standards. Engaging with certified and reputable suppliers guarantees that you’re incorporating trusted tools that meet global benchmarks into your production processes.
Trustworthiness in the realm of precision instruments is further reinforced by endorsements from industry experts and peer reviews. Companies that have established a solid track record of reliability and performance will often have numerous recommendations and case studies demonstrating their impact across various sectors. Networking within industry forums and participating in trade shows can provide additional insights into the reputations of various manufacturers.
The journey toward impeccable precision in manufacturing is continuous. Companies that prioritize regular updates and maintenance of their measurement equipment often experience sustained excellence in product quality. Calibration services offered by qualified professionals ensure that each tool maintains its accuracy and reliability over its operational lifespan. This proactive approach to equipment management plays a significant role in upholding manufacturing standards while fostering a culture of continuous improvement.
In conclusion, the strategic integration of precision tools and gauges, backed by expert knowledge and reliable practices, significantly contributes to the sustained success of manufacturing operations. As the bridge connecting meticulous standards to end products, these tools symbolize a company’s commitment to quality, precision, and innovation. Investing in and nurturing this aspect of the manufacturing process is not merely a choice but a critical step toward achieving exceptional standards in today’s competitive market.