In the realm of metal table fabrication, choosing the right welding methods is crucial for creating durable and high - quality metal fab tables. Storaen (Cangzhou) International Trading Co. understands the significance of these techniques in meeting industry standards.
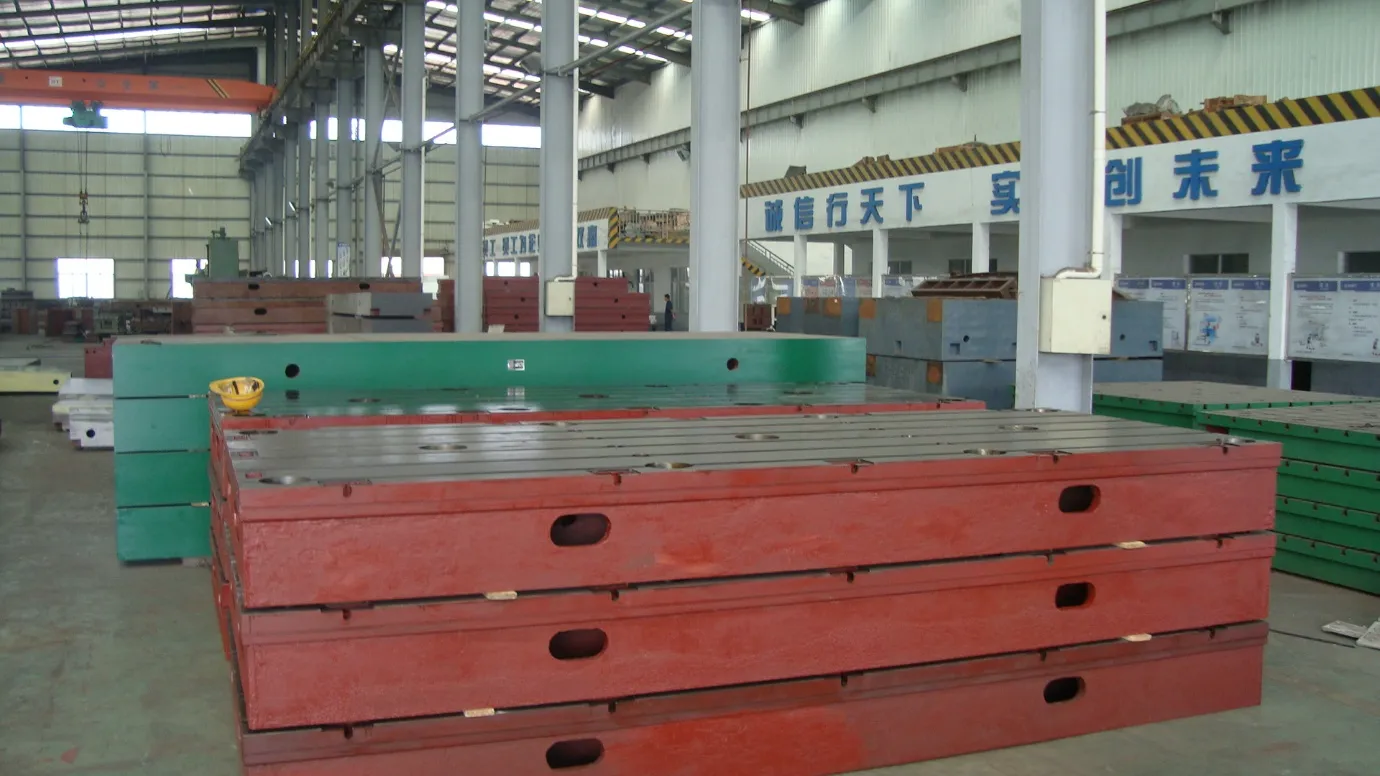
Cast Iron Surface Plate Characteristics Table
Aspect
|
വിശദാംശങ്ങൾ
|
Usage History
|
Used for decades in various industrial settings
|
Key Advantage - Durability
|
Can withstand heavy loads without deforming, suitable for machining and fabrication work
|
Key Advantage - Damping
|
Natural damping properties absorb vibrations, enhancing measurement accuracy
|
Limitation - Corrosion
|
Prone to rust and corrosion if not properly maintained, limiting lifespan
|
Limitation - Maintenance
|
Requires regular scraping to maintain flatness, time - consuming and may need skilled personnel
|
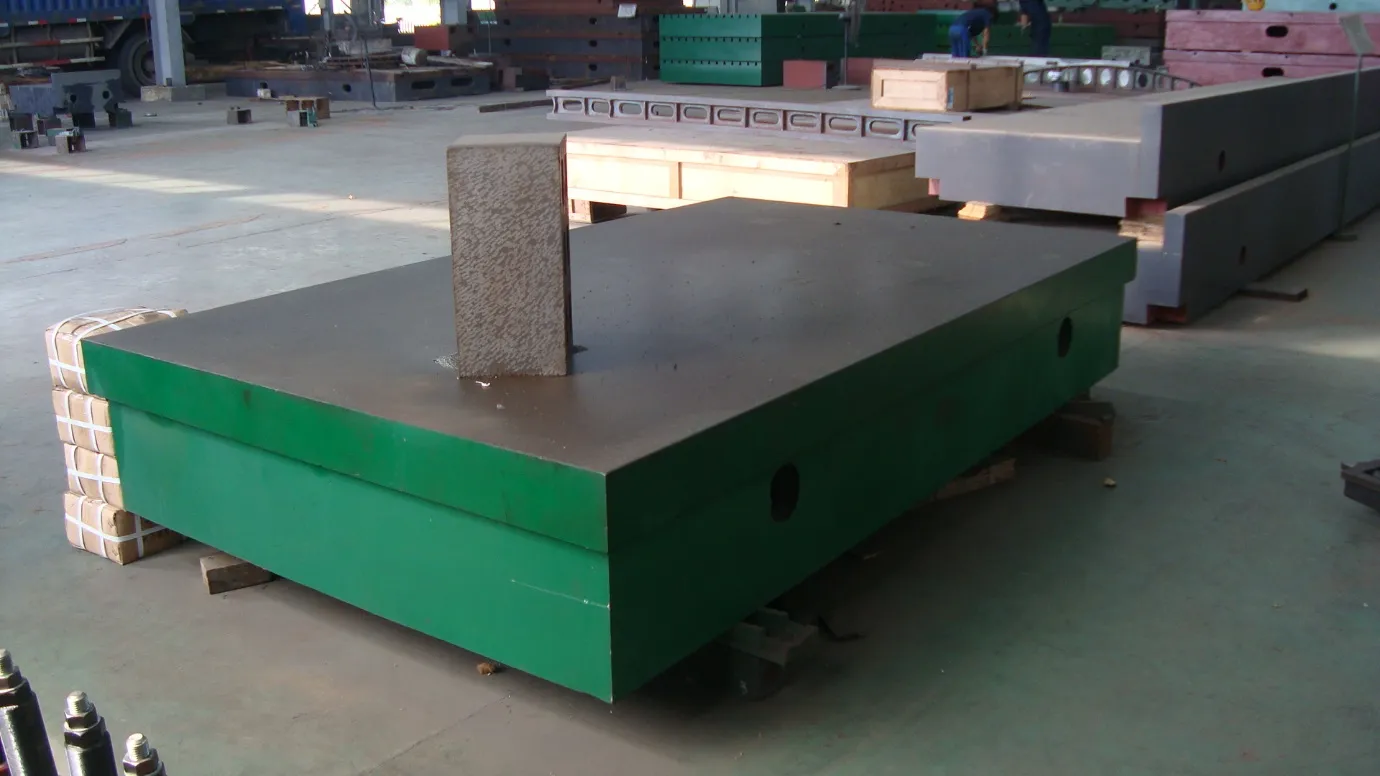
Understanding Metal Table Fabrication
- Metal table fabrication encompasses a series of processes aimed at creating sturdy and functional metal fab tables. Storaen (Cangzhou) International Trading Co. emphasizes the importance of precision in every stage, from material selection to the final assembly. Welding, in particular, plays a pivotal role in joining different metal components together to form a cohesive structure.
- The choice of materials and welding methods in metal table fabricationdepends on various factors, such as the intended use of the table, load - bearing requirements, and environmental conditions. Different welding techniques offer unique advantages and are suitable for specific types of metals and fabrication needs.
- Tools like cast iron surface platescan be used during the fabrication process to ensure flatness and accuracy, especially when aligning and measuring metal components. Their durability and damping properties can contribute to the overall quality of the metal fab table.
-
Common Welding Methods for Metal Fab Tables
- Shielded Metal Arc Welding (SMAW): Also known as stick welding, SMAW is a versatile method commonly used in metal table fabrication. It uses a consumable electrode covered in a flux coating. This flux generates a shielding gas and slag during the welding process, protecting the weld pool from contamination. SMAW can be used on a variety of metals, including mild steel, stainless steel, and cast iron, making it suitable for different types of metal fab table It is relatively easy to learn and can be performed in various positions, even in outdoor or less - controlled environments.
-
- Gas Metal Arc Welding (GMAW): GMAW, or MIG (Metal Inert Gas) welding, is another popular choice. It uses a continuous wire electrode and an external shielding gas, such as argon or a mixture of gases, to protect the weld area. GMAW offers fast welding speeds, high deposition rates, and produces clean, smooth welds. It is well - suited for welding thin to medium - thickness metals, which are often used in the construction of metal fab tables. This method provides good control over the weld bead shape and size, allowing for precise and aesthetically pleasing joints.
-
- Gas Tungsten Arc Welding (GTAW): GTAW, also called TIG (Tungsten Inert Gas) welding, uses a non - consumable tungsten electrode and an inert shielding gas, like argon. It is known for its ability to produce high - quality, precise welds with excellent control over the heat input. GTAW is ideal for welding thin materials and for applications where aesthetics and weld quality are of utmost importance, such as in the fabrication of high - end metal fab tables. However, it requires a higher level of skill and is generally slower than other welding methods.
-
- Flux - Cored Arc Welding (FCAW): FCAW uses a tubular electrode filled with flux. The flux inside the electrode provides shielding during the welding process, eliminating the need for an external shielding gas in some cases. This makes it a convenient option, especially for outdoor or hard - to - reach welding tasks in metal table fabrication. FCAW can handle a wide range of metal thicknesses and is suitable for both structural and non - structural welding of metal fab table
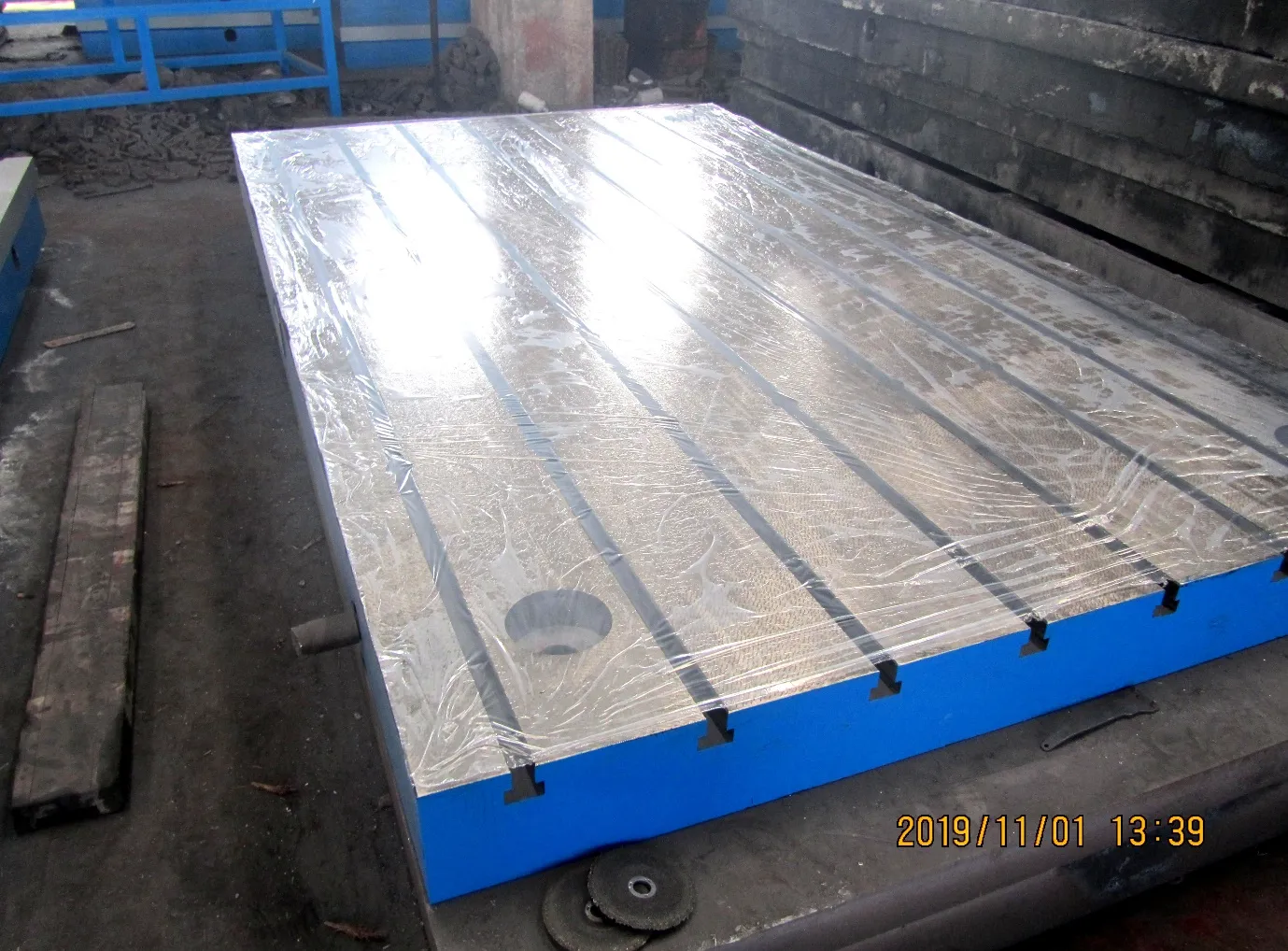
Role of Cast Iron Surface Plate in Metal Table Fabrication
- Ensuring Flatness: Cast iron surface platesserve as a reliable reference surface during metal table fabrication. When cutting, shaping, or assembling metal parts, placing them on a cast iron surface plate helps ensure that they are flat and properly aligned. This is crucial for creating a stable and level metal fab table. The plate's flatness, maintained through regular scraping, provides an accurate base for measuring and marking metal components.
- Vibration Absorption: During welding operations, vibrations can occur, which may affect the precision of the work. The natural damping properties of cast iron surface plateshelp absorb these vibrations, reducing the risk of errors in the fabrication process. This is especially beneficial when working on delicate or precision - oriented metal table fabrication tasks, as it helps maintain the integrity of the metal components and the quality of the welds.
- Supporting Heavy Components: Given their ability to withstand heavy loads without deforming, cast iron surface platescan support the weight of large and heavy metal parts used in metal table fabrication. This allows fabricators to work on substantial components with confidence, knowing that the surface plate can handle the load and maintain its shape, ensuring consistent and accurate results throughout the fabrication process.
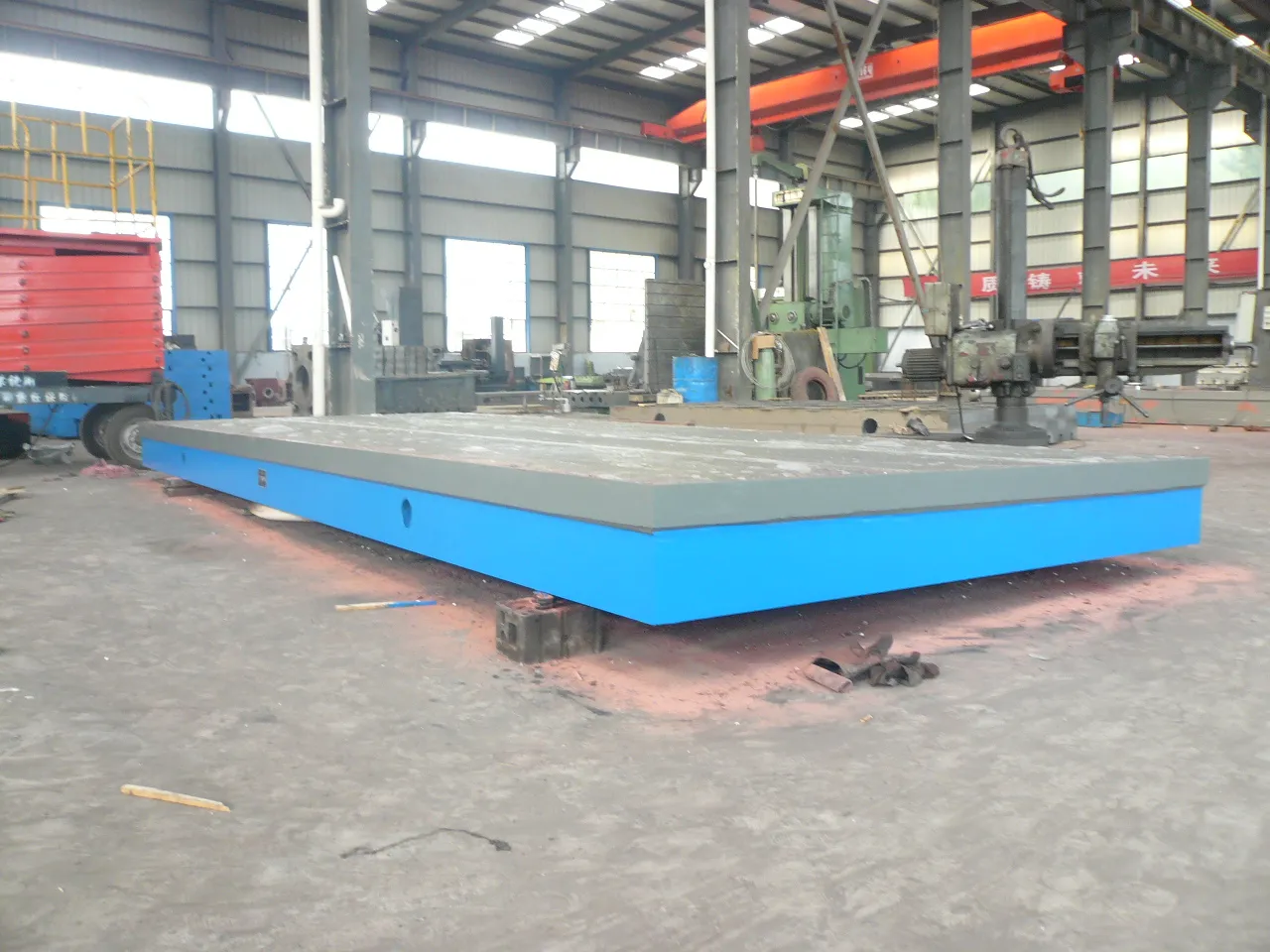
Metal Table Fabrication FAQS
Which welding method is best for thin metal sheets in metal fab table fabrication?
Gas Tungsten Arc Welding (GTAW), or TIG welding, is often the best choice for thin metal sheets in metal fab table fabrication. It offers precise control over the heat input, minimizing the risk of warping or burning through the thin material. This allows for the creation of high - quality, clean welds that are both strong and aesthetically pleasing, making it ideal for crafting delicate or precision - oriented metal table components.
How does a cast iron surface plate contribute to the accuracy of metal table fabrication?
A cast iron surface plate contributes to the accuracy of metal table fabrication in multiple ways. Its flat surface provides a reliable reference for aligning and measuring metal components, ensuring they are properly positioned. The plate's damping properties absorb vibrations during welding and other fabrication processes, reducing errors caused by movement. Additionally, its ability to support heavy loads without deforming allows for stable working conditions, enabling fabricators to achieve consistent and accurate results.
Can different welding methods be combined in metal table fabrication?
Yes, different welding methods can be combined in metal table fabrication. For example, Gas Metal Arc Welding (GMAW) can be used for initial assembly of larger components due to its speed, while Gas Tungsten Arc Welding (GTAW) can be employed for finishing touches or welding thinner sections that require more precision. Combining methods allows fabricators to leverage the strengths of each technique, optimizing the fabrication process and ensuring the best quality for the metal fab table.
What are the potential drawbacks of using a cast iron surface plate in metal table fabrication?
The main drawbacks of using a cast iron surface plate in metal table fabrication include its susceptibility to rust and corrosion if not properly maintained. This can limit its lifespan and require regular upkeep, such as cleaning and applying protective coatings. Additionally, cast iron plates need regular scraping to maintain their flatness, which is a time - consuming process and often requires the skills of experienced personnel. These factors should be considered when integrating cast iron surface plates into the fabrication workflow.
How can wholesalers ensure the quality of metal table fabrication products?
Wholesalers, like Storaen (Cangzhou) International Trading Co., can ensure the quality of metal table fabrication products by carefully selecting fabrication partners with skilled welders and proper quality control processes. They should verify that the appropriate welding methods are used for each project, and that inspections and testing are conducted throughout the fabrication process. Providing clear specifications and requirements to fabricators, and having a system in place to review and approve the final products, also helps maintain high - quality standards for metal fab tables.