Understanding the intricacies involved in purchasing an 80mm gate valve can significantly influence the operations and maintenance of fluid management systems. These seemingly small components play a crucial role in regulating flow, making their purchase a decision not to be taken lightly. Let's delve into the core aspects that determine the price and performance of 80mm gate valves.
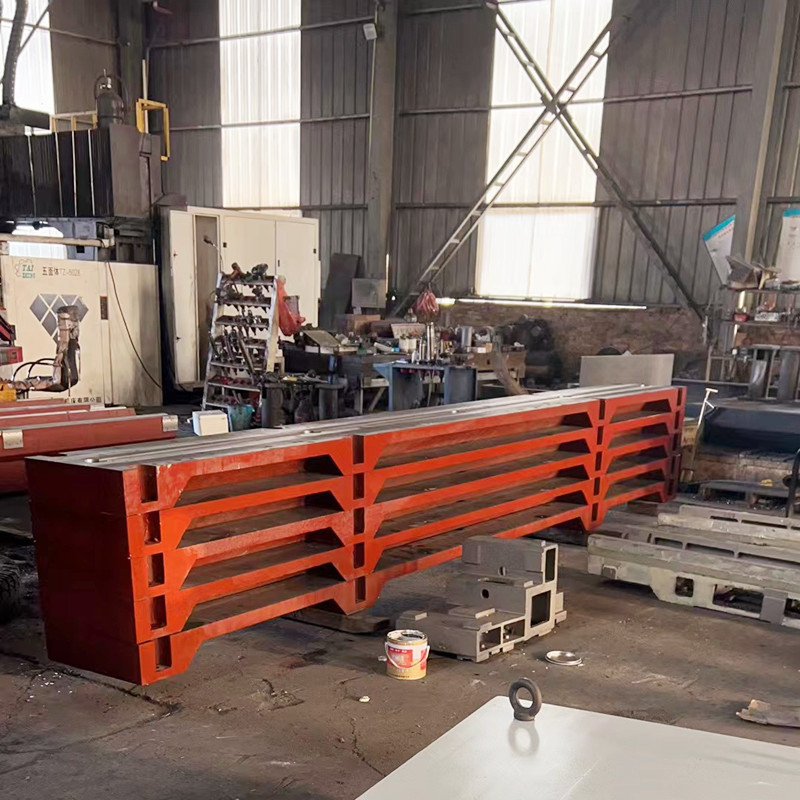
A gate valve, fundamentally, is a universally employed component used to control the flow of liquids or gases by using a gate or wedge to block the path. When considering a gate valve of 80mm size, companies must evaluate a variety of factors that affect both initial purchase costs and potential long-term operational expenses.
One of the primary considerations is the material used in manufacturing the gate valve. The material not only implicates the durability but also dictates the specific applications the valve is suitable for. Common materials include stainless steel, cast iron, and brass. Stainless steel valves, for instance, boast excellent resistance to corrosion, making them ideal for industries where purity and contamination prevention are crucial, such as in pharmaceuticals or food and beverage. Consequently, they often come at a higher price point due to their longevity and effectiveness in harsh conditions. Cast iron, although more economical, might be susceptible to corrosion over time, which could increase maintenance costs.
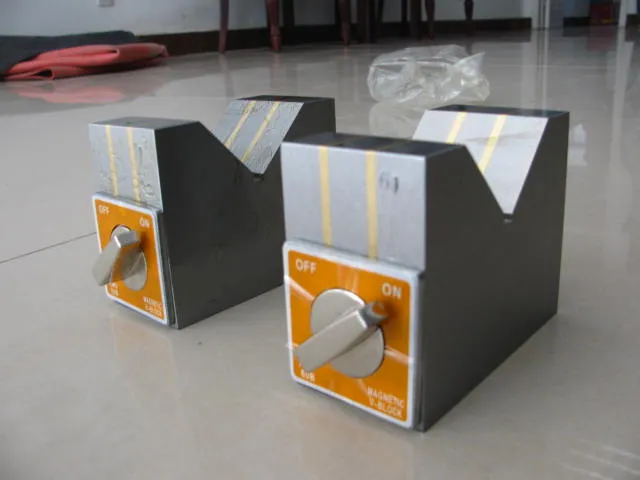
The valve's operation mechanism, whether manual or automated, further influences pricing. Automated valves, offering remote operational capabilities, significantly enhance efficiency, especially in complex systems where manual operation may be impractical or hazardous. However, this convenience reflects in the initial cost outlay, which could be considerably higher than their manual counterparts.
Manufacturing brands also play a pivotal role in determining the price range of these valves. Established brands often command higher prices, justified by their reputation for quality and after-sales service. Moreover, these manufacturers frequently offer broader warranties and certifications, ensuring conformity with international standards, which can be particularly critical in regulated industries like chemicals and gas.
80mm gate valve price
The geographical location where the valve will be sourced is another factor impacting pricing. Import regulations, shipping costs,
and tariffs can all influence the final purchase price. Local sourcing might reduce some of these additional costs, but it might limit the choices available based on the domestic manufacturing capabilities.
Furthermore, the valve's pressure rating and temperature tolerance are quintessential for ensuring it will operate effectively within the specified system parameters. Valves that withstand higher pressures and temperatures typically require more advanced engineering and materials, thus increasing costs. However, the reliability and safety they offer could offset higher initial expenses by preventing costly downtimes and repairs.
Not to be overlooked are the certifications and compliance standards adhered to by the valve manufacturer. Compliance with international standards such as ISO, ANSI, or API ensures that the valve meets stringent quality and safety benchmarks. Choosing a certified valve can provide peace of mind and mitigate operational risks, although it may elevate the buying price slightly.
To conclude, investing in an 80mm gate valve is a decision that should be guided by a comprehensive assessment of operational requirements, environmental conditions, and budgetary considerations. While seeking to find a balance between cost and quality, understanding the complete lifecycle costs including maintenance, reliability, and potential downtime is essential. Making an informed choice ensures longevity and optimal performance of the system, thereby delivering sustained value over time. Always consult with seasoned industry experts and conduct thorough market research to secure a valve that meets both current and future operational needs. This proactive approach underpins not just a competitive edge in pricing but also fortifies the foundation for robust and effective fluid management infrastructure.