Control valves are pivotal components in various industrial processes, precisely controlling the flow of liquids or gases. Their importance cannot be overstated, as they directly impact productivity, efficiency, and safety.
Choosing the right type of control valve for specific applications can be daunting due to the myriad of options. Here, we delve into various types of control valves, highlighting their distinct functions and advantages.
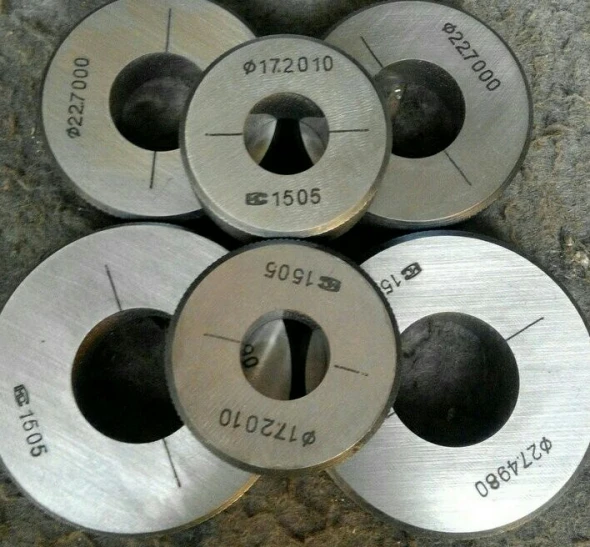
Understanding Control Valves A Crucial Component in Modern Industry
The primary role of control valves is to regulate process variables such as flow, pressure, temperature, and liquid level by fully or partially opening or closing. Given their critical function, selecting the appropriate valve requires an in-depth understanding of the process requirements and operating environment.
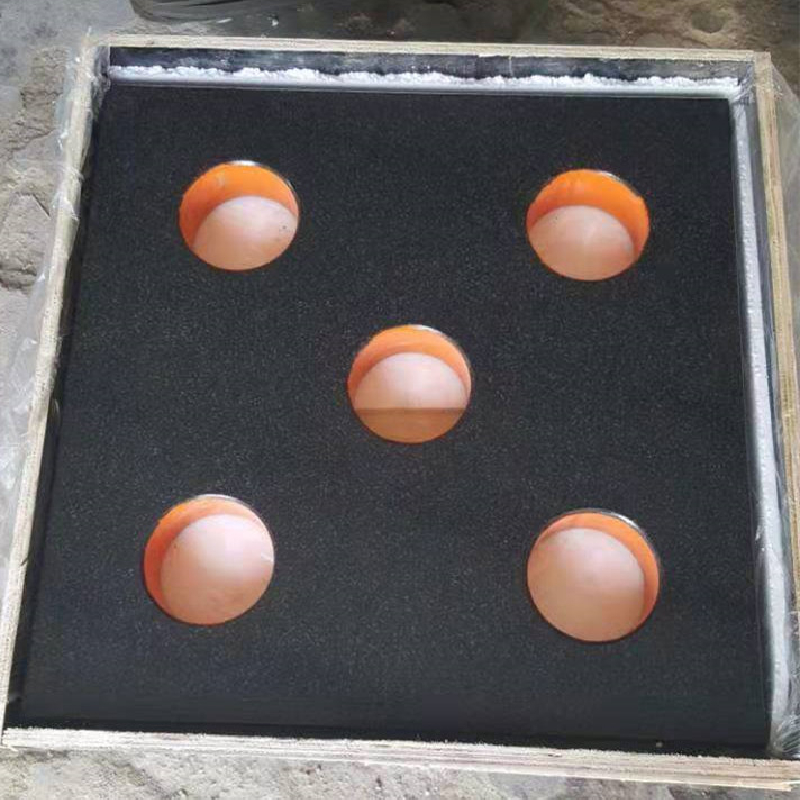
1. Ball Valves Efficiency and Reliability
Ball valves are renowned for their excellent shut-off capability. They employ a simple mechanism — a ball with a hole through its center that rotates to open or close the valve. The main advantage of ball valves lies in their durability and reliability, often used in applications where a tight shut-off is crucial. Their simplistic design makes them easy to operate and maintain, making them a preferred choice in industries ranging from oil and gas to water treatment.
2. Butterfly Valves Cost-Effectiveness and Light Weight
Butterfly valves consist of a rotating disc to regulate flow. Their primary selling points are their lightweight design and cost-effectiveness. They require less material compared to other valve types and are quick-acting, making them ideal for processes involving large volumes of fluid or low-pressure drop. Butterfly valves are frequently used in water distribution systems and pulp and paper industry processes, where space and weight are concerns.
3. Globe Valves Precision in Control
various types of control valves
Globe valves are distinguished by their spherical shape and proven design, which is highly effective for flow regulation. They are widely used for applications requiring precise control and throttling, making them suitable for industries like chemical processing and power generation. The specific design reduces leakage risk and allows for easy maintenance, but they can offer higher resistance to flow compared to other types, which must be considered in high-pressure applications.
4. Diaphragm Valves Versatility and Safety
Diaphragm valves are unique due to their design, which utilizes a flexible diaphragm to separate the flow medium from the closure element. Their corrosion resistance and suitability for clean or sterile applications make them invaluable in the food, pharmaceutical, and water treatment industries. Additionally, diaphragm valves support excellent leak-tight performance, ideal for hazardous or corrosive media handling.
5. Gate Valves Unrestricted Flow and Minimal Pressure Loss
Gate valves feature a sliding gate to open or close the valve, providing minimal pressure loss and unrestricted flow when fully open. Their design is particularly suitable for applications requiring infrequent operation, like starting or stopping flows, and they are commonly found in the oil, gas, and mining industries. Despite slower operation compared to other valve types, their ability to handle high pressures and temperatures cannot be understated.
Conclusion
Deciphering the nuances of various control valves enriches decision-making processes, ensuring that industrial systems are optimized for maximum efficiency and safety. Valves must be chosen based on specific process requirements, operating conditions, and material compatibility. By considering these factors, industries can achieve better control, reduced downtime, and enhanced operational performance.
Proper valve selection not only increases productivity but also significantly impacts environmental and economic sustainability. With technological advancements continually reshaping valve design and functionality, staying informed about the latest innovations remains essential for engineers and process managers aiming to maintain a competitive edge. Each valve type discussed here offers distinct benefits, underscoring the importance of tailored solutions to meet unique industrial challenges.