Control valves are essential components in various industries, regulating the flow of fluids to ensure optimal system performance. Understanding the different types of control valves and their specific applications can significantly enhance the efficiency and security of industrial processes.
This article provides a comprehensive guide to control valve types and their applications, integrating both practical experience and authoritative insights.
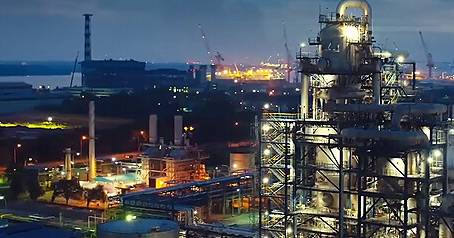
Control valves can be classified into several types linear motion, rotary motion, specialty, and advanced technology valves. The choice of a particular type often depends on the specific requirements of the application, including factors such as fluid characteristics, pressure conditions, system dynamics, and environmental concerns.
Linear motion valves, such as globe and diaphragm valves, are typically favored in applications requiring precise flow control. Globe valves, with their robust design, are ideal for throttling services, allowing for fine adjustment of fluid flow. These valves are commonly used in power plants and oil refineries, where the control of steam, water, and gas is crucial for operational safety and efficiency. On the other hand, diaphragm valves are preferred in the pharmaceutical and food industries. Their unique sealing mechanism provides excellent containment, essential for maintaining sanitary conditions and preventing contamination.
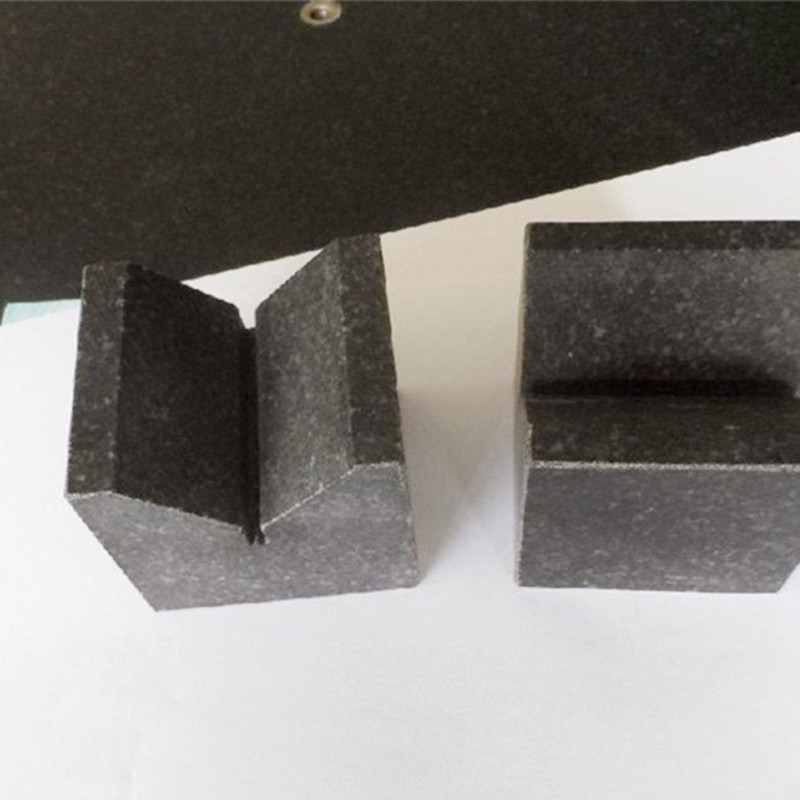
Rotary motion valves, which include ball, butterfly, and plug valves, offer quick shut-off and are generally simpler in design than linear motion valves. Ball valves are prevalent in pipelines for their durability and reliable sealing, being suitable for high-pressure applications where tight shut-off is necessary. Butterfly valves, recognized for their compact size and low-pressure drop, are widely used in water treatment plants and HVAC systems. Their lightweight structure and efficient operation make them an economical choice for managing large volumes of fluid.
Specialty valves such as pinch, needle, and pressure relief valves serve highly specific functions. Pinch valves are ideal for handling abrasive or corrosive slurries and are extensively used in the mining and wastewater treatment industries. Needle valves, with their fine-thread adjustment capabilities, are perfect for precise flow control in instrumentation and measurement applications. Pressure relief valves play a critical role in safeguarding systems, preventing overpressure conditions by allowing fluid to escape when preset pressure limits are exceeded.
control valve types and applications
Advanced technology valves include smart control valves equipped with sensors and automation capabilities, providing real-time data and remote controllability. These valves are crucial in Industry 4.0 environments, enhancing predictive maintenance and reducing downtime through data-driven insights. For instance, in chemical processing plants, smart valves optimize flow control based on real-time analytics, improving energy efficiency and product quality.
The expertise involved in selecting and implementing control valves is paramount for optimal system performance. Thorough understanding of the process conditions, combined with knowledge of the properties of the fluid being transported, is vital for choosing the right valve type. Moreover, consideration of factors such as valve material, size, and actuation mechanism ensures that the valve will perform effectively under the specified conditions.
Authoritative sources such as the International Society of Automation (ISA) and leading valve manufacturers provide extensive guidelines and best practices for valve selection and maintenance. Adherence to these standards not only prolongs the lifespan of the valve but also enhances the trustworthiness of industrial operations, minimizing the risk of system failures and ensuring regulatory compliance.
In conclusion, the selection of control valve types involves a blend of technical knowledge, industry experience, and adherence to authoritative guidelines. By combining these elements, industries can achieve optimal efficiency, safety, and reliability in their processes. Awareness of the latest advancements and trends in valve technology is essential for maintaining competitiveness and operational excellence in today's rapidly evolving industrial landscape.