Hydraulic ball check valves are an indispensable component in hydraulic systems, renowned for their reliability and functionality. These devices, which allow fluid to flow in one direction while preventing reverse flow, play a crucial role in ensuring system efficiency and longevity. Their simple yet effective design makes them a preferred choice in various industrial applications, from manufacturing to automotive systems.
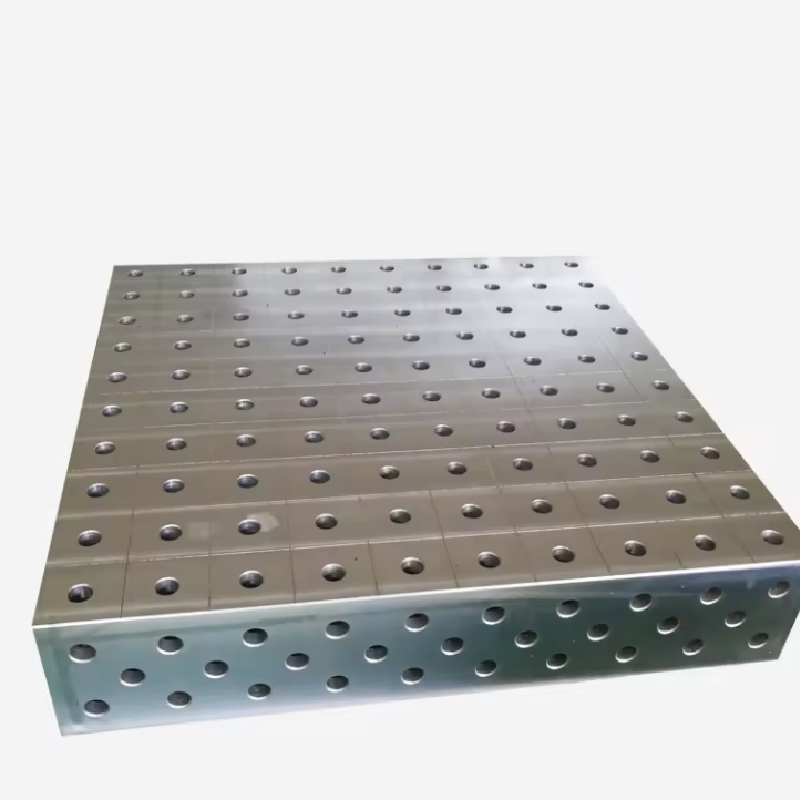
Choosing the right hydraulic ball check valve is critical for system optimization. These valves consist of a spherical ball that seals against a seat within the valve body. When fluid pressure is applied in the desired direction, the ball lifts off the seat, allowing fluid to pass. When the flow reverses, the ball returns to the seat, preventing backflow. This action safeguards system components from damage caused by reverse flow, such as pump or actuator failure.
The construction material of hydraulic ball check valves significantly influences their performance and suitability for specific applications. High-grade stainless steel is often favored due to its robustness, corrosion resistance, and ability to withstand high pressures and temperatures. In environments where chemicals are present, materials like Teflon or PVC may be used to offer added chemical resistance. Selecting the appropriate material ensures the valve's durability and minimizes maintenance requirements.
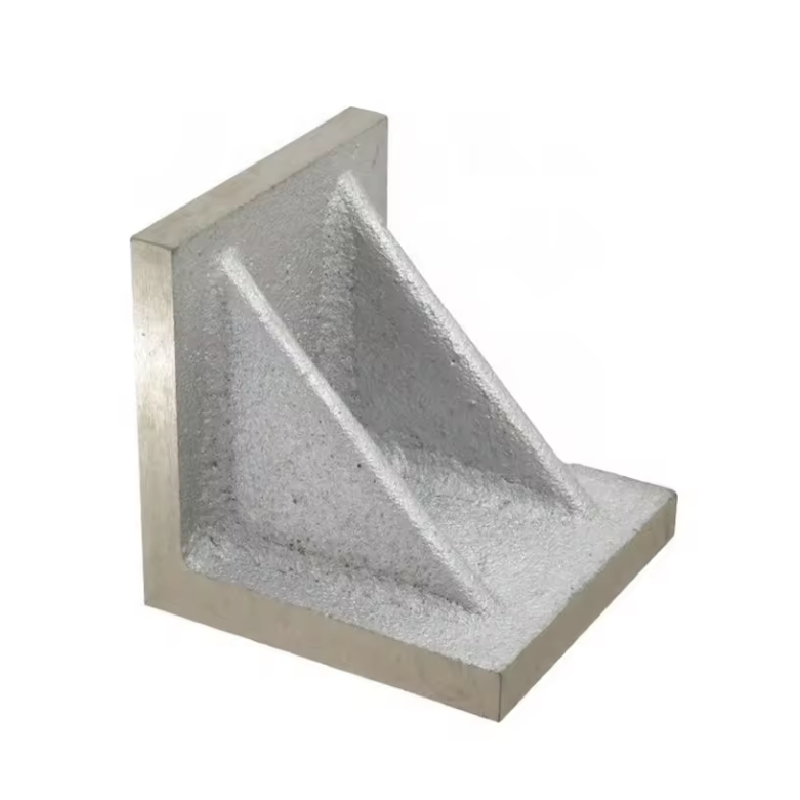
The importance of size and pressure ratings cannot be overstated. Valves must be correctly sized to match the flow rate of the hydraulic system, which ensures optimal performance and prevents undue stress on the valve and system components. Similarly, understanding the pressure rating is crucial; a valve rated for a lower pressure could fail, leading to costly downtimes and repairs. Consulting the system’s specifications with a valve distributor or engineer can aid in proper selection, ensuring compatibility with existing systems.
Installation and maintenance of hydraulic ball check valves require attention to detail and expertise. Proper installation involves ensuring that valves are aligned correctly with the flow direction clearly defined by the manufacturer's instructions. Misalignment can lead to inefficient operation or system failure. Regular maintenance checks, such as inspecting the ball and seat for wear and cleaning any debris or buildup, prolong the valve’s life and functionality.
hydraulic ball check valve
For industries relying on hydraulic systems, the choice of hydraulic ball check valves is a strategic decision that affects operational efficiency and cost-effectiveness. Advanced features such as quick-connect fittings and enhanced sealing options are available and should be considered when selecting a valve to further enhance system performance.
In addition to practical considerations, industry standards and certifications offer guidance on valve selection. Standards such as the ISO 90012015 for quality management systems and API certifications for manufacturing standards help ensure the products meet rigorous quality and safety requirements. Selecting certified valves from reputable manufacturers can enhance the system's credibility and reliability, as well as provide peace of mind to end-users.
The recent technological advancements have also influenced the manufacturing of hydraulic ball check valves. Innovations in material science have led to the development of composite materials that offer superior strength-to-weight ratios and enhanced durability. Furthermore, digital monitoring solutions integrated into hydraulic systems now allow for real-time diagnostics and predictive maintenance, which helps in maximizing valve performance and preventing unexpected failures.
Ultimately, hydraulic ball check valves are more than mere components; they are vital to the safety and efficiency of hydraulic systems. By understanding the nuances of their operation, material composition, size, pressure ratings, and installation practices, industry professionals can make informed decisions that optimize their systems' performance and extend operational life. Staying abreast of industry standards and technological advancements ensures that these valves continue to serve as reliable and cost-effective solutions in an ever-evolving industrial landscape.