Crafted predominantly from cast steel, gate valves are integral components within various industries due to their sturdy structure and reliable performance in fluid control. Gate valves operate by lifting or lowering a gate, hence named, to block or allow fluid passage. This mechanism provides an unobstructed flow path with minimal resistance, making them ideal for applications needing a full open or closed system. Let's delve into the unique features, benefits, and considerations associated with cast steel gate valves.
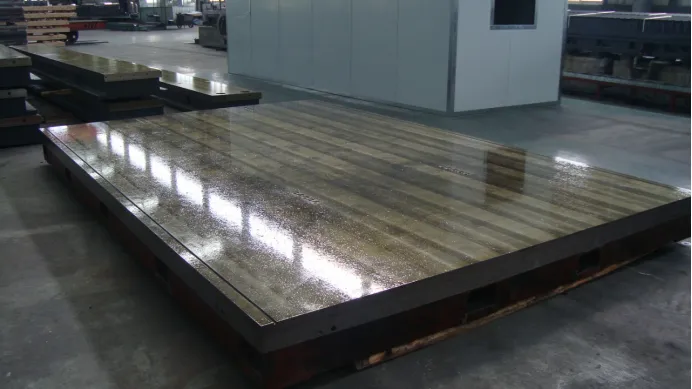
Renowned for their durability, cast steel gate valves are commonly favored in high-pressure environments. Cast steel's strength offers resilience against the stress of high temperature and pressure fluctuations, ensuring service continuity even in challenging conditions. Such robustness is pivotal in industries like oil and gas, petrochemicals, and power generation, where operational efficiency is paramount.
In terms of expertise, cast steel provides an advantageous toughness-to-weight ratio. Its ability to withstand mechanical stress without deformation elongates the operational life of gate valves. Industries often opt for cast steel due to its weldability, allowing for seamless integration into pipelines, which is crucial for maintaining a leak-proof operation. Furthermore, various alloys of cast steel can be utilized to enhance characteristics like resistance to corrosion, making these valves adaptable to different fluids and environments.
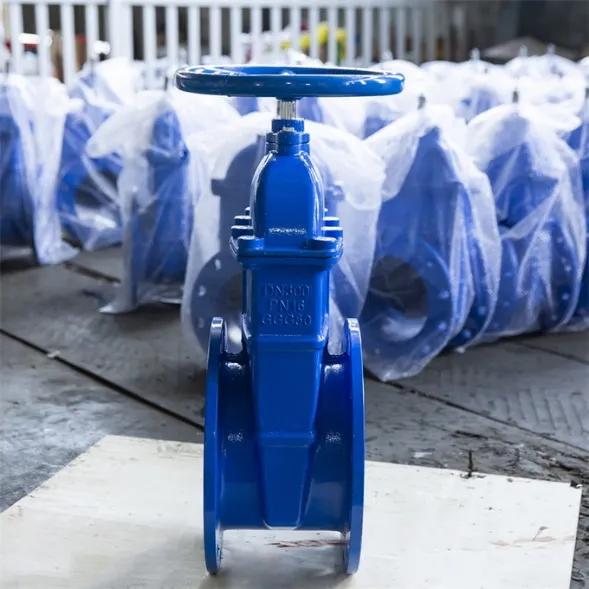
Authoritativeness often comes from design precision, and cast steel gate valves are engineered with this in mind. The manufacturing process of casting allows for complex shapes and sturdy configurations, essential for ensuring a tight seal when the valve is closed. The precision in design not only enhances operational efficiency but also contributes to safety by minimizing leakage risks, a critical factor in hazardous fluid handling.
The expertise inherent in cast steel gate valves extends to maintenance efficiency, providing return on investment through reduced downtime. Regular inspections and basic servicing can sustain their performance over many years. Moreover, the availability of standardized parts enhances maintenance procedures, ensuring timely and cost-effective repairs when necessary. This factor contributes significantly to the trustworthiness of cast steel gate valves in industry applications.
gate valve cast steel
When considering trustworthiness, performance consistency and safety are key. The integrity of cast steel gate valves is upheld through rigorous testing and adherence to international standards. Certification from industry bodies assures compatibility with engineering benchmarks, instilling confidence in their use across various sectors. The reliability of these valves in maintaining system integrity underpins their standing in industrial applications, where any malfunction can lead to significant operational hazards.
While cast steel gate valves offer numerous benefits, they also require careful consideration regarding operational environment and fluid characteristics. It is crucial to evaluate factors such as temperature, pressure, and chemical composition of the fluid being controlled, ensuring that the selected valve meets all application-specific requirements. Consultation with technical specialists is advisable during the selection phase to optimize performance and longevity.
In addition to mechanical performance, cast steel gate valves are cost-effective solutions relative to their lifespan, making them an economical choice for long-term projects. Initial costs are often offset by their durability and low maintenance needs, providing substantial savings over time.
Conclusively, cast steel gate valves embody a harmonization of advanced engineering and practical functionality. Their adoption in diverse industries is a testament to their capability in providing fluid control that is both efficient and reliable. With continual advancements in materials and design, the future of cast steel gate valves looks promising, ensuring their role remains vital in evolving industrial landscapes. Investing in these robust components means prioritizing operational safety, efficiency, and sustainability, key tenets for any modern industrial operation.