Navigating the landscape of metalwork measuring tools requires not only an understanding of the tools themselves but also how they enhance precision and quality in metalworking projects. Whether you're crafting intricate components in aerospace or assembling robust structures in construction, the right measuring tools make all the difference between a project’s success and failure.
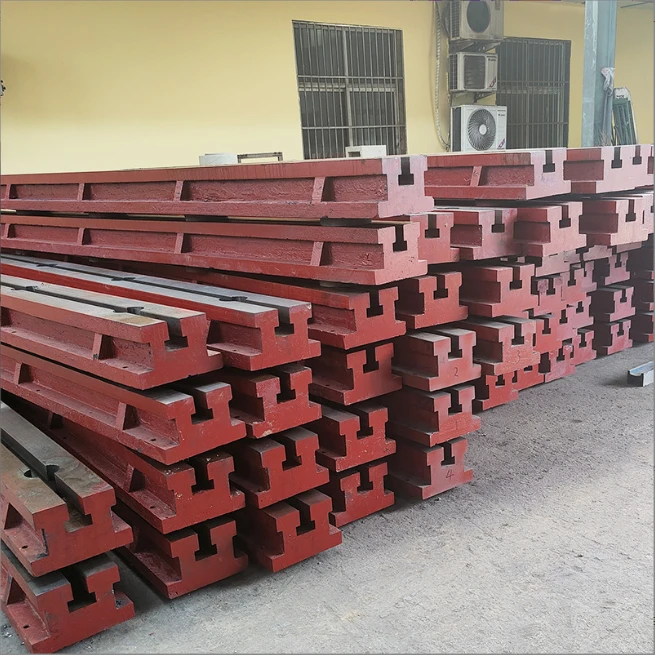
1. Understanding Precision Tools Calipers and Beyond
Calipers have long been the cornerstone of precision measurement in metalworking. With digital calipers now offering the speed and accuracy that surpass their vernier ancestors, metalworkers can attain up to 0.01mm precision. This level of accuracy is essential, especially in fields requiring stringent tolerances. Alongside calipers, micrometers provide even greater precision levels, ideal for gauging thicknesses and external dimensions of small objects. The typical micrometer offers a precision of up to 0.001mm,
essential for exact measurements in industries like aerospace.
2. Embracing Advanced Technologies Laser and Optical Measuring Systems
Laser measuring tools have revolutionized metalwork with their non-contact precision and capability to measure over extended distances. These tools often integrate software solutions that allow for three-dimensional measurement, offering unparalleled accuracy in both production and quality assurance processes. Optical comparators, another technological marvel, facilitate complex measurements by magnifying the part and overlaying it with an engineering drawing to ensure adherence to design specifications.
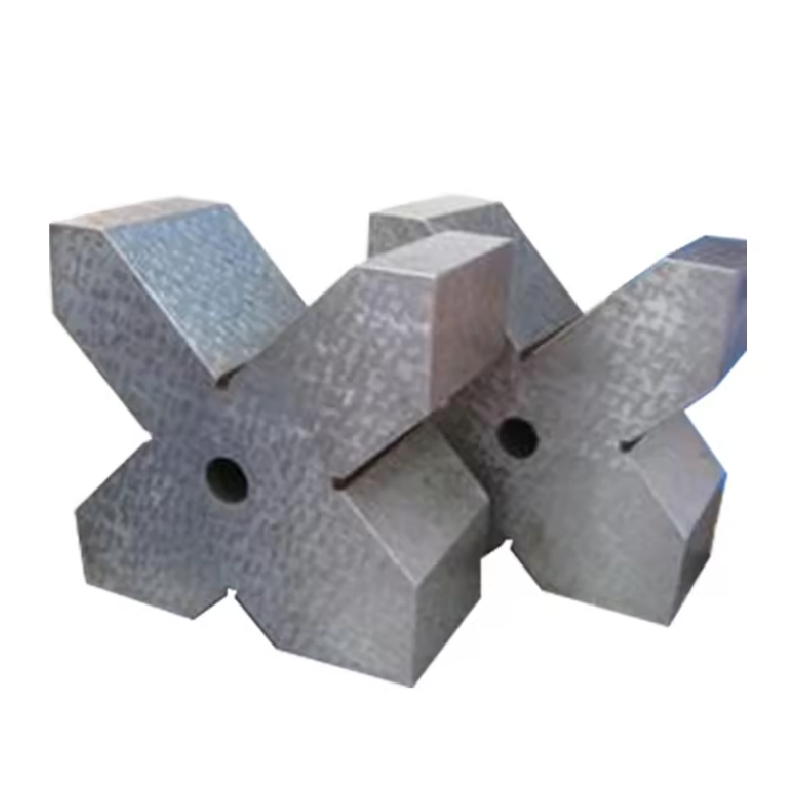
3. The Role of Coordinate Measuring Machines (CMMs)
Coordinate Measuring Machines stand at the pinnacle of measurement accuracy, employing computer-controlled systems to capture the geometry of physical objects with precision. Industries such as automotive and aerospace rely heavily on CMMs to certify that components meet rigorous quality standards. With the ability to measure hermetically sealed parts in 3D, CMMs mitigate error, reduce material waste, and enhance productivity.
4. Employing Traditional Tools The Value of Rulers and Squares
Despite advancements in technology, traditional tools like rulers and squares remain integral in metalwork for preliminary measurements and angle verification. Combination squares, in particular, offer a multifunctional tool adept at checking 90-degree angles, pinpointing centers, and comparing heights—a practical choice for quick checks and simple tasks where high precision is not the sole priority.
measuring tools for metal work
5. Ensuring Accuracy with Dial Indicators
Dial indicators are indispensable in aligning machinery and ensuring parts meet specifications during both dial test indicator applications and critical tolerance assessments. With their ability to measure diminutive deviations in alignments or surface flatness, these tools are vital for processes demanding meticulous attention to detail—often a deciding factor in the quality of the final product.
6. Training and Maintenance Securing Longevity and Efficacy
Training is key in leveraging the full potential of these sophisticated tools. Without adequate knowledge, even the most advanced systems are rendered ineffective. Regular maintenance ensures longevity and reliability, with calibration being crucial for maintaining measurement accuracy. Workshops that train personnel on how to handle, store, and calibrate these instruments correctly are non-negotiable for maintaining a competitive edge.
7. Safety Protocols Protecting Users and Equipment
Beyond usage, adherence to safety protocols cannot be overemphasized, especially when using high-technology measuring systems. Proper handling reduces the risk of damage to sensitive equipment and also protects the user from potential hazards. Wearing appropriate personal protective equipment (PPE) and following operational guidelines safeguards both human and hardware resources.
In conclusion, selecting the appropriate measurement toolset involves understanding each tool’s unique advantages and how they complement one another to enhance metalwork precision. For professionals committed to excellence, investing in high-quality tools, continuous training, and regular maintenance routines ensures that measurements are not just numbers but represent meticulous accuracy that fosters trust and reliability in every metalwork project. Embracing both traditional and advanced measurement systems reflects a balanced strategy, underscoring the expertise necessary to excel in modern metalwork.