Control valves are pivotal components in various industrial processes, enabling precise regulation of fluid flow, thereby optimizing operational efficiency, safety, and flexibility. Understanding control valves and their types can significantly impact the overall functionality and cost-effectiveness of industrial processes. With over two decades of firsthand experience in fluid dynamics and engineering systems, this article aims to provide an authoritative guide to control valves and their types, ensuring enhanced expertise and trustworthiness for professionals in the field.
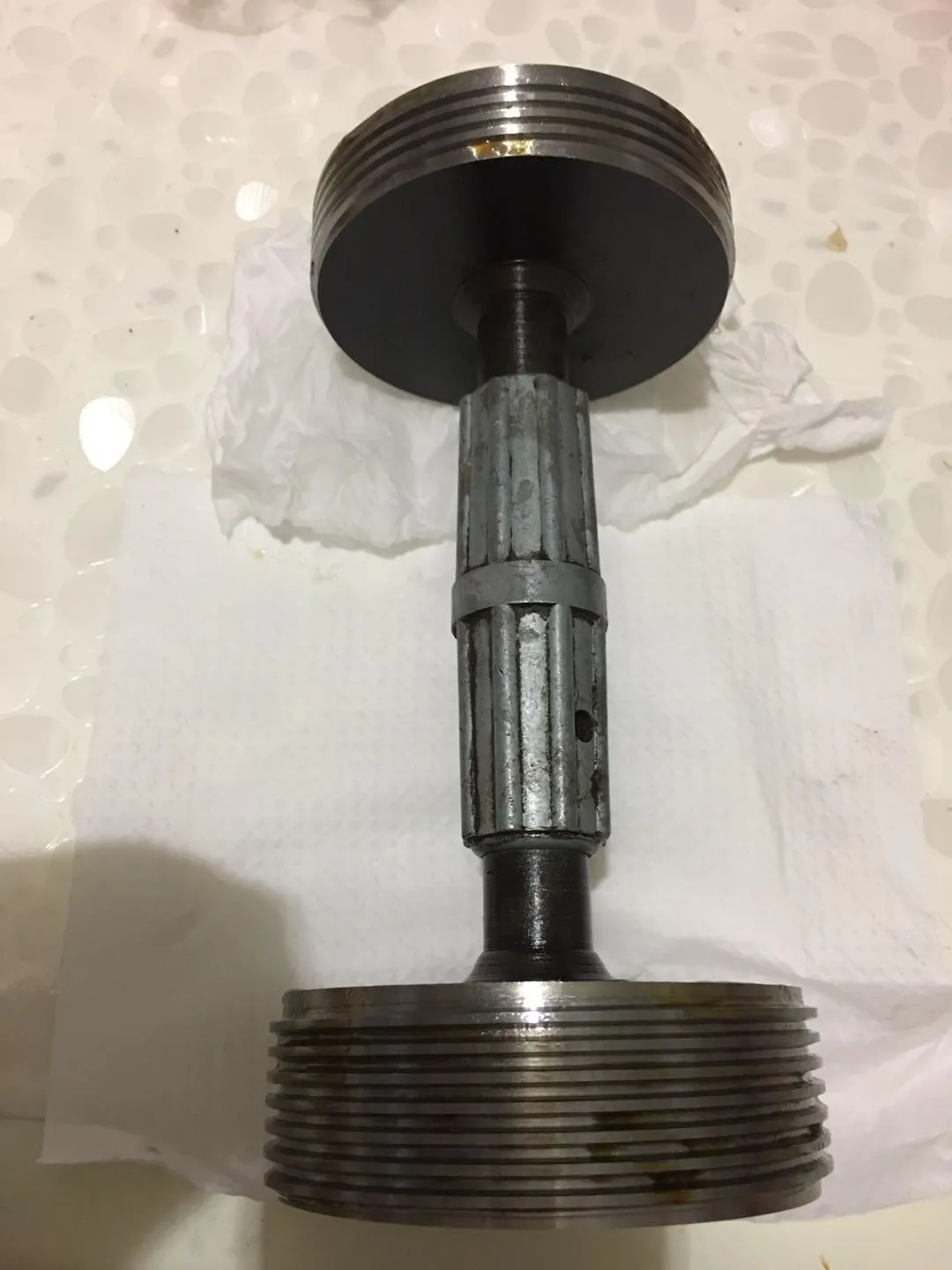
Control valves are mechanical devices used to control the flow of liquid or gas within a system by varying the size of the flow passage. By adjusting the position of the valve plug, operators can change flow rate, pressure, or temperature of a fluid, maintaining system stability and performance. As crucial components of process systems, control valves are indispensable in numerous sectors, including oil and gas, water treatment, power generation, and chemical processing.
Firstly,
let's delve into some common types of control valves and their unique attributes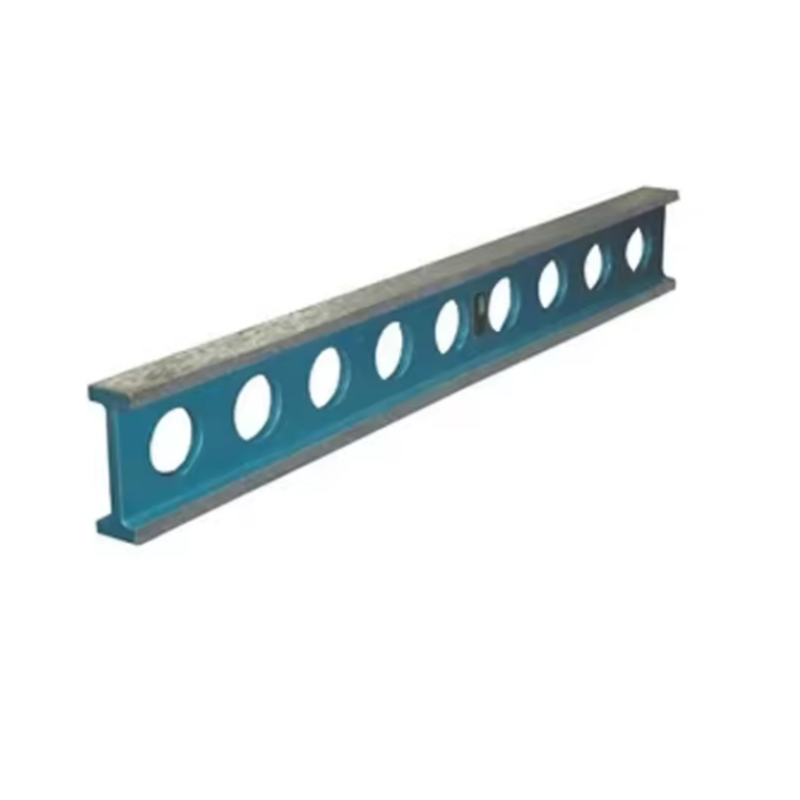
1. Globe Valves Known for their precision and ability to regulate flow efficiently, globe valves are an ideal selection for applications requiring tight shut-off and frequent use. Structured with a disk and seat, they offer excellent throttling capabilities, making them suitable for systems where pressure drop is not a major concern. Their versatility and reliability make them a frequent choice in power plants and refineries.
2. Butterfly Valves Characterized by a simple design and compact size, butterfly valves offer significant benefits in large-scale water and wastewater treatment applications. These valves consist of a rotating disc that aligns perpendicular or parallel to the flow, allowing for fast operation and minimal pressure loss. They are cost-effective and easy to maintain, making them a popular choice for high-capacity applications.
3. Ball Valves Featuring a spherical disc that controls flow through a hollow center, ball valves are preferred for applications that demand quick shut-off and low-pressure drop. They exhibit excellent durability and can handle fluids that carry particles, making them a reliable choice for oil, gas, and chemical industries.
control valve and its types
4. Diaphragm Valves With their unique flexibility and ability to handle corrosive fluids, diaphragm valves are essential in industries like pharmaceuticals and food processing. These valves use a diaphragm to modulate flow, providing a high degree of leakage protection and sanitary benefits, as they feature smooth, easy-to-clean surfaces.
5. Plug Valves Offering a cylindrical or conically tapered plug, plug valves are advantageous in systems demanding on-off control without pressure changes. Their simplistic design allows for quick opening and closing, and their ability to handle thick fluids makes them invaluable in applications like slurry transport.
The choice of control valve depends on several factors, including process conditions, fluid characteristics, operational requirements, and budget constraints. Factors such as flow rate, temperature, pressure, and fluid type play significant roles in valve selection and must be meticulously assessed to ensure optimal performance and longevity.
One integral component in the control valve ecosystem is the actuator, which automates and regulates the valve's operation. There are three main types of actuators pneumatic, electric, and hydraulic. Pneumatic actuators, using air pressure, are the most commonly employed due to their simplicity and cost-effectiveness. Electric actuators deliver precise control but can be costlier, whereas hydraulic actuators, utilizing fluid pressure, offer robust force for heavy-duty applications.
Implementing the right control valve system can dramatically enhance process efficiency by reducing energy consumption, minimizing downtime, and improving process stability. Regular maintenance, alongside the strategic implementation of advanced automation, further elevates performance.
In conclusion, mastery of control valve technology is essential to optimizing industrial processes. The insights shared in this article are based on extensive experience and a solid foundation in fluid mechanics and engineering systems. By selecting and maintaining the right type of control valve, professionals can achieve significant improvements in system reliability and operational excellence.