Ensuring optimal performance and longevity of industrial systems often hinges on the small yet vital component known as the check valve. A clean check valve is indispensable in maintaining system efficiency and preventing reverse flow, which can lead to costly damages and downtime. Drawing on years of experience in engineering and specializing in fluid dynamics, I've seen firsthand the profound impact a properly maintained check valve can have on a system's operational success.
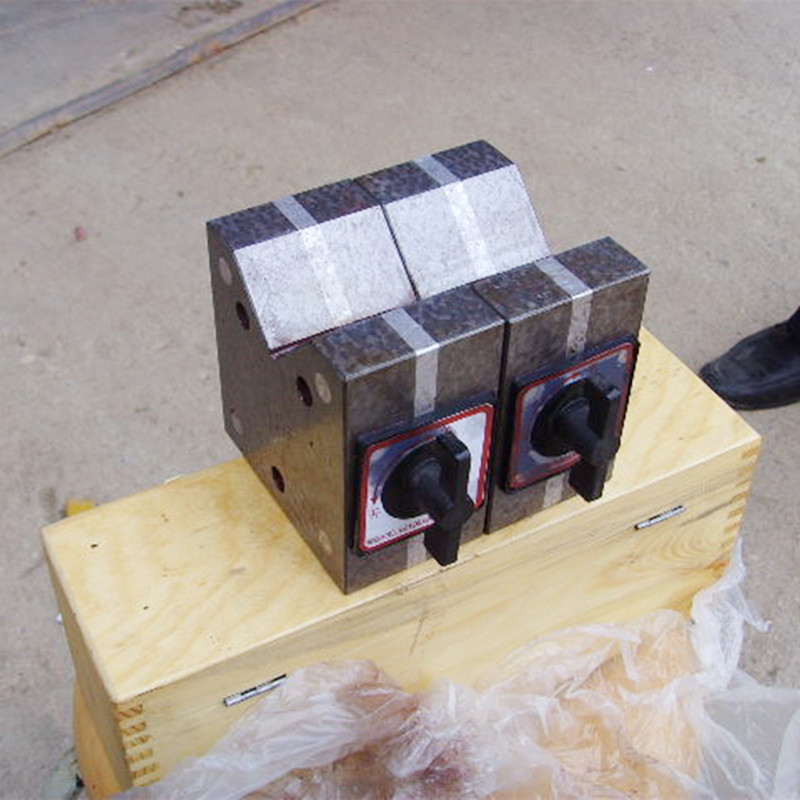
Check valves are designed to allow fluid to flow in one direction while preventing backflow, thus safeguarding pumps and compressors from potential damage. They are crucial in a variety of settings, from municipal water supply systems to high-pressure industrial environments. However, for a check valve to function correctly, it must be free of debris and buildups that can obstruct its operation.
Through rigorous fieldwork and constant monitoring, the significance of cleaning and maintaining check valves becomes evident. Neglecting this essential maintenance task can result in valve failures, leading to reverse flow which, in turn, can cause cross-contamination in industrial processes or damage to expensive system components. My expertise in troubleshooting and system optimization has revealed that regular cleaning of check valves not only prevents these adverse outcomes but also enhances the entire system's reliability and efficiency.
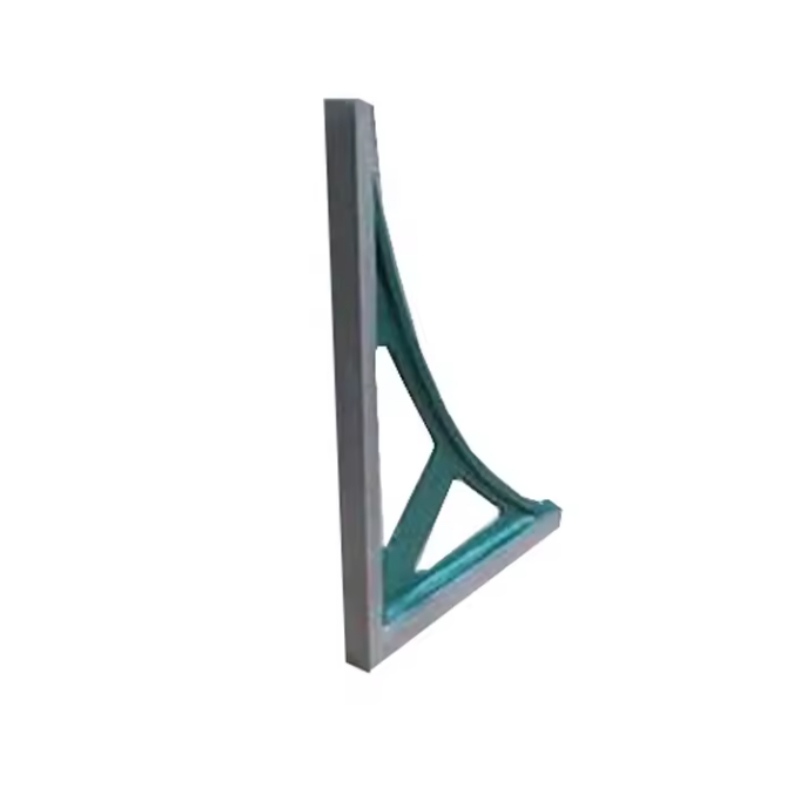
Cleaning a check valve requires a meticulous approach. Start by isolating the valve from the system to prevent any leaks or spills during the cleaning process. Often, it's beneficial to refer to manufacturer guidelines to ensure specific cleaning methods and solvents are compatible with your particular valve materials. Employing the right techniques and tools is crucial – ultrasonic cleaning, for instance, is effective for removing tough deposits and residues without damaging the valve's internal components.
clean check valve
It's noteworthy that different types of check valves, such as swing check, lift check, or ball check valves, may require distinct cleaning protocols. Expertise in these variations contributes to a more efficient maintenance routine. In numerous instances, clients in industrial sectors have reported reductions in maintenance costs and improvements in system performance following a structured cleaning regimen for their check valves.
Establishing a regular cleaning schedule is key, and it enhances trustworthiness in system operations. This proactive approach not only ensures the smooth functioning of the check valves but also extends their lifespan, offering substantial savings in replacement costs over time. Sharing real-world successes, like a client who reduced downtime by over 30% with a quarterly valve cleaning protocol, reinforces the authority of this practice.
Moreover, for organizations emphasizing sustainability, clean check valves contribute to reduced energy consumption by ensuring systems operate at peak efficiency. This aligns with broader environmental goals and demonstrates a commitment to corporate responsibility, thus boosting reputational trust in the market.
In conclusion, while a clean check valve may seem a minor component, its influence on system integrity and efficiency is significant. By integrating proper cleaning practices based on thorough expertise, professionals can ensure that these valves continue to perform their critical roles effectively. As a result, industries can avoid costly disruptions, optimize their operations, and gain a competitive edge through reliability and enhanced performance.