Understanding the Critical Role of a 600mm Butterfly Valve in Industrial Applications
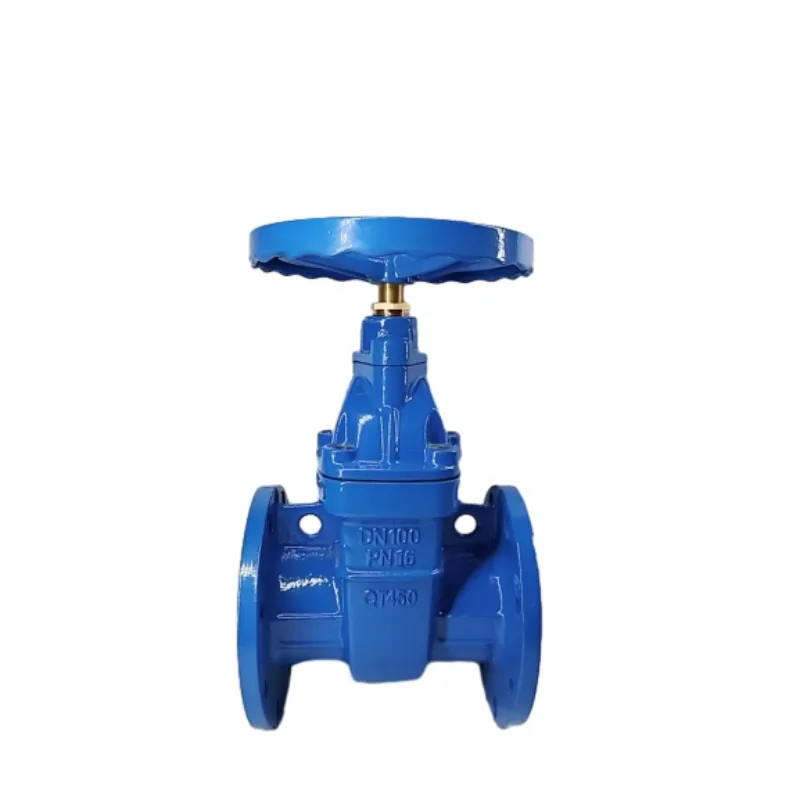
In the dynamic world of industrial machinery, the 600mm butterfly valve stands out as a pivotal component, offering unmatched functionality and efficiency. As industries increasingly prioritize seamless operation and minimal downtime, the demand for reliable equipment has never been more pressing. The 600mm butterfly valve meets these needs by ensuring excellent flow control, operational safety, and durability, making it indispensable across various sectors ranging from water treatment to petrochemical processing.
A 600mm butterfly valve is essentially a flow-regulating device that utilizes a rotating disc to start, stop, and modulate fluid flow through a system. One of its crowning features is the simple yet effective design, which not only reduces the valve's profile inside piping systems but also ensures quick operation. This in-line functionality is paired with the valve's lightweight structure, making it cost-effective compared to other alternatives such as gate or globe valves. The 600mm variant, with its optimal diameter, is particularly suited for handling substantial flow rates without compromising on control precision.
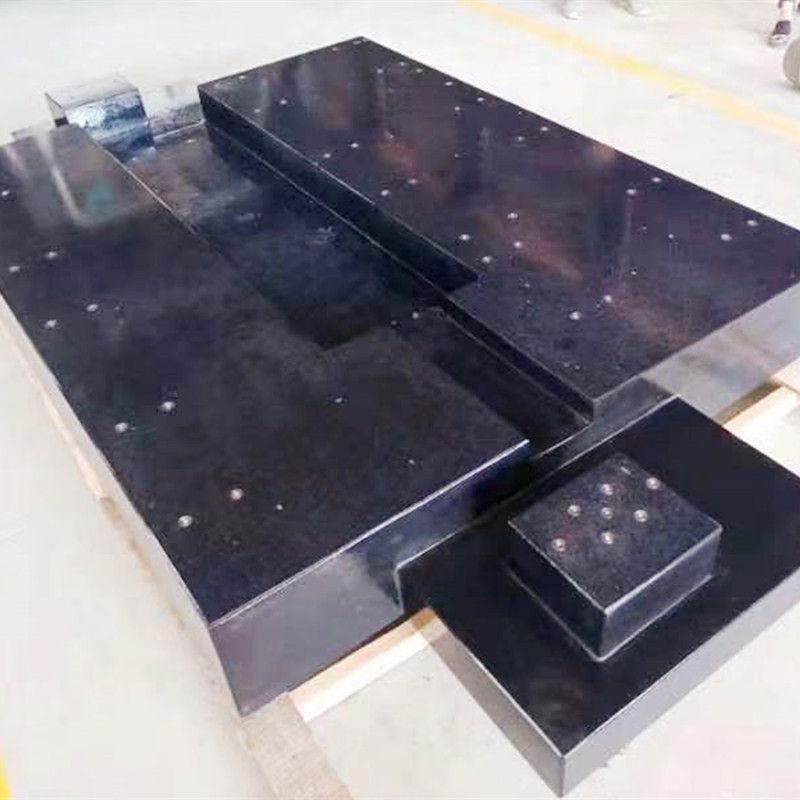
The expertise behind the 600mm butterfly valve lies in its material composition and engineering. Typically composed of cast or ductile iron, stainless steel, or high-grade carbon steel, the valve is built to withstand high pressures and corrosive environments. This engineering excellence extends to the valve’s sealing technology. With elastomer liners or resilient-seated options, the valve ensures a tight seal, thereby minimizing leakage risks and enhancing safety. In environments where reliability is non-negotiable, such as chemical processing plants or municipal water systems, these features are not just desirable but essential.
600mm butterfly valve
Authoritativeness in context comes from the valve's widespread adoption and endorsement across infrastructure projects worldwide. Industry titans and governmental entities often opt for butterfly valves, specifically the 600mm variant, due to positive past performance metrics and peerless adaptability. As an example, major waterworks upgrade projects often list this valve as a specification due to its ability to handle various fluid types under diverse operational conditions—demonstrating its robustness and versatility.
Trustworthiness also extends from the continual innovation in the valve design. Manufacturers frequently incorporate advances in material sciences and fluid dynamics to refine the operation and longevity of the valve. Consider enhancements in the elastomer compounds used in seals, which are now more resistant to a wider range of chemical compositions, thus extending the service life of valves in aggressive environments.
Real-world experience solidifies trust in the 600mm butterfly valve. Operators report less frequent maintenance needs compared to other valve types, leading to cost savings and reduced operational disruptions. The simplicity of its structure translates to easier, less costly retrofitting and servicing. Moreover, the ability to control large volumes of fluid with a minimal pressure drop is a recurrent theme in industry feedback, particularly within systems that require consistent flow rates over extended distances.
In conclusion, the 600mm butterfly valve is not just a mechanical component—it is a proven solution aligned with modern industry demands for efficiency, reliability, and security. From expert engineering to authoritative use cases, its role in industrial settings is both foundational and forward-looking. Those engaged in selecting infrastructure components should consider these valves a critical investment, ensuring not only immediate operational efficiency but also long-term economic benefits.