In the diverse and intricately technical world of industrial applications, a check valve assembly plays a pivotal role. With multifaceted utilization across various sectors, understanding the intricacies of check valve assemblies is imperative for ensuring optimal performance and long-term reliability in your equipment.
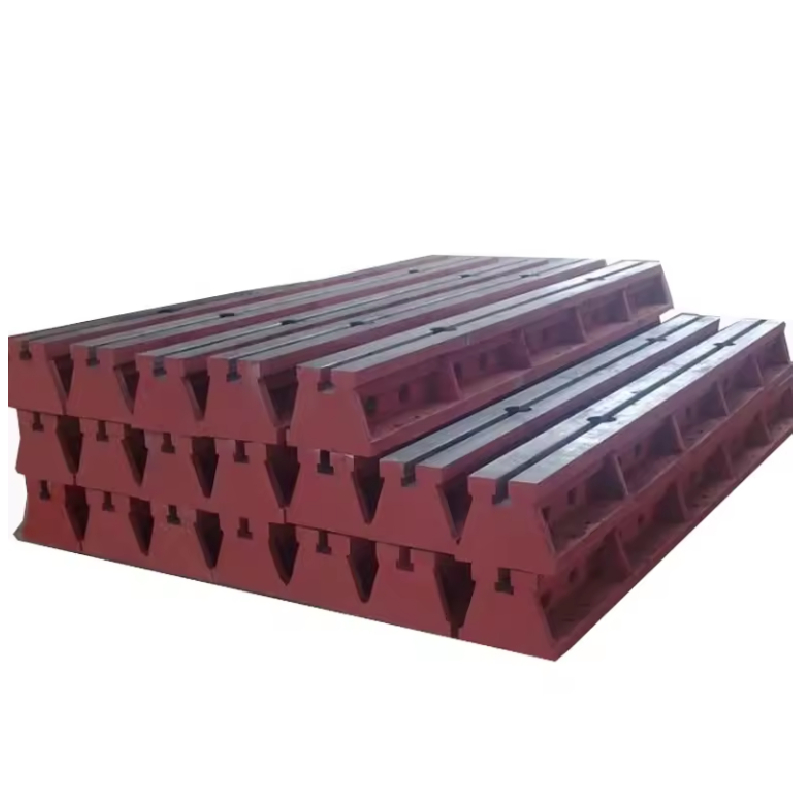
Check valve assemblies are engineered to permit fluid (liquid or gas) to flow in one direction while preventing reverse flow. This functionality is crucial in maintaining system stability, preventing potential damage, and ensuring efficient operation. The design and material selection of a check valve assembly significantly impact its effectiveness, reliability, and lifespan, and thus necessitate in-depth expertise for selection and maintenance.
Professionals in the field of fluid dynamics understand the criticality of choosing the appropriate type of check valve assembly based on application requirements. The applications range from low-pressure fluid systems to high-pressure hydraulic systems, and each has its unique demands. Ball check valves, for example, are often used for pumping systems and gas lines, benefiting systems where there’s low back-pressure. Disc check valves, on the other hand, find their niche in high-flow applications due to their robust, reliable performance in managing backflow.
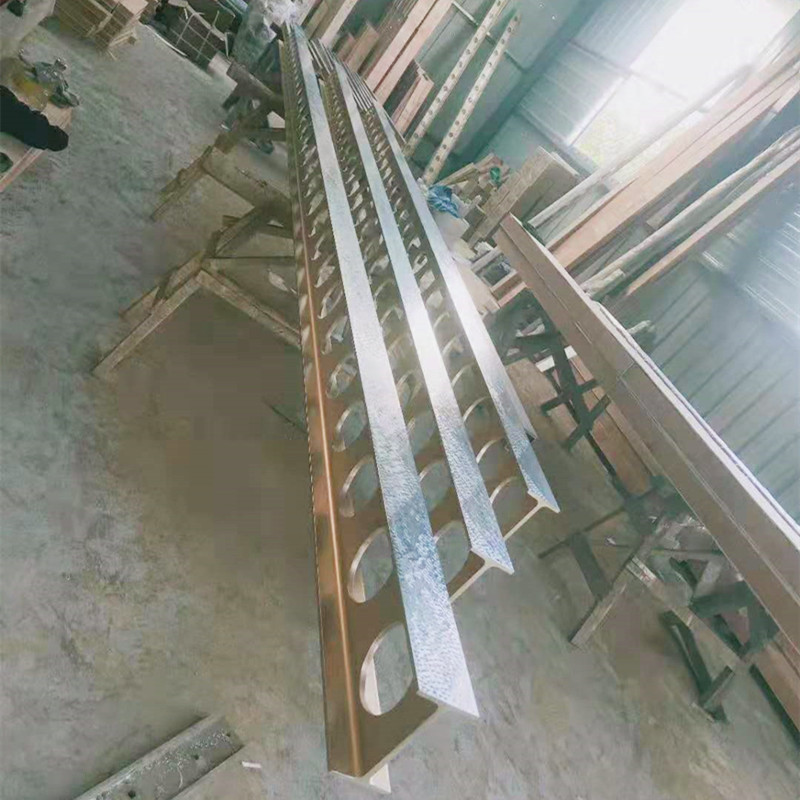
Expertise dictates that selecting the right material for a check valve assembly is not merely about durability, but rather about compatibility with the fluid or gas it controls. Stainless steel assemblies are often favored in corrosive environments due to their resistance to degradation, while plastic assemblies may be employed in areas where weight constraints and chemical compatibility are considerations.
For industry stalwarts,
the installation of a check valve assembly is as critical as its selection. Improper installation can lead to system inefficiencies or catastrophic failures. Ensuring the valve is installed in the correct orientation, according to the specific system’s flow path, and conducting thorough pressure testing pre- and post-installation are steps that cannot be overlooked. Adhering to manufacturers’ specifications and guidelines guarantees the optimal performance of the valve, thereby extending its service life.
check valve assy
Establishing trustworthiness in the lifespan of check valve assemblies comes from rigorous testing and validation. Each component undergoes comprehensive assessments to ascertain performance under varying conditions – from temperature and pressure fluctuations to chemical exposure. Leading manufacturers often adhere to stringent international standards such as ISO or API, ensuring that their assemblies can handle the harshest conditions without compromising system integrity.
Conducting regular maintenance checks, which include inspecting the valve seat for wear and ensuring no debris obstructs the valve’s operation, enhances the longevity of the system. Engineering professionals emphasize predictive maintenance strategies that anticipate wear and replacement schedules, thus reducing unexpected downtimes and maintaining system efficiency.
In scenarios involving specialized industries such as pharmaceuticals or food processing, where cleanliness and contamination control are of paramount importance, check valve assemblies with enhanced sanitary features are employed. These assemblies are designed to facilitate easy cleaning, often employing features such as quick disassembly and the use of materials that resist microbial growth.
An authoritative perspective in the field leverages years of experience in specifying check valve assemblies that optimize both performance and cost. By precisely aligning valve specifications with operational demands, potential issues such as water hammer, pressure losses, and flow restrictions can be mitigated. Industry experts frequently undergo continuous education to stay abreast of the latest developments in valve technology, ensuring they are equipped with cutting-edge solutions that leverage advancements in materials science and fluid dynamics.
In summary, the choice, installation, and maintenance of a check valve assembly demand a confluence of detailed technical knowledge and practical experience. A thorough comprehension of system requirements, combined with a strategic approach to component selection, ensures that each check valve assembly performs effectively, enhancing the overall efficiency, safety, and reliability of industrial systems. For professionals seeking to optimize their fluid management systems, partnering with knowledgeable manufacturers and employing thorough inspection and maintenance protocols remain crucial steps towards achieving desired operational outcomes.